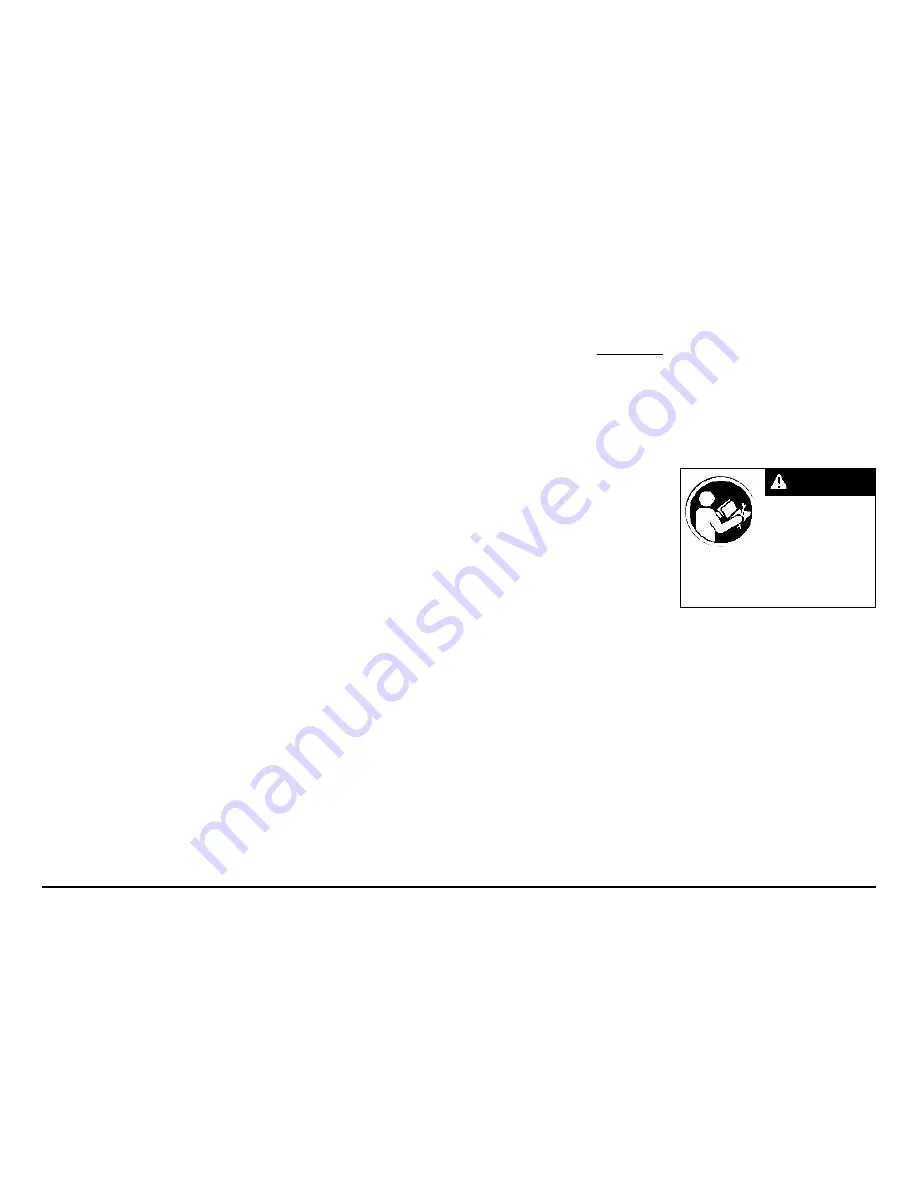
520-202-000
9/03
Model S20 Non-Metallic Design Level 2 Page 15
RuppGUARD™ FOR VIRGIN PTFE
EQUIPPED PUMPS CONCEPT
The spill prevention option prevents
the air end components from being
contaminated or damaged when a
pumping diaphragm ruptures while
pumping caustic or toxic materials. It
also helps to protect the environment.
With the installation of optional leak
detectors (either mechanical or
electronic) the diaphragm rupture can be
detected. The pump can then be shut
down and repaired before any caustic or
toxic materials can enter the air end and
be exhausted into the surrounding
environment.
RuppGUARD™ OPTION
DIAPHRAGM SERVICING
To service the diaphragms first shut
off the suction, then shut off the
discharge lines to the pump. Next shut
off the compressed air supply, bleed the
pressure from the pump, and disconnect
the air supply line from the pump. Drain
any remaining pumped liquid from the
pump. Remove the pump before
servicing.
Next, drain the fluid from the spill
prevention chambers. This can be done
by removing the bottom plug (item 53)
from each spill prevention chamber.
After the fluid from the spill
prevention chambers has been drained,
the wet end components can now be
removed. See diaphragm servicing
section for detailed instructions. The spill
prevention option has two additional
virgin PTFE pumping diaphragms (item
48). These diaphragms are installed with
the natural
concave
curve toward the
outer chamber (items 17 from the pump
assembly drawing). The molded
directional arrows on the diaphragms
must point vertically.
FILLING RuppGUARD™ CHAMBERS
WITH LIQUID
THE CHAMBERS ARE FILLED
WITH WATER AT THE FACTORY.
If you prefer to substitute another
liquid, to prevent system contamination
consult the factory first to determine
compatibility of the substitute with pump
construction.
Follow the steps listed here to replace
the liquid in the pump after disassembly
or liquid loss:
1. Drain the fluid in the spill prevention
chambers by removing the bottom two
boss plugs (items 53). Replace the
bottom two boss plugs after the fluid is
drained.
2. Remove the eight capscrews (item
10) fastening the discharge manifold and
elbows to the outer chambers (items 17).
The discharge manifolds and elbows can
now be removed.
3. Remove the top two boss plugs
(items 53). The spill prevention
chambers are filled through the exposed
ports.
4. Apply air pressure to the air
distribution valve. Install safety clip (item
1-N) into the smaller unthreaded hole in
one end cap (item 1-D). This locks the
valve spool to one side, keeping the
pump from shifting.
5. Face the side of the pump with
the installed safety clip. If the safety clip
is installed in the top end cap, fill the
left spill containment chamber. If the
safety clip is installed on the bottom end
cap, fill the right spill prevention chamber.
The volume of fluid is 1420 ml (48.01 fl.
oz.). It is important that the exact amount
of fluid is used. Too little or too much
fluid causes premature diaphragm
failure and erratic pumping.
6. Loosely reinstall one boss plug
(item 53) to the filled spill prevention
chamber.
7. Shut off air supply. Remove safety
clip. Adjust the air line regulator so that
air pressure slowly fills the pump. The
diaphragm expands, forcing the fluid in
the chamber to be slowly displaced.
When the pump shifts to the opposite
side, quickly install the safety clip.
8. Loosen the top boss plug on the
filled chambers. This allows fluid in the
chamber to purge trapped air from the
chamber. This can be seen by watching
the column of fluid in the sight tube. When
fluid appears at the top of the port,
quickly tighten the boss plug. Fluid loss
of 1 to 2ml is acceptable.
9. Tilt the pump so the uppermost
pipe tee (item 56) is in the vertical
position. Loosen the pipe plug (item 52).
This will allow trapped air to purge
through the pipe tee. When fluid appears
at the tee opening, reinstall the pipe
plug.
NOTE:
If all air is not purged using
this procedure, remove the check valve
components from the top port of the outer
chamber (item 17). Apply manual
pressure to the pumping diaphragm by
inserting a blunt instrument into the top
port of the outer chamber and applying
pressure to the diaphragm. Loosen the
pipe plug (item 52) allowing the fluid to
Read these instructions
completely, before in-
stallation and start-up. It
is the responsibility of
the purchaser to retain
this manual for reference. Failure to
comply with the recommendations stated
in this manual will damage the pump, and
void factory warranty.
IMPORTANT
purge any remaining trapped air.
Reinstall the plug.
10. Repeat steps 5 through 9 to fill
opposite spill prevention chamber.
11. Reinstall the check valve
components, discharge manifold and
elbows to the pump. The pump is now
ready for operation.
Summary of Contents for S20
Page 2: ......