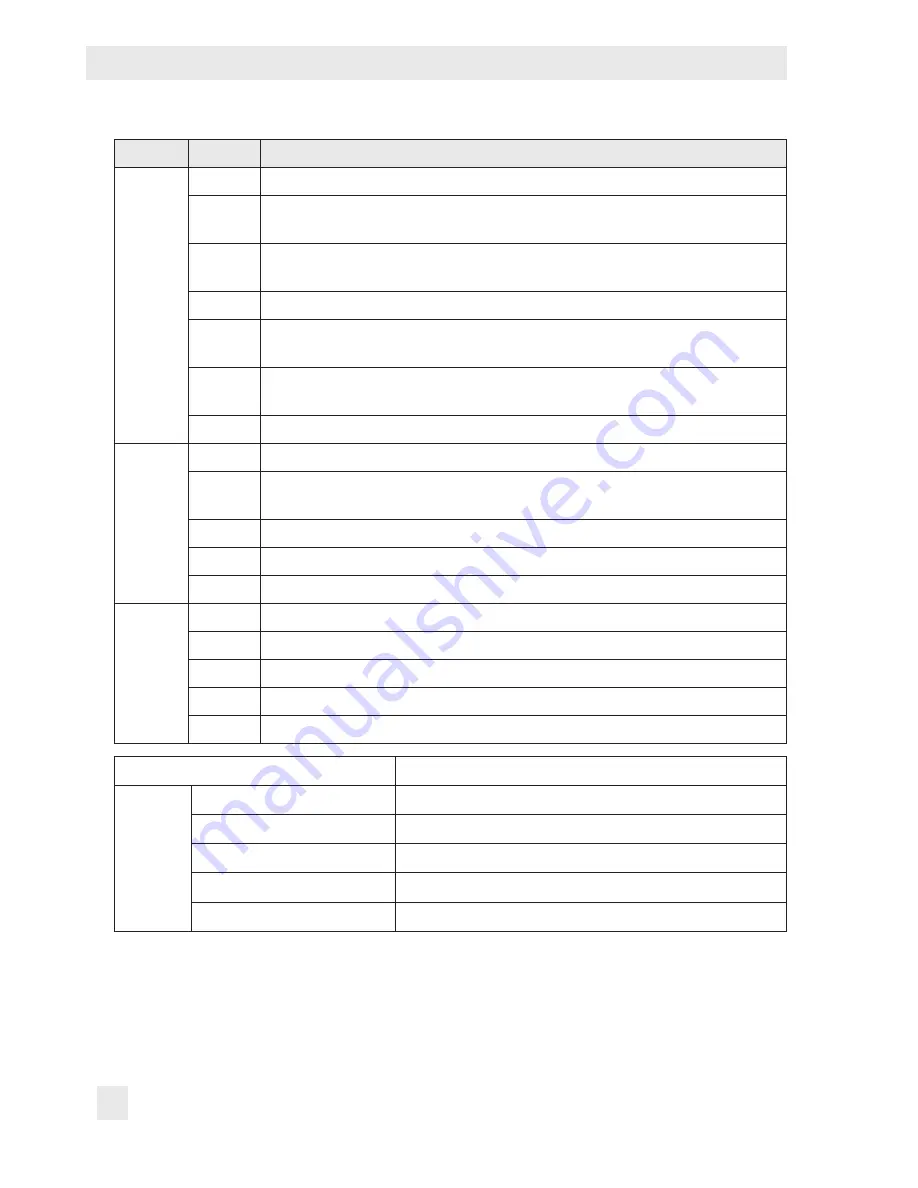
Universal commands
20
KH 8384-3 EN
Byte
Bit
Message description
27
Bit 0
Observing end position – OK
Bit 1
Observing end position – Zero point shift monotone down, average above
reference
Bit 2
Observing end position – Zero point shift monotone up, average above ref
-
erence
Bit 3
Observing end position – Zero point alternates, average above reference
Bit 4
Observing end position – Zero point shift monotone down, average below ref
-
erence
Bit 5
Observing end position – Zero point shift monotone up, average below refer
-
ence
Bit 6
Observing end position – Zero point alternates, average below reference
28
Bit 0
Positioner/valve mechanical connection – OK
Bit 1
Positioner/valve mechanical connection – No optimum travel transmission
(TEST)
Bit 2
Positioner/valve mechanical connection – Perhaps loose
Bit 3
Positioner/valve mechanical connection – Perhaps range limit
Bit 4
Positioner/valve mechanical connection – Perhaps loose (TEST)
29
Bit 0
Working range – OK
Bit 1
Working range – Mostly near closing position
Bit 2
Working range – Mostly near max. opening
Bit 3
Working range – Mostly closing position
Bit 4
Working range – Mostly max. opening
Byte
Message description
30/31
00000000
00000001
No PST performed
00000000
00000010
PST successful performed
00000000
00000100
x cancelation
00000000
00001000
Δp out cancelation
00000000
00010000
Tolerance band exceeded