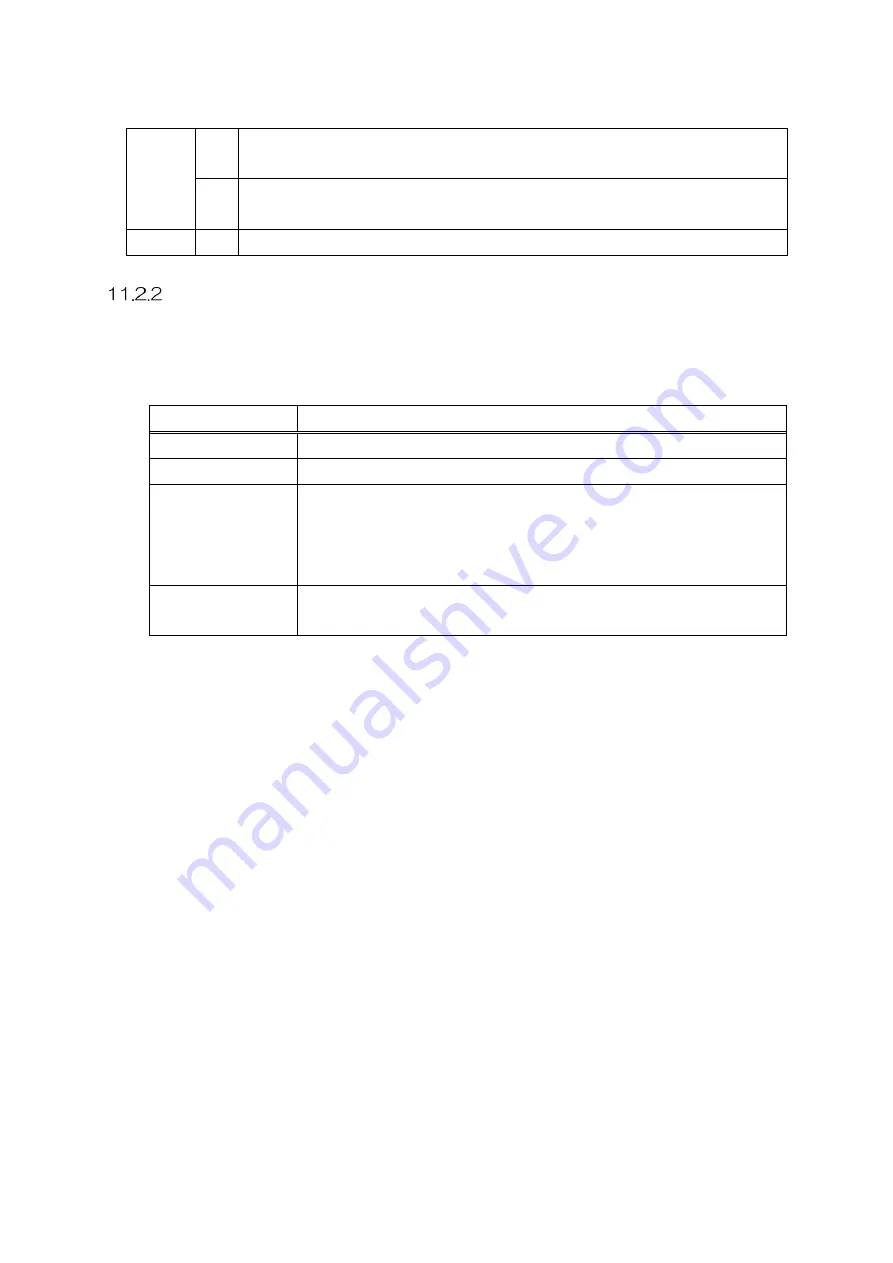
67
Power
◎
Displays the powers detected with the built-in or external CT, external PT,
and conversion board.
●
Displays the powers detected with the external CT, external PT, and
conversion board.
―
Displays nothing.
Feedback control
This function performs feedback control using detected values. Mode can be set by display
panel. The related parameters are shown below.
F400: Feedback control method
The selectable modes differ according to the connected conversion board.
Model
Mode selectable with F400
UG-TB1A
0: No feedback, 1: Constant current control
UG-TB1V
0: No feedback, 2: Constant voltage control
UG-TB3
UG-TB3H
UG-TB3U
UG-TB3HU
0: No feedback, 1: Constant current control
2: Constant voltage control, 3: Constant power control
UG-TB4
UG-TB4H
0: No feedback, 3: Constant power control
※
If only [0: No feedback] can be selected on the setting screen, the conversion board
may not be connected correctly. Check if the model is displayed with [F408:
Conversion board model check].
※
This parameter needs to be set again after the conversion board is removed and
installed again for replacement or other purposes. If you start operation without
setting the mode again, this function may fail to operate correctly.
Summary of Contents for CALPOTE UG Series
Page 94: ...94 APPENDIX B PANEL TRANSITION DIAGRAM...
Page 96: ...MEMO...