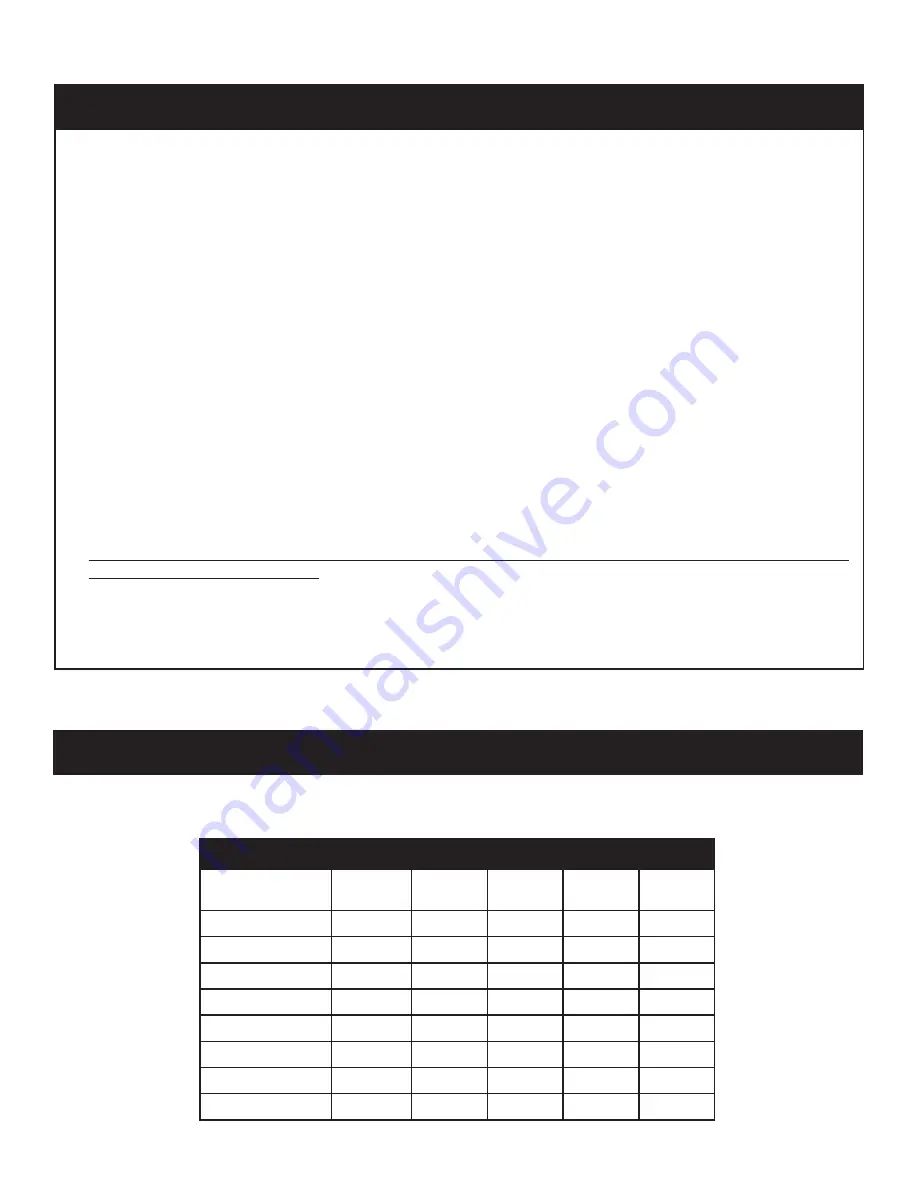
16
8. Burner Setup
Good, reliable operation with a minimum of service, starts with attention to the small
details:
Please review burner manufacturer manuals for proper install guidelines!
Oil:
1. Setting the nozzle position and electrodes to the manufactures specs using the
manufacturer's gauges.
2. Installing a quality micron filter at the burner.(replace old oil lines and clear sludge)
3. Making careful/tight flare connections, without couplings, on oil suction line.
4. Checking fuel pump pressure is set to specs on following page.
5. Checking draft at the breeching to insure it is adequate to overcome flue gas
resistance. (-.02 to –.04 in. w.c.)
6. Setting the air band properly with well maintained instruments. A good target is 12%
to 12.5% of (CO2).
7. To achieve the rated efficiency level the CO2 should be set to 12.5% CO2.
To ensure proper burner setup, gauges should be used to check things such as the
pump pressure, CO2 levels, CO levels, etc…
Gas:
1. Checking the electrode, orifice size, and flame rod settings against manufacturer’s
specs to insure proper operation.
2. Installing properly sized gas piping according to BTU input required and length of gas
line run.
3. Making sure there is proper manifold pressure before and after the gas valve using
a calibrated manometer.
4. Checking draft at the breeching to insure it is adequate to overcome flue gas
resistance. (-.02 to –.04 in. w.c.)
5. Setting the air band properly with well maintained instruments. A good target is 9.5%
to 10.0% of (CO2) for natural gas, or 11.0% to 11.5% of (CO2) for LP gas.
8.1 Oil Burner Setup
BURNER MANUFACTURER: RIELLO
Boiler Model:
OPTI GLP
6
OPTI GLP
8
OPTI GLP
10
OPTI GLP
12
OPTI GLP
14
Burner Model:
40 F10
40 F20
40 F20
40 F20
40 F20
Firing Rate (GPH):
2.23
3.13
4.00
4.90
5.54
Insertion Depth:
3.5”
5”
5”
5”
5”
Nozzle:
1.75X60
2.50X60
3.00X60
3.50X60
4.00X60
Spray Pattern:
B
B
B
W
W
Pump Pressure:
190 psi
175 psi
190 psi
205 psi
205 psi
Turbulator:
4
0
1
3
5
Air Gate:
4.00
2.75
3.50
4.50
5.25
This page is only for boilers using an oil burner. If a gas burner is being used,
please refer to page 17 for the proper setup of the burner and gas lines.
NOTE:
Elevated CO during combustion analysis for the first few hours of operation from
off gassing due to insulation in the combustion chamber.