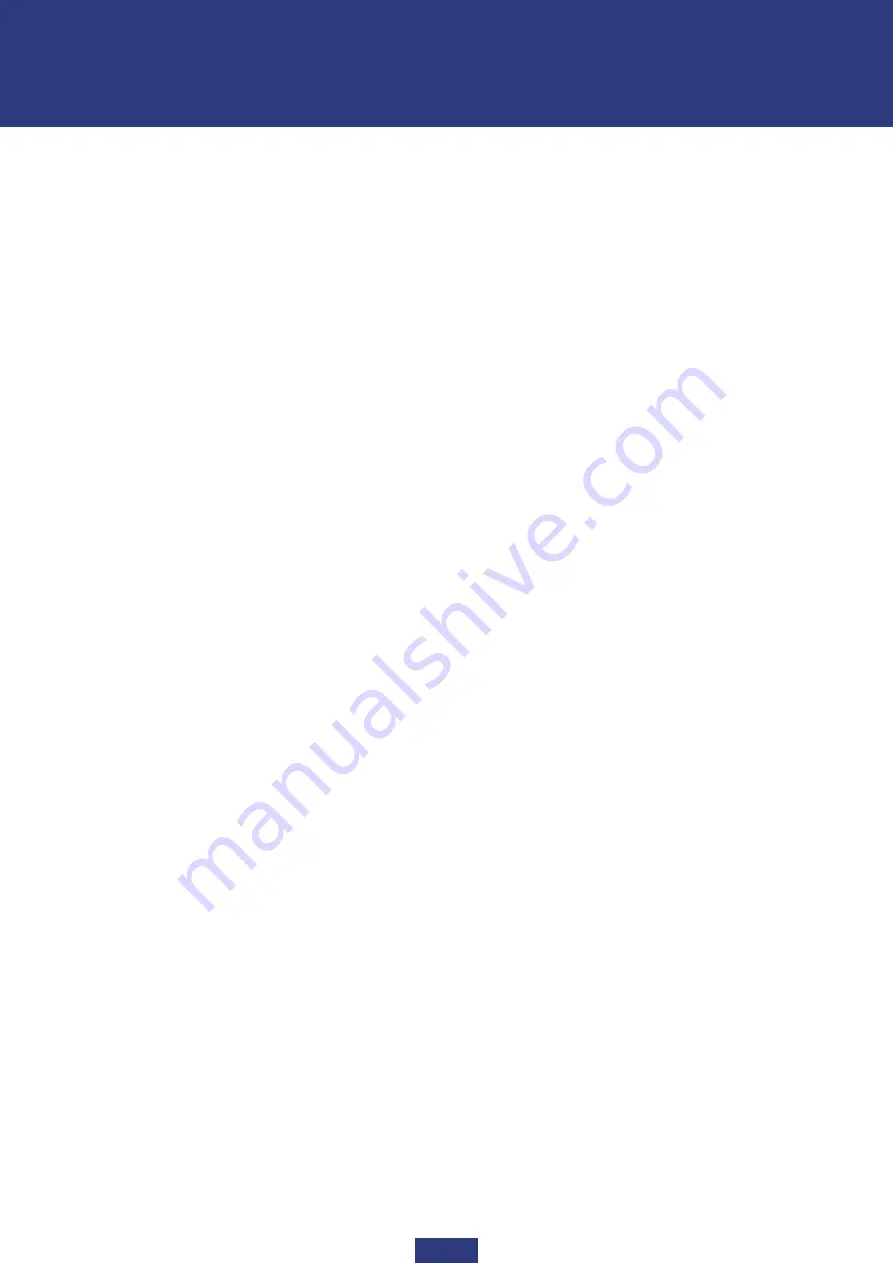
Installation | Receiving Pump | Storage | Location
Setting Baseplate/Pedestal | Alignment Procedure
INSTALLATION
RECEIVING PUMP
Check pump for shortages and damage immedi-
ately upon arrival. (An absolute must!) Prompt
reporting to the carrier's agent, with notations
made on the freight bill, will expedite satisfactory
adjustment by the carrier.
Pumps and drivers are normally shipped from the
factory, mounted on a baseplate. Couplings may
either be completely assembled or have the
coupling hubs mounted on the shafts and the
connecting members removed. When the connect-
ing members are not assembled, they will be
packaged in a separate container and shipped with
the pump or attached to the baseplate.
Shafts are in alignment when the unit is shipped;
however, due to shipping, the pumps may arrive
misaligned and, therefore, alignment must be
established during installation. SAM Engineering
has determined that proper and correct alignment
can only be made by accepted assembly practices.
Refer to the following paragraphs on "Foundation",
"Setting Baseplate", "Grouting Procedure",
"Alignment Procedure", and "Doweling".
STORAGE
Short term: (Less than 6 months) SAM Engineering
normal packing procedure is designed to protect
the pump during shipping. Upon receipt, store in
a covered and dry location.
Long term: (More than 6 months) Preservative
treatment of bearings and machined surfaces will
be required. Rotate shaft several times every 3
months. Refer to driver, coupling and seal
manufacturers for their long-term storage
procedures. Store in a covered, dry location.
LOCATION
The pump should be installed as near the suction
supply as possible, with the shortest and most
direct suction pipe practical. The total dynamic
suction lift (static lift plus friction losses in suction
line) should not exceed the limits for which the
pump was sold.
The pump must be primed before starting.
Whenever possible, the pump should be located
below the fluid level to facilitate priming and
assure a steady flow of liquid. This condition
provides a positive suction head on the pump. It is
also possible to prime the pump by pressurising
the suction vessel.
When installing the pump, consider its location in
relation to the system to assure that sufficient Net
Positive Suction Head (NPSH) at pump suction is
provided. Available NPSH must always equal or
exceed the required NPSH of the pump.
The pump should be installed with sufficient acces-
sibility for inspection and maintenance. A clear
space with ample headroom should be allowed for
the use of an overhead crane or hoist sufficiently
strong to lift the unit.
NOTE: Allow sufficient space to be able to disman-
tle pump without disturbing the pump inlet and
discharge piping.
Select a dry place above the floor level wherever
possible.
Make sure there is a suitable power source avail-
able for the pump driver. If motor driven, electri-
cal characteristics should be identical to those
shown on motor data plate.
SETTING BASEPLATE/PEDESTAL
The foundation surface will support the pump and
driver with shims and plates under the baseplate
at the foundation bolts. The foundation should be
smooth and level at these points to distribute the
load evenly on the shims. A thin metal plate
levelled in a puddle of mortar or grout is often the
easiest way to achieve this level and smooth
surface. Use thick shims wherever possible to
reduce the number of shims used.
ALIGNMENT PROCEDURE
The pump and driver have been checked at the
factory to determine that field alignment dimen-
sionally can be made. Shims and dowels are
packaged separately and shipped with the pump.
It is mandatory that the unit be field aligned since
any baseplate, regardless of size or style, can be
warped in shipment or when installed on a founda-
tion. Generally, any type of coupling can be used
if aligned properly.
SUCTION AND DISCHARGE PIPING
When installing the pump piping, be sure to
observe the following precautions:
a) Both the suction and discharge piping should
be independently supported near the pump
and properly aligned so that no strain is
transmitted to the pump when the flange bolts
are tightened. Use pipe hangers or other
supports at necessary intervals to provide
supports.
4
Summary of Contents for CSR
Page 1: ......