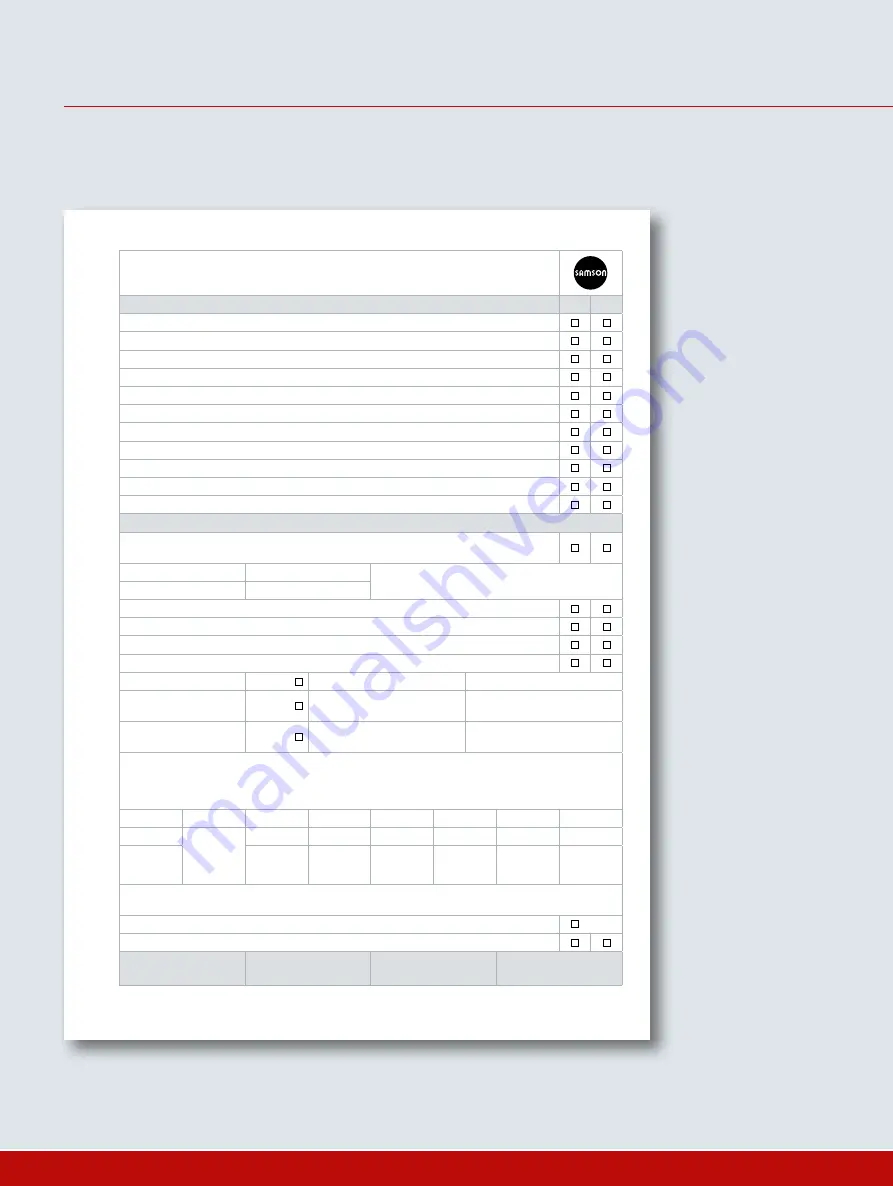
30
Competence in Functional Safety
Functional safety of globe valves, rotary plug valves, ball valves and butterfly valves
9 Appendix 2 − Example of a checklist for a final element
Competence in Functional Safety
Functional safety of globe valves, rotary plug valves, ball valves and butterfly valves
Competence in Functional Safety
Functional safety of globe valves, rotary plug valves, ball valves and butterfly valves
30
31
Checklist for testing safety equipment
Final element test
Yes
No
Is the tag documentation complete and up-to-date?
Are the connecting cables in good order?
Are the screw fittings in good order?
Is the labeling complete and in a readable state? Control room, on site, process control system and safety PLC
Are all connecting housings free of moisture, water, oil and dust? (solenoid valve, feedback etc.)
Are the actuator or solenoid valve free of corrosion? Paint finish in good order?
Visual inspection of the pneumatic system: Are all pneumatic connections in good order and leak-tight?
Are the bridges, yokes, stem connectors, fastening nuts free of corrosion and fastened properly?
Is the valve packing leak-tight? Are there any visible signs of the process medium?
Is the bellows seal/bellows monitoring still in good order?
Check of the exhaust ports of the solenoid valve
Fail-safe position check
Open final element in
process control system
Set to Manual and move
P&ID Fail Close
DCS
* Valve: Remove air hose at the air manifold
while the valve is being moved!
Loop
Valve
Do the valve position and output signal match? Move valve to OPEN and CLOSED positions!
Does the actuator move smoothly to its operating position when the signal pressure is applied?
Is there any leakage at the actuator?
Does the actuator move smoothly to its fail-safe position when moved by the springs?
Valve transit time
N/A
Time to open the valve
sec. Time to close the valve
sec.
Closing time
Fail-close position
N/A
Time allowed for the valve
to move to its fail-safe position
sec.
Valve closing time to fail-safe
position
sec.
Permissible leakage rate
N/A
Leakage rate allowed in
fail-safe position
1/min, m³/min
Leakage rate measured
in fail-safe position
1/min, m³/min
To measure the leakage rate, the valve must be removed from the pipeline and tested in the workshop.
Refer to DIN EN 12266-1 (A.4 Seat tightness) for the test procedures.
The following table contains the permissible leakage rates.
For control valves functioning as safety equipment, leakage can also be measured according to DIN EN 1349.
Test medium
Leakage rate A
Leakage rate B
Leakage rate C
Leakage rate D
Leakage rate E
Leakage rate F
Leakage rate G
Liquid
Liquid
No visible
leaks found
during test
0.01 *DN
0.03 *DN
0.1 *DN
0.3 *DN
1.0 *DN
2.0 *DN
Gas
0.3 *DN
3.0 *DN
30.0 *DN
300 *DN
3000 *DN
6000 *DN
The leakage rates only apply when room temperature prevails at the outlet side. “No visible leaks found during test“ means
no visible moisture or formation of drops or bubbles. This corresponds to a lower leakage rate than leakage rate B.
Attach green label after the test has been completed.
Does repair work need to be performed on the system? If this is the case, write out a separate order.
Tester 1:
Tester 2:
Test date:
Signature:
Checklist for testing safety equipment
Owner
Created/Revised by:
Operation:
Plant:
Subplant:
Tag no.:
Operating state during test:
Prüfung:
Shutdown
PLC/DCS:
Tester:
Test date:
Fail-safe position:
SIL level:
Architecture:
Measuring principle:
Manufacturer:
Manufacturer model:
Body number/serial number/stamp number/ID:
Site of installation:
Barrier medium:
+H551-14E2
Final element exists in the following SIL loops
SIF no.:
Commissioning test:
Proof test:
Revision test:
Final element test
……. years
Lockout test
……. years
- An assessment of the process and safety hazards in the plant and installation is necessary.
- Obtain a permit to work!
- Wear suitable protection for the work! Observe explosion protection regulations!
- The person performing the work is responsible for using the appropriate maintenance methods according to the recognized codes
of practice as well as for using suitable and tested tools!
- The person performing the work bears the compulsory insurance during the work!
This includes, for example, the safeguarding of the workplace against unauthorized access or against accidental contact with
unprotected electrical installations while temporarily leaving the workplace.
- Take precautionary measures to protect the plant against external influences, such as weather or other damaging environmental
influences.
Measuring equipment list:
Type/Manufacturer/model:
Serial number:
Type/Manufacturer/model:
Serial number:
Type/Manufacturer/model:
Serial number:
Type/Manufacturer/model:
Serial number:
Type/Manufacturer/model:
Serial number:
Type/Manufacturer/model:
Serial number:
Tester 1:
Tester 2:
Test date:
Signature:
9
Appendix 2 − Example of a checklist for a final element