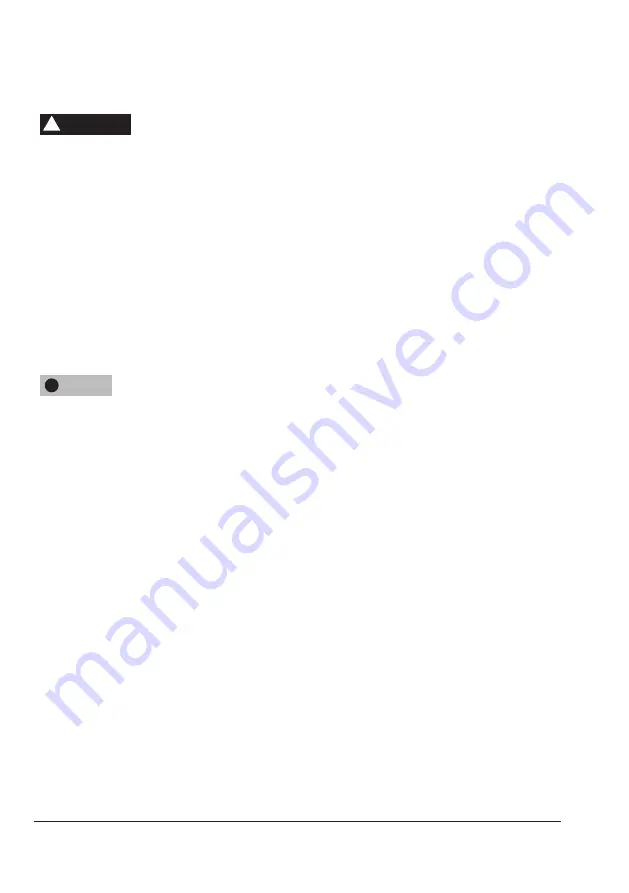
1-6
EB 8079 EN
Safety instructions and measures
WARNING
!
Risk of personal injury through incorrect operation, use or installation as a result of
information on the valve being illegible.
Over time, markings, labels and nameplates on the valve may become covered with dirt
or become illegible in some other way. As a result, hazards may go unnoticed and the
necessary instructions not followed. There is a risk of personal injury.
Î
Keep all relevant markings and inscriptions on the device in a constantly legible
state.
Î
Immediately renew damaged, missing or incorrect nameplates or labels.
1.3 Notes on possible property damage
NOTICE
!
Risk of valve damage due to contamination (e.g. solid particles) in the pipeline.
The plant operator is responsible for cleaning the pipelines in the plant.
Î
Flush the pipelines before start-up.
Risk of valve damage due to unsuitable medium properties.
The valve is designed for a process medium with defined properties.
Î
Only use the process medium specified for sizing.
Risk of leakage and valve damage due to excessively high or low tightening torques.
Observe the specified torques on tightening control valve components. Excessively tight-
ened torques lead to parts wearing out quicker. Parts that are too loose may cause leak-
age.
Î
Observe the specified tightening torques (see the 'Tightening torques, lubricants and
tools' section in the annex of these instructions).
Risk of valve damage due to the use of unsuitable tools.
Certain tools are required to work on the valve.
Î
Only use tools approved by SAMSON (see the 'Tightening torques, lubricants and
tools' section in the annex of these instructions).
Summary of Contents for 3595
Page 12: ...1 8 EB 8079 EN...
Page 32: ...4 6 EB 8079 EN...
Page 48: ...8 4 EB 8079 EN...
Page 58: ...9 10 EB 8079 EN...
Page 59: ...EB 8079 EN 9 11...
Page 60: ...9 12 EB 8079 EN...
Page 66: ...12 2 EB 8079 EN...
Page 68: ...13 2 EB 8079 EN...
Page 70: ...14 2 EB 8079 EN...
Page 74: ...15 4 EB 8079 EN...
Page 75: ......