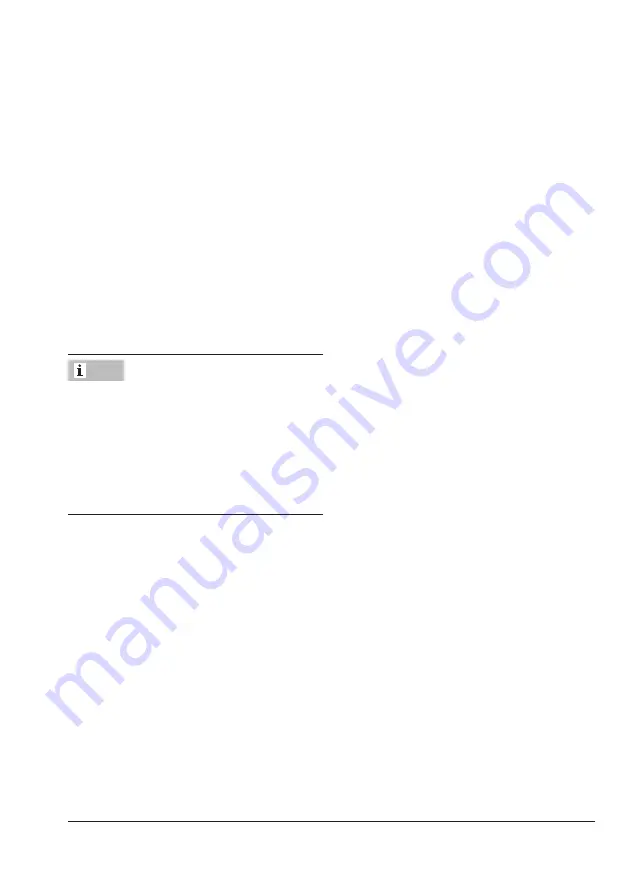
EB 3135-1 EN
41
Servicing
Removing the restriction
The procedure described below refers to
electric actuators without fail-safe action.
1. Put the regulator out of operation (see
section 9.1).
2.
DN 15 to 25:
undo the side adjustment
screw (8.3) and unscrew the connecting
piece (8) belonging to the restriction us-
ing a socket wrench.
DN 32 to 50:
unscrew the connecting
piece (8) belonging to the restriction.
3. Remove the seal (8.7).
The actuator stem of electric actuators with
fail-safe action must be retracted before
mounting or removing the electric actuator.
Refer to the mounting and operating instruc-
tions of the electric actuator with fail-safe ac-
tion for more details. See information under
‘Referenced documentation’ on page 7.
Note
Mounting the restriction
The procedure described below refers to
electric actuators without fail-safe action.
1. Insert the seal (8.7).
2.
DN 15 to 25:
screw the connecting piece
(8) belonging to the restriction using a
socket wrench. Screw in the side adjust-
ment screw (8.3). Observe the tightening
torques specified in section 7.5.
DN 32 to 50:
screw the connecting piece
(8) belonging to the restriction. Observe
the tightening torques specified in sec
-
3. Install the regulator into the pipeline.
4. Fasten the electric actuator (10) using the
coupling nut (10.2) to the connecting
piece (8) of the valve. Observe the tight-
ening torques specified in section 7.5.
5. Connect the supply voltage to the electric
actuator (see section 6.1.1).
6. Put the regulator into operation (see sec-