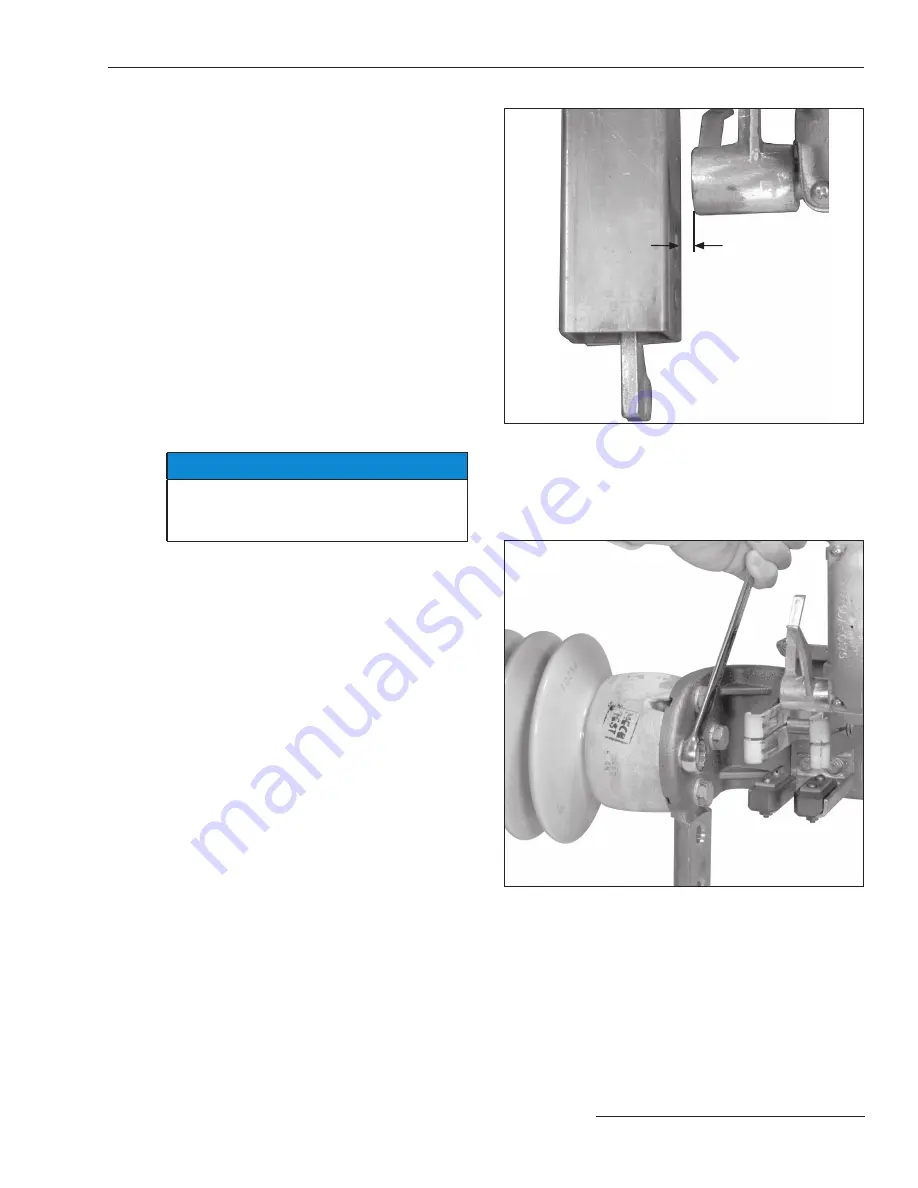
S&C Instruction Sheet 761-507
23
Installation
(g) Move the blade assembly slowly toward the
Closed
position until the blade assembly is
under the interrupter lever shaft. Verify the gap
between the end of the interrupter lever shaft
and the blade assembly is between and
3∕16
-
inch
(5 mm) and
9�32
-inch (7 mm). See Figure 36.
(h) If the conditions described above are not met,
adjust as follows. Loosen the four
½
-inch–13
×
1
¼
-inch hex-head galvanized steel cap screws
that fasten the terminal base castings to the
stationary insulators. See Figure 37. Shift the
terminal base castings as required. Tighten the
cap screws and recheck for conformance to the
conditions outlined above. Readjust if required.
Make certain the cap screws are tightened to
fi nal tightness (55 ft.-lb.).
If any of the conditions described in this step
cannot be achieved, contact the nearest S&C
Sales Office because it is likely damage was
sustained during shipment.
NOTICE
Stationary contacts are greaseless and
self-lubricating .
Do not apply lubricant to
the stationary contacts .
Connecting High-Voltage Conductors
When high-voltage conductors are to be connected
using aluminum-alloy body connectors
●
the following
procedures should be used:
(a) Thoroughly wire-brush the current-transfer
surfaces of each connector and immediately
apply a liberal coating of Penetrox® A (available
from Burndy Corporation) to the brushed
surfaces.
(b) Wire-brush each terminal pad of the interrupter
switch and apply a coating of Penetrox A. Then
bolt the connectors to the terminal pads.
(c) Prepare the conductors using established
procedures and clamp them in their respec tive
connectors.
●
(“Mass anode”-type connectors, such as the catalog number 6300
series offered by S&C, that have been designated by the connector
manufacturer as being suitable for direct attachment to copper bearing
alloy terminal pads .
Figure 36. Verifying the gap between the end of the interrupter
lever shaft and the blade assembly.
Figure 37. Adjusting the position of the terminal base casting.
3∕16
-inch (5 mm) min,
9/32
-inch (7 mm) max