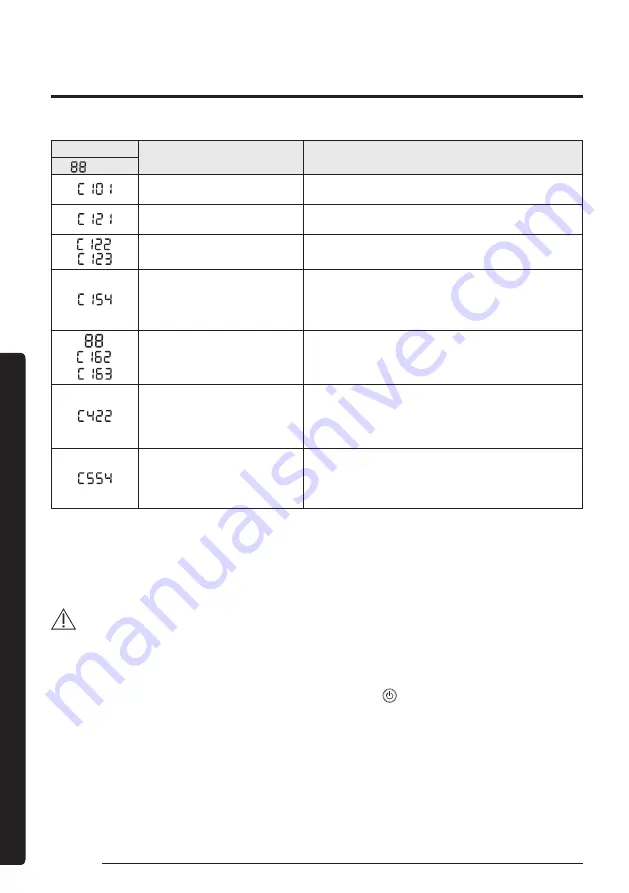
28
Installation Inspection and Testing
English
Instal
lation
Step 4-8 Performing final checks and
trial operation
WARNING
Stop the unit, disconnect the power, and contact Samsung
technical support if any of the following occurs:
•
The unit produces a burning smell or smoke.
•
The power cable is hot or damaged.
•
The unit is very noisy.
•
Any foreign substance, such as water, has entered the
appliance.
•
The appliance becomes flooded.
1
Check the following:
‐
Strength of the installation site
‐
Tightness of pipe connection to detect gas leak
‐
Electric wiring connection
‐
Heat-resistant insulation of the pipe
‐
Drainage
‐
Grounding conductor connection
‐
Correct operation (Take the following steps.)
2
Press the (Power) button on the remote control to
check the following:
‐
The indicator on the indoor unit lights up.
‐
The airflow blade opens and the fan gears up for
operation.
Error indicator
Error
Measures for the installer to take
Display
Communication error between
indoor and outdoor units
•
Check the cables between the indoor and outdoor units.
See if the power cable or communication cable is crossed.
Error on indoor temperature sensor
•
Make sure that the indoor temperature sensor is properly
connected.
,
Error on indoor heat exchanger
•
Make sure that the evaporator temperature sensor is
properly connected.
Error on indoor fan motor
•
Make sure that the evaporator motor is properly
connected to the board.
•
Check for a foreign substance inside the unit that may be
preventing the blower wheel from turning.
,
,
EEPROM/Option error
•
Reset the option codes.
Refrigerant flow blocking error
•
Make sure that the service valves are completely open.
•
Check for any blockage in the refrigerant pipe that
connects the indoor and outdoor units.
•
Check for refrigerant leaks.
Lack of refrigerant (for inverter
models only)
•
Make sure a sufficient amount of refrigerant has been
added for a pipe that is longer than 7.5 m.
•
Check for refrigerant leaks between the valve and pipe
connection.
Summary of Contents for AR TXFY Series
Page 32: ......