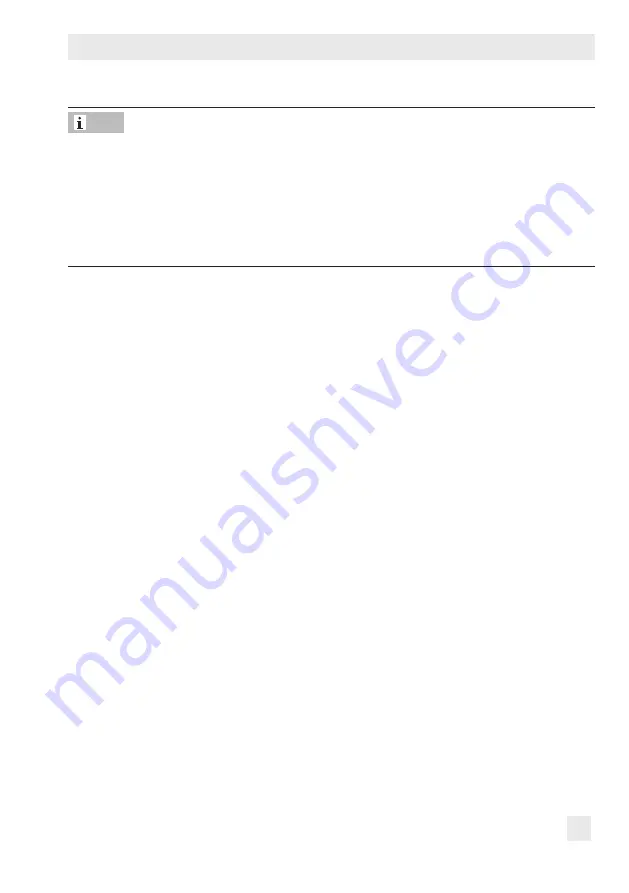
EB 8052 EN
23
Design and principle of operation
Refer to the following data sheets for more dimensions and weights:
u
T 8052 for valves with bellows seal, insulating section or heating jacket
The associated actuator documentation applies to actuators, e.g. for SAMSON pneumatic
actuators:
u
T 8310‑1 for Type 3271 and Type 3277 Actuators up to 750 cm² actuator area
u
T 8310‑2 for Type 3271 Actuator with 1000 cm² actuator area and larger
u
T 8310‑3 for Type 3271 Actuator with 1400‑60 cm² actuator area
Note
Summary of Contents for 3251
Page 11: ...EB 8052 EN 11...
Page 37: ...EB 8052 EN 37...
Page 58: ...58 EB 8052 EN...
Page 59: ...EB 8052 EN 59...