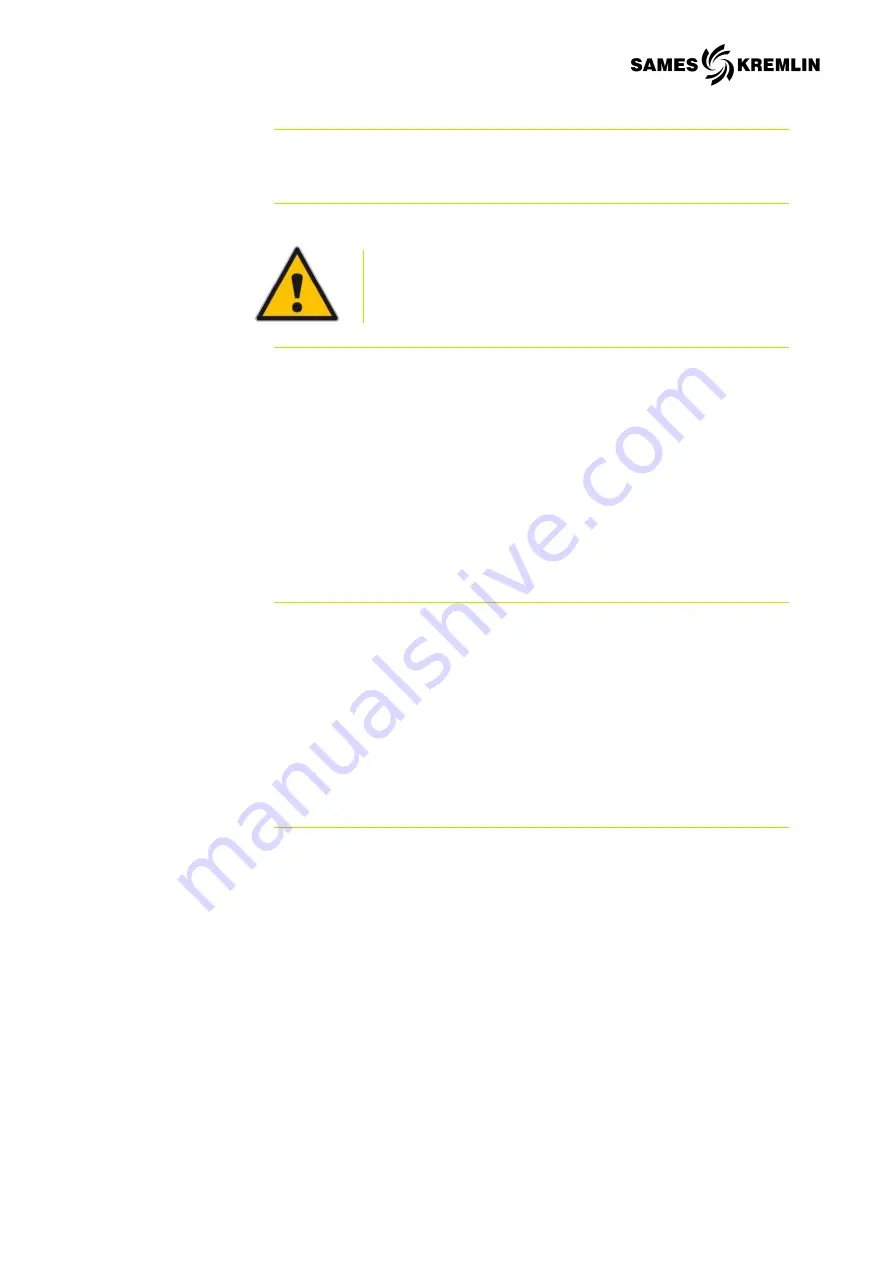
Commissioning
30
8
Commissioning
The fluid sections are integrated in a system, if necessary
refer to any additional instructions for further information
on commissioning.
Pump
The Pumps are tested for operation at the factory using a light weight
oil lubricant.
Before commissioning, this lubricant must be removed by flushing with
a suitable solvent.
At the end of the day, flush with a suitable solvent.
It is advisable to stop the fluid section in the "low" position in order to
prevent the product from taking hold of the piston rod.
Motor
The Air motors are tested before their shipment. Nevertheless:
Before coupling the Air motor to a fluid section pump, it is
recommended to run the air motor at a low air pressure (1
bar / 14.5 psi max) for a few minutes.
Couple the motor with the recommended pump fluid
section.