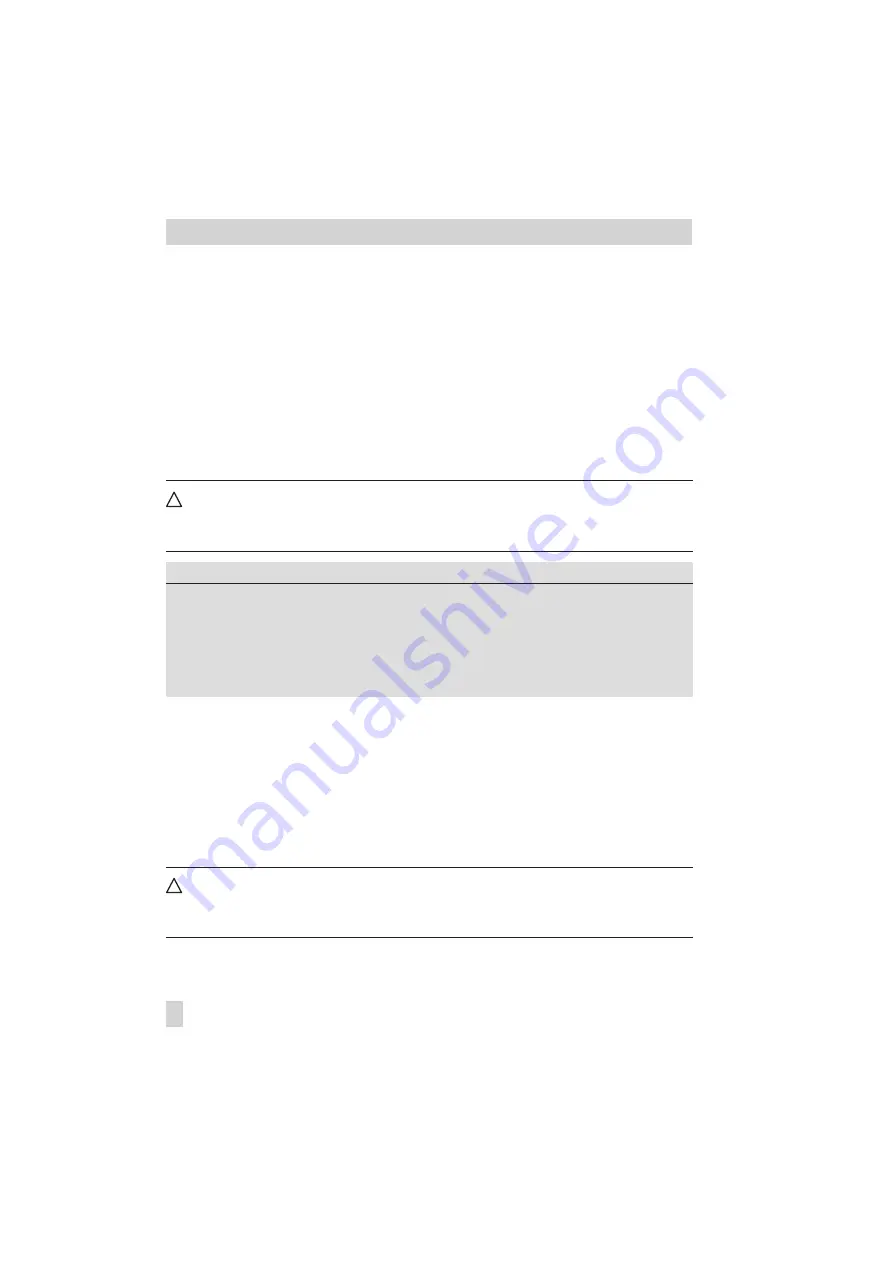
Modbus slave interface
in combination with RS-232/RS-485 cable converters (for four-wire bus)
Operating the PLC in combination with cable converters requires a permanent bus connec-
tion (data cable). The bus line links the devices/control units in an open ring. At the end of
the bus line, the data cable is connected to the control station using an RS-485/RS-232 con-
verter (e.g. TROVIS 5484). The maximum extension (cable length) of the bus line is 1,200 m.
A maximum of 32 devices can be connected to such a segment. If you wish to use more than
32 devices or need to bridge greater distances, make sure repeaters (e.g. TROVIS 5482) are
installed to replicate the signal. In all, a maximum of 246 devices can be connected to a bus
line.
Caution!
Make sure that the relevant standards and regulations concerning lightning and overvoltage
protection are observed upon installation.
Parameters
*
WE
Settings level / Range of values
Station address
16-bit addressing?
Control system
monitoring
255
No
30 min
RS-232/Slave > Modbus Slave / 1 to 247, 255
RS-232/Slave > Modbus Master > Station address / Yes, No
RS-232/Slave > Modbus Slave / 1 to 300 min
Modem
Off
RS-232/Slave / Modem = Off
Baud rate
9600
RS-232/Slave / 9600, 19200
* –> Section 5.3 (Description of communication parameters to be adjusted)
5.2
Modbus master interface
Modbus instruments can be connected to the PLC using the RS-485 Modbus master interface.
The maximum bus line is 1,200 m. If you need to bridge greater distances, make sure repeaters
(e.g. TROVIS 5482) are installed to replicate the signal.
Terminals 1 and 2 are used for connection (see Fig. 4). Up to four expansion modules can also
be connected in parallel to these terminals. Refer to section 8.4.3 for more details.
Caution!
Make sure that the relevant standards and regulations concerning lightning and overvoltage
protection are observed upon installation.
20
EB 5571 EN
Communication
!
!
Summary of Contents for TROVIS 5571
Page 43: ...EB 5571 EN 43...