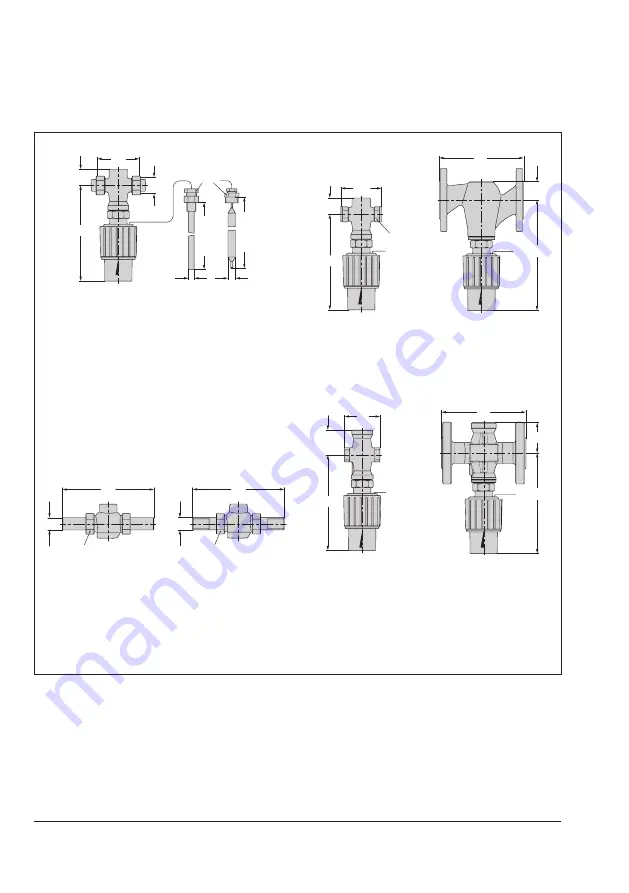
22
EB 2171 EN
Design and principle of operation
Dimensional drawings
L
185(220)
185(220)
Ø12 (19) Ø9.5 (16)
G ½
(G ¾)
R
H2
H
L
H2
H
SW
L3
H2
H
Thermowell Packing
Type 43-2
Valve with male thread and control thermostat
Type 43-1
Female thread (red brass)
Type 43-2
Flanged valve body
(spheroidal graphite iron)
L1
SW
Ød
L2
SW
A
L
H2
H
L3
H2
H
Type 43-2
with welding ends
Type 43-2
with threaded ends
Type 43-1
Female thread (stainless
steel)
Type 43-2
Flanged valve body (stainless
steel)
Fig. 5:
Dimensions