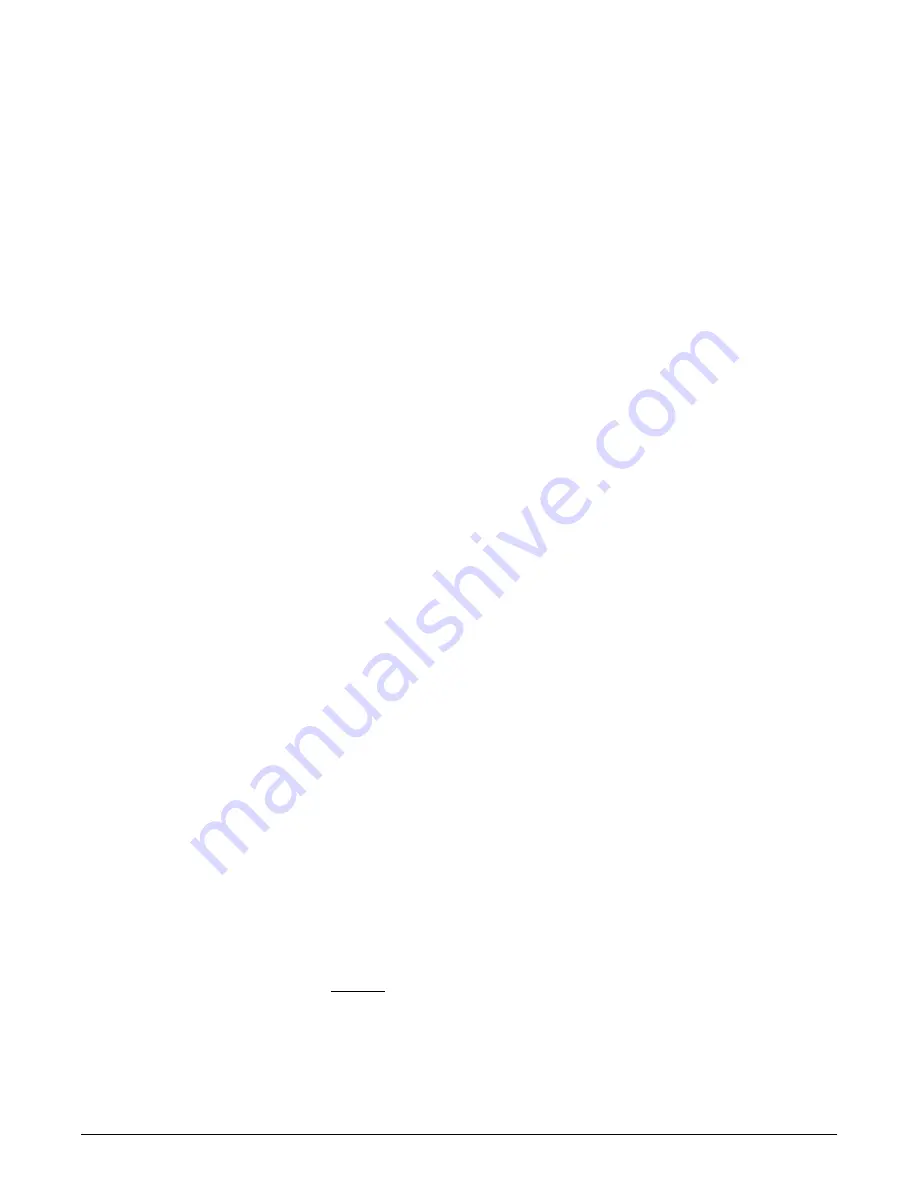
hdf2dl6sm-rev0316
Model HDF2 Page 6
A NOTE ABOUT AIR VALVE LUBRICATION
The SANDPIPER pump’s pilot valve and main air valve assemblies are designed to
operate WITHOUT lubrication. This is the preferred mode of operation. There may be
instances of personal preference, or poor quality air supplies when lubrication of the com-
pressed air supply is required. The pump air system will operate with
properly lubricated compressed air supplies. Proper lubrication of the compressed air
supply would entail the use of an air line lubricator (available from Warren Rupp) set to
deliver one drop of 10 wt., non-detergent oil for every 20 SCFM of air the pump consumed
at its point of operation. Consult the pump’s published Performance Curve to
determine this.
It is important to remember to inspect the sleeve and spool set routinely. It should
move back and forth freely. This is most important when the air supply is lubricated. If a
lubricator is used, oil accumulation will, over time, collect any debris from the compressed
air. This can prevent the pump from operating properly.
Water in the compressed air supply can create problems such as icing or
freezing of the exhaust air causing the pump to cycle erratically, or stop operating. This
can be addressed by using a point of use air dryer to supplement a plant’s air drying
equipment. This device will remove excess water from the compressed air supply and al-
leviate the icing or freezing problem.
ESADS+PLUS:
EXTERNALLY SERVICEABLE AIR DISTRIBUTION SYSTEM
Please refer to the exploded view drawing and parts list in the Service Manual supplied
with your pump. If you need replacement or additional copies, contact your local Warren
Rupp Distributor, or the Warren Rupp factory Literature Department at the number shown
below. To receive the correct manual, you must specify the MODEL and TYPE information
found on the name plate of the pump.
MODELS WITH 1" SUCTION/DISCHARGE OR LARGER, AND
METAL CENTER SECTIONS:
The main air valve sleeve and spool set is located in the valve body mounted on the
pump with four hex head capscrews. The valve body assembly is removed from the pump
by removing these four hex head capscrews.
With the valve body assembly off the pump, access to the sleeve and spool set is
made by removing four hex head capscrews (each end) on the end caps of the valve body
assembly. With the end caps removed, slide the spool back and forth in the sleeve. The
spool is closely sized to the sleeve and must move freely to allow for proper pump opera-
tion. An accumulation of oil, dirt or other contaminants from the pump’s air supply, or from
a failed diaphragm, may prevent the spool from moving freely. This can cause the spool to
stick in a position that prevents the pump from operating. If this is the case, the sleeve and
spool set should be removed from the valve body for cleaning and further inspection.
Remove the spool from the sleeve. Using an arbor press or bench vise (with an impro-
vised mandrel), press the sleeve from the valve body. Take care not to damage the sleeve.
At this point, inspect the o-rings on the sleeve for nicks, tears or abrasions. Damage of this
sort could happen during assembly or servicing. A sheared or cut
o-ring can allow the pump’s compressed air supply to leak or bypass within the air valve
assembly, causing the pump to leak compressed air from the pump air exhaust or not
cycle properly. This is most noticeable at pump dead head or high discharge pressure
conditions. Replace any of these o-rings as required or set up a routine, preventive main-
tenance schedule to do so on a regular basis. This practice should include cleaning the
spool and sleeve components with a safety solvent or equivalent, inspecting for signs of
wear or damage, and replacing worn components.
To re-install the sleeve and spool set, lightly lubricate the o-rings on the sleeve with an
o-ring assembly lubricant or lightweight oil (such as 10 wt. air line lubricant).
Re-install one end cap, gasket and bumper on the valve body. Using the arbor press or
bench vise that was used in disassembly, carefully press the sleeve back into the valve
body, without shearing the o-rings. You may have to clean the surfaces of the valve body
where the end caps mount. Material may remain from the old gasket. Old material not
cleaned from this area may cause air leakage after reassembly. Take care that the bumper
stays in place allowing the sleeve to press in all the way. Reinstall the spool, opposite end
cap, gasket and bumper on the valve body. After inspecting and cleaning the gasket sur-
faces on the valve body and intermediate, reinstall the valve body on the pump using new
gaskets. Tighten the four hex head capscrews evenly and in an alternating cross pattern.