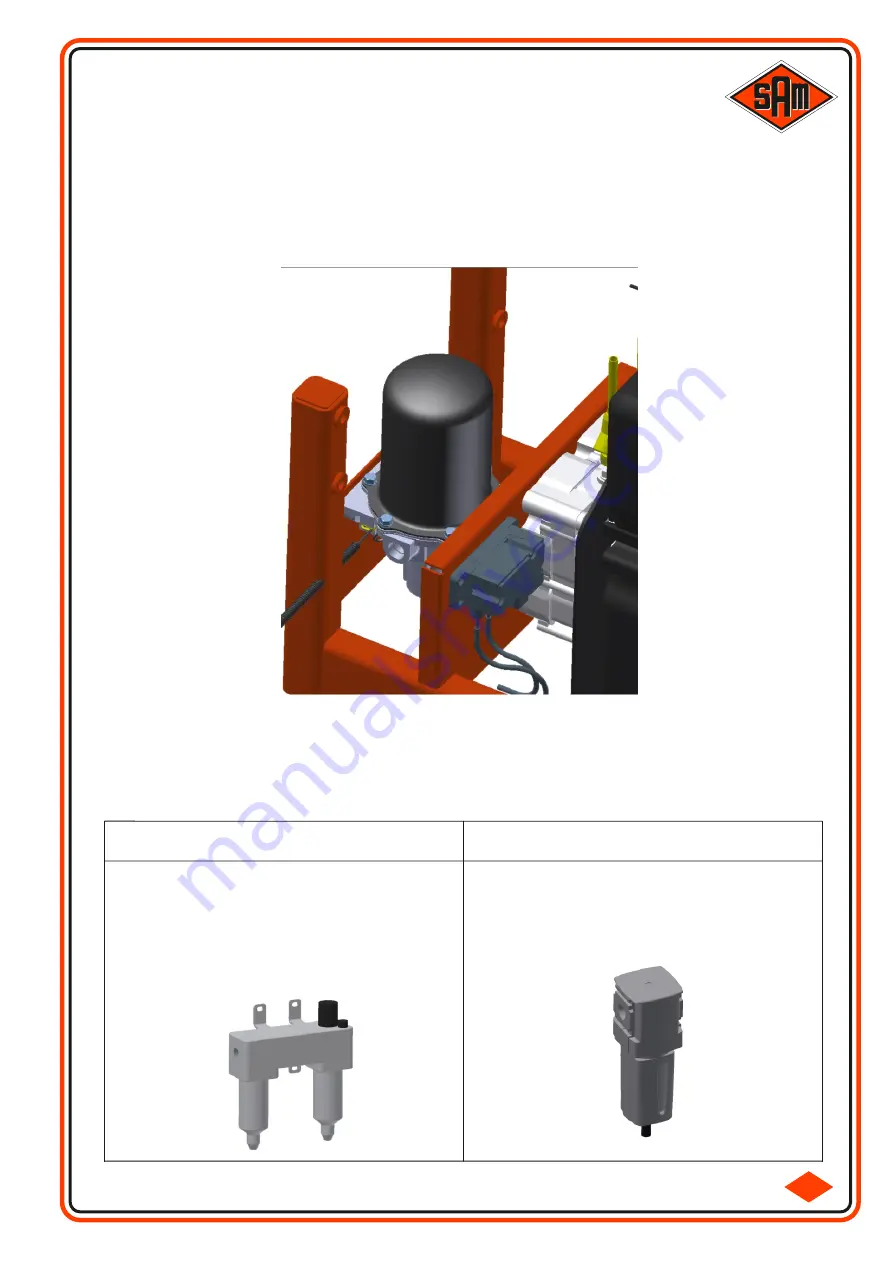
43
An air compressor mounted directly on the engine provides the air supply for the machine.
An Air Dryer with integral unloader valve is mounted on the Right hand side of the machine, behind the AdBlue
Reservoir. This is preset to maintain the air pressure at approximately 8 bar (116 psi). A filter is incorporated
within the unit and should be replaced following the maintenance schedule.
The Air reservoir, mounted below the engine, (incorporated within the chassis) should be drained daily.
COMPRESSED AIR SYSTEM
3-12
Air is fed throughout the machine via a filter/lubricator assembly located at the right hand end of the cat walk.
THE AIR RESERVOIR MUST BE CHECKED ANNUALLY BY A RECOGNISED INSPECTOR.
With lubricator
Without lubricator
SAM Ltd recommends the use of 'Tellus 37' lubricant in the
lubricator bowl.
It is impossible for SAM Ltd to satisfactorily adjust the
lubrication rate. The operator must regulate this himself
over several weeks.
Oil usage should be in the region of one bowl every 500 to
600 hours.
Due to a recent product development, the system now
does not require a lubricator as pneumatic components
are now self lubricating.
In this case, the operator will find only a filter and water
trap.
Summary of Contents for Horizon
Page 5: ...4 SECTION 1 SAFETY ...
Page 14: ...13 ...
Page 15: ...14 SECTION 2 MACHINE CONTROLS 2 1 4000 4000E 5500 6000 MACHINES 2 2 3000 3000E 3500 MACHINE ...
Page 32: ...31 SECTION 3 MECHANICAL COMPONENTS ...
Page 40: ...39 3 8 TYRES LOAD INDEX TABLE ...
Page 45: ...44 ...
Page 46: ...45 SECTION 4 SPRAYING COMPONENTS ...
Page 53: ...52 SECTION 5 SPRAYING ...
Page 58: ...57 ...
Page 59: ...58 SECTION 6 6 1 MAINTENANCE 6 2 Fuses for 3000 3000E 3500 Machine ...