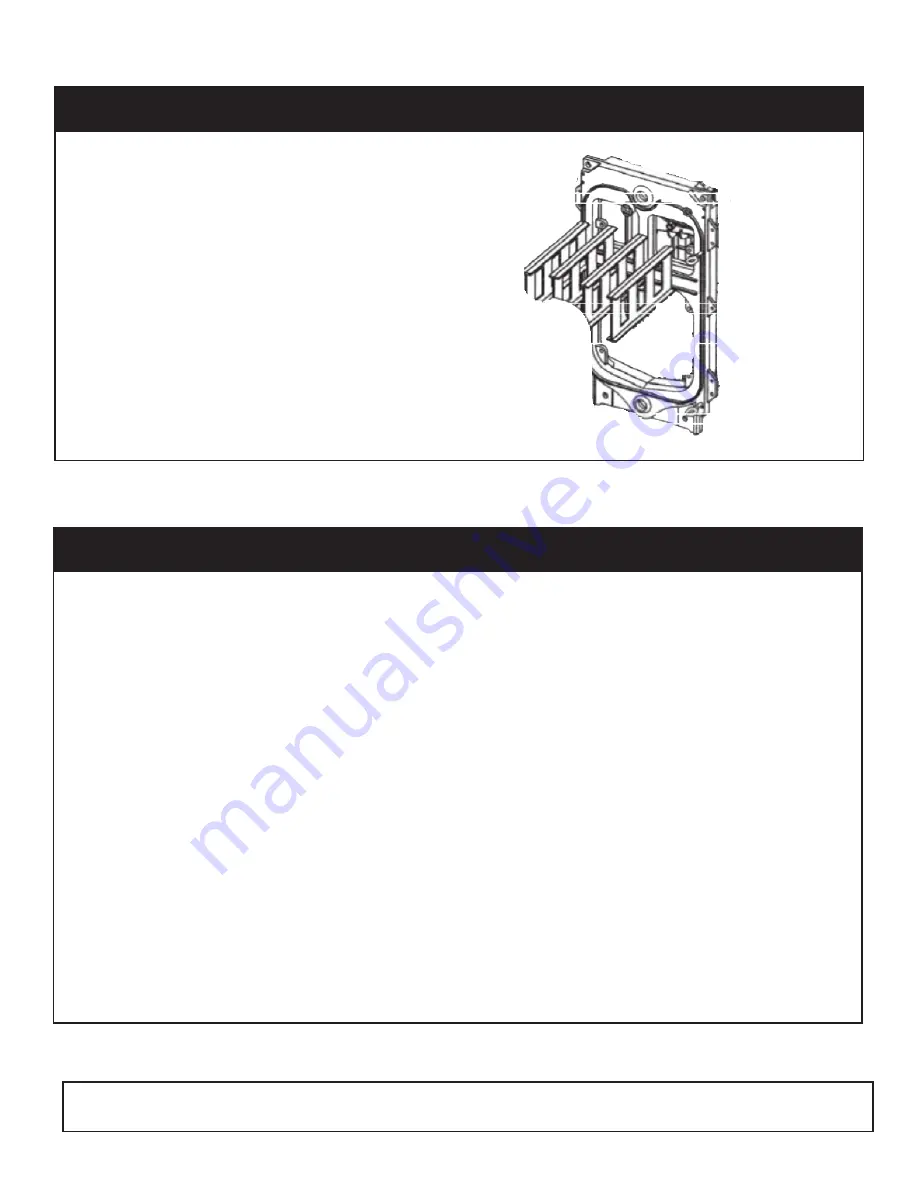
22
To achieve maximum efficiency, baffles
have been installed in the second pass
of the boiler. One baffle is installed into
each of the 2nd passes as shown in Fig. 10.1.
For the baffle to fit correctly, the shortest
leg of the baffle must be facing down. If
the steady state flue temperature is too
low, less than 325º F, the baffles may be
removed to increase the temperature.
11. Baffle Installation
Fig 10.1
The electricity to the boiler shall come from a dedicated breaker in the electric
service box. A service switch should be mounted on the side of the boiler so the
burner technician can service the burner and controls. The electrical wiring should be
routed so as not to interfere with normal servicing of the boiler. Wiring done in the field
between devices not attached to boiler shall conform with the temperature limitations
for type T wire (63F/35C) or other specified wire as applicable when installed in
accordance to manufacturer's instructions and wiring diagrams.
If an external electrical source is utilized, the boiler, when installed, must be
electrically bonded to ground in accordance with the requirements of the authority
having jurisdiction or, in the absence of such requirements, with the National Electrical
Code, ANSI/NFPA 70 and/or the Canadian Electrical Code Part 1, CSA C22.1, Electrical
Code.
Since the boiler is equipped with a swinging burner door, the supplied 48” long
burner wiring harness with 4-prong quick disconnect plug needs to be used. The short
end of the wiring harness needs to be wired to the burner following the respective
burner wiring diagram in the subsequent pages of this manual. The long end of the
wiring harness needs to be wired into the burner operating control located at the
installers discretion.
NOTE: You must connect a pump to C terminals on hydrostat when using DHW. Pump
needs to turn on to push heat for DHW through boiler.
12. Wiring
Refer to pages 25 for oil wiring diagrams and page 26 for gas wiring diagrams. Priority
wiring for Hydrolevel controls is on pages 24.