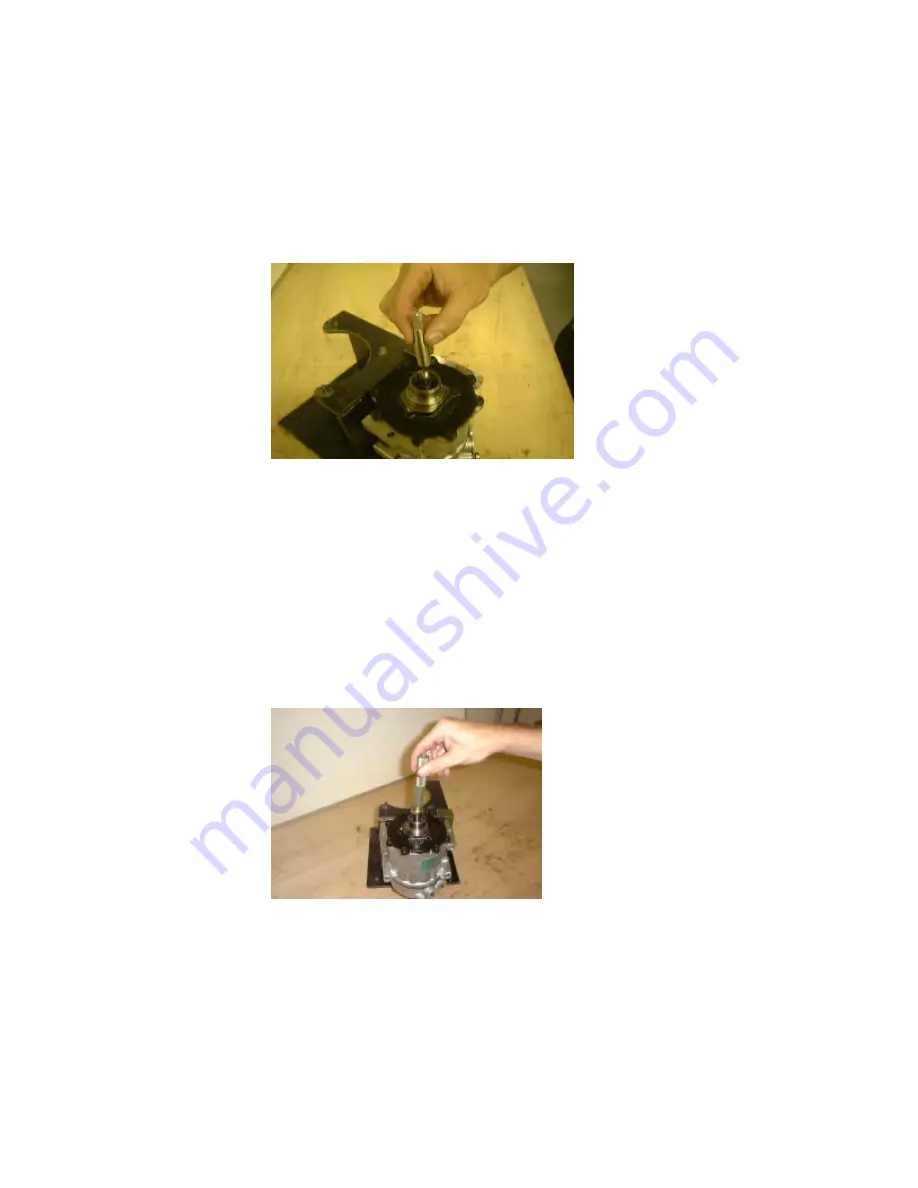
SD7H15 Type C Service Manual
Prepared July 1999 – Application Engineering
12
Service Operations – Shaft Seal
6.
Place shaft seal protector sleeve over compressor shaft. Inspect the sleeve
to ensure that it has no scratches and is smooth so that the lip seal will not
be damaged. Make sure there is no gap between the end of the sleeve and
the seal surface of the shaft (Fig.17).
Fig.17 Protector sleeve fitting
7.
Engage the lips of the seal removal and installation tool with the slots in
the new lip seal housing. Make sure the lip seal assembly, especially the
O-ring is clean. Dip the entire lip seal assembly, on the tool, into clean
refrigerant oil. Make sure the seal assembly is completely covered with
oil.
8.
Install the lip seal over shaft and press firmly to seat. Twist the tool in the
opposite direction to disengage it from the seal and withdraw the
tool.(Fig.18)
Fig.18 Replacement of lip seal
9.
Reinstall shaft seal snap ring with internal snap ring pliers. Bevelled side
should face up. (Away from the compressor body). Ensure that the snap
ring is completely seated in the groove.
10.
Tap new felt ring assembly into place.
11.
Reinstall clutch assembly as detailed in section A.