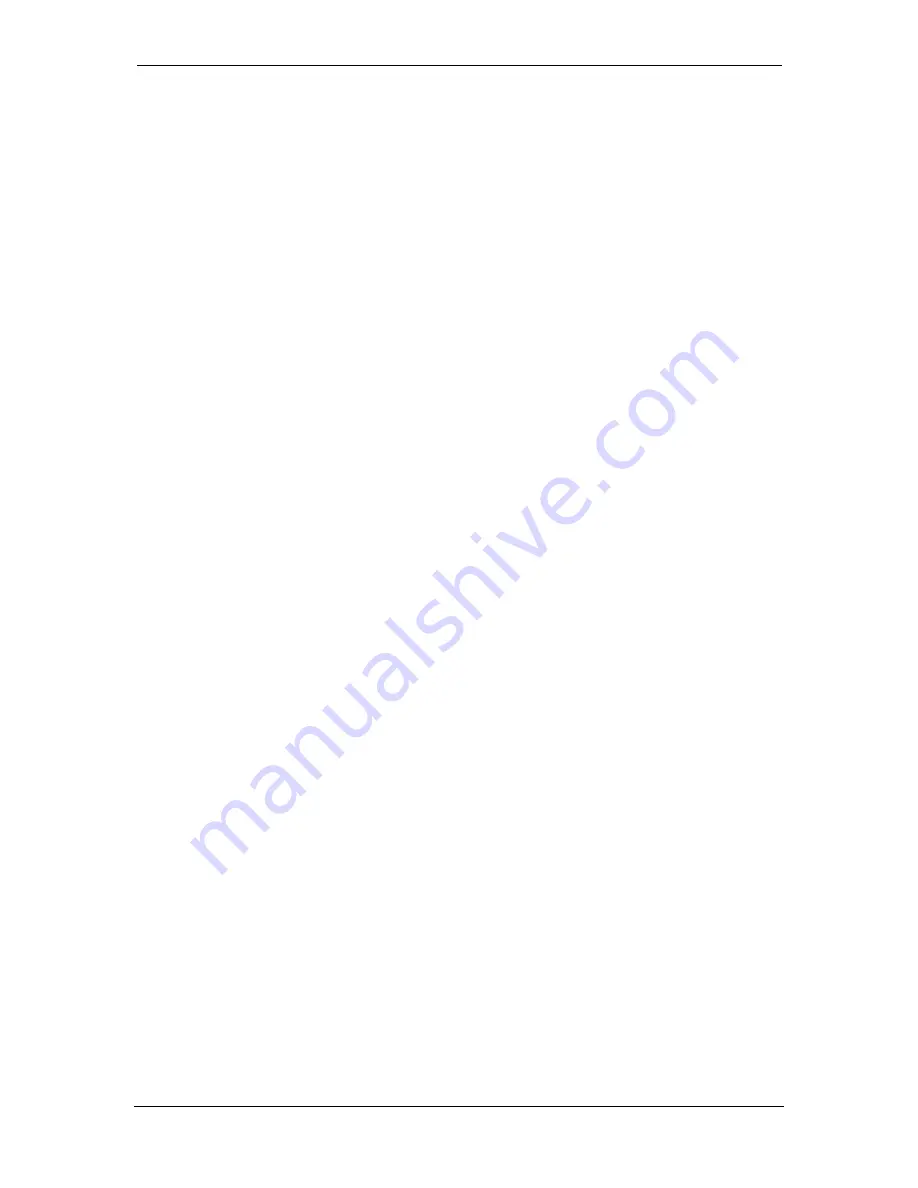
PFD2/PFS2 – OPERATING INSTRUCTIONS
INDEX
DATE
N°
03
26/06/01
DC02020US
5/11
IV.4 – Applications
The PFD/PFS pump is a volumetric pump. The stroke volume is dependent on the flow rate and
discharge pressure.
In order to know the precise flow rate of the pump, a paddle wheel flow transmitter can be fitted on
outlet. For PFD2/PFS2 the part number of the flow transmitter is DP11619.
•
Part number marked
K
(PFD2 316K or PFS2 316K) indicates that the pump will be supplied with
KALREZ
®
manifold (P/N 2464K) and body (P/N 2738K) O.rings.
•
Part number marked
W
(PFD2 316W or PFS2 316W) indicates that the pump will be supplied
with PFA manifold seals (P/N 2587), PTFE body rings (P/N 2588), and special manifolds
(P/N 2586M and 2585M).
•
Part number marked
G
(PFD2 316G or PFS2 316G) indicates that the pump will be supplied with
manifolds with no seals (P/N 2749G and 2750G) and PTFE body seals (P/N 2588).
PFS2 pumps are equipped with valve seats without lip (P/N 2759A) and rounded spires bellows
(P/N 2760S) in order to pump abrasive products (Slurry).
Common applications are:
•
Semiconductor Industry:
Transfer of ultrapure and corrosive chemicals.
Pump filter recirculation systems.
•
Pharmaceuticals and Chemicals: Chemical injection and sampling.
IV.5 – Limitations of use
The standard pumping speed of the PFD2/PFS2 is about 120 strokes/min.
The following should NOT be part of the system:
•
Do not connect the pump inlet or outlet with air, nitrogen or liquid under pressure,
•
Lubricated and/or wet air/nitrogen,
•
Air supply tubing greater than 5/32" ID (4 mm),
•
Air line length between the pump and control valve less than 10 feet (3 m) and more than
20 feet (6 m),
•
Air pressure less than 29 PSI (2 bar) or greater than 72.5 PSI (5 bar),
•
Inlet connection less than 5/8" ID (15 mm),
•
Restricted suction side (valves, filters...)
•
Exceed the recommended liquid temperatures,
•
Pumping too viscous or abrasive liquids.
Any of the above may be detrimental to the normal operation and life expectancy of the pump, and
may invalidate the warranty.
If the pump is being used with very corrosive chemicals, or if it is left for extended periods not in use,
we recommend the system is emptied and flushed.
V – Maintenance
V.1 – Trouble Shooting
If the pump stops for any reason check:
•
The air/nitrogen supply,
•
That all valves in the chemical lines are open.
Before dismantling the pump, ensure the shuttle valve is in the correct position. Depress the manual
override on the shuttle valve (P/N 2701) to re-position the shuttle.