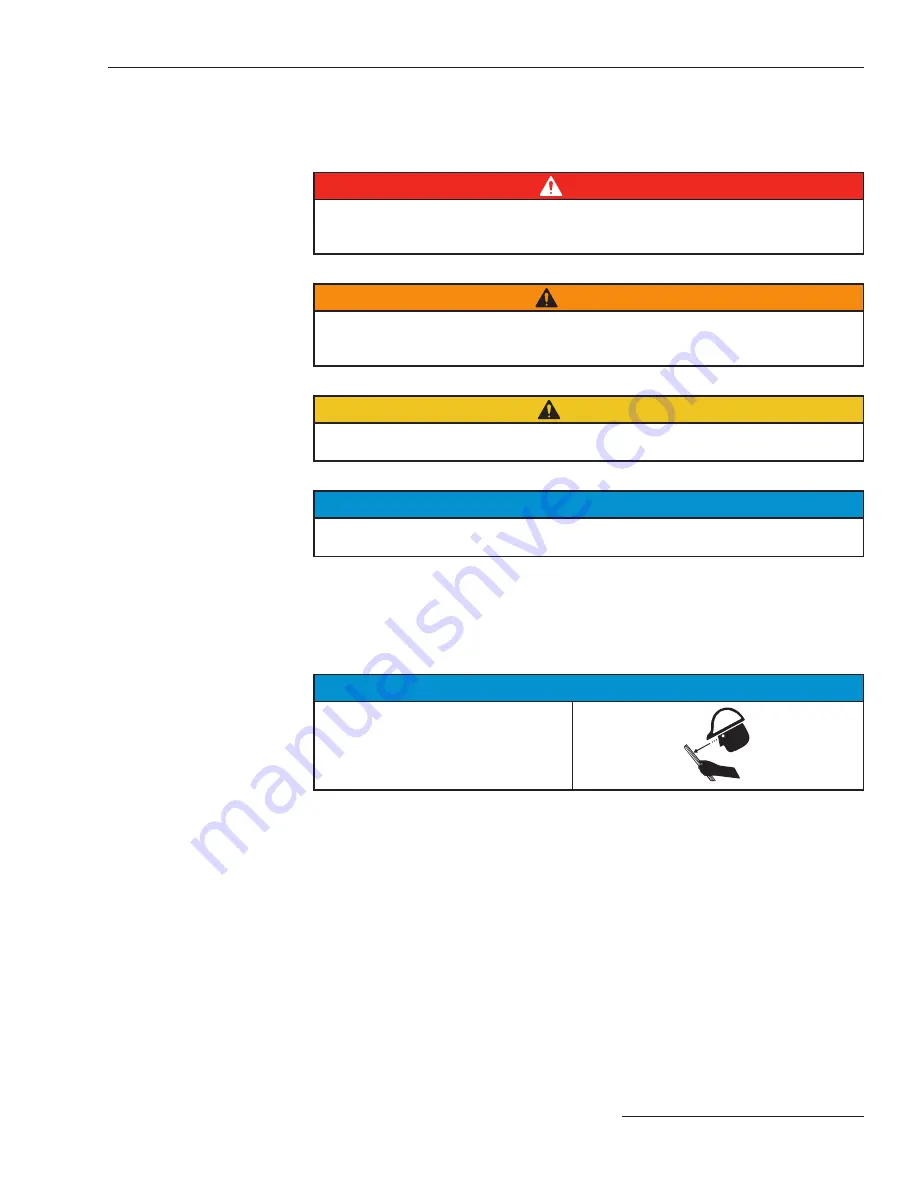
Understanding
Safety-Alert
Messages
Several types of safetyalert messages may appear throughout this instruction sheet and
on labels attached to the S&C Overcurrent Control. Famil iarize yourself with these types
of messages and the importance of these various signal words:
DANGER
“DANGER” identifies the most serious and immediate hazards that
will likely
result in serious personal injury or death if instructions, including recommended pre-
cautions, are not followed .
WARNING
“WARNING” identifies hazards or unsafe practices that
can
result in serious per-
sonal injury or death if instructions, including recommended precautions, are
not followed .
CAUTION
“CAUTION” identifies hazards or unsafe practices that
can
result in minor
personal injury if instructions, including recommended precau tions, are not followed .
NOTICE
“
NOTICE
” identifies important procedures or requirements that
can
result in product or
property damage if instructions are not followed .
Following Safety
Instructions
If you do not understand any portion of this instruction sheet and need assistance,
contact your nearest S&C Sales Office or S&C Authorized Distributor. Their tele
phone numbers are listed on S&C’s website
sandc.com
. Or call the S&C Global Monitoring
and Support Center at 18884561100.
NOTICE
Thoroughly and carefully read this
instruction sheet before programming
your S&C Overcurrent Control .
Replacement
Instructions
and Labels
If you need additional copies of this instruction sheet, contact your nearest S&C Sales
Office, S&C Headquarters, or S&C Electric Canada Ltd.
It is important that any missing, damaged, or faded labels on the equipment be
replaced immediately. Replacement labels are available by contacting your nearest S&C
Sales Office, S&C Headquarters, or S&C Electric Canada Ltd.
Safety Information
S&C Instruction Sheet 695-515
3
Summary of Contents for Vista SD
Page 34: ......