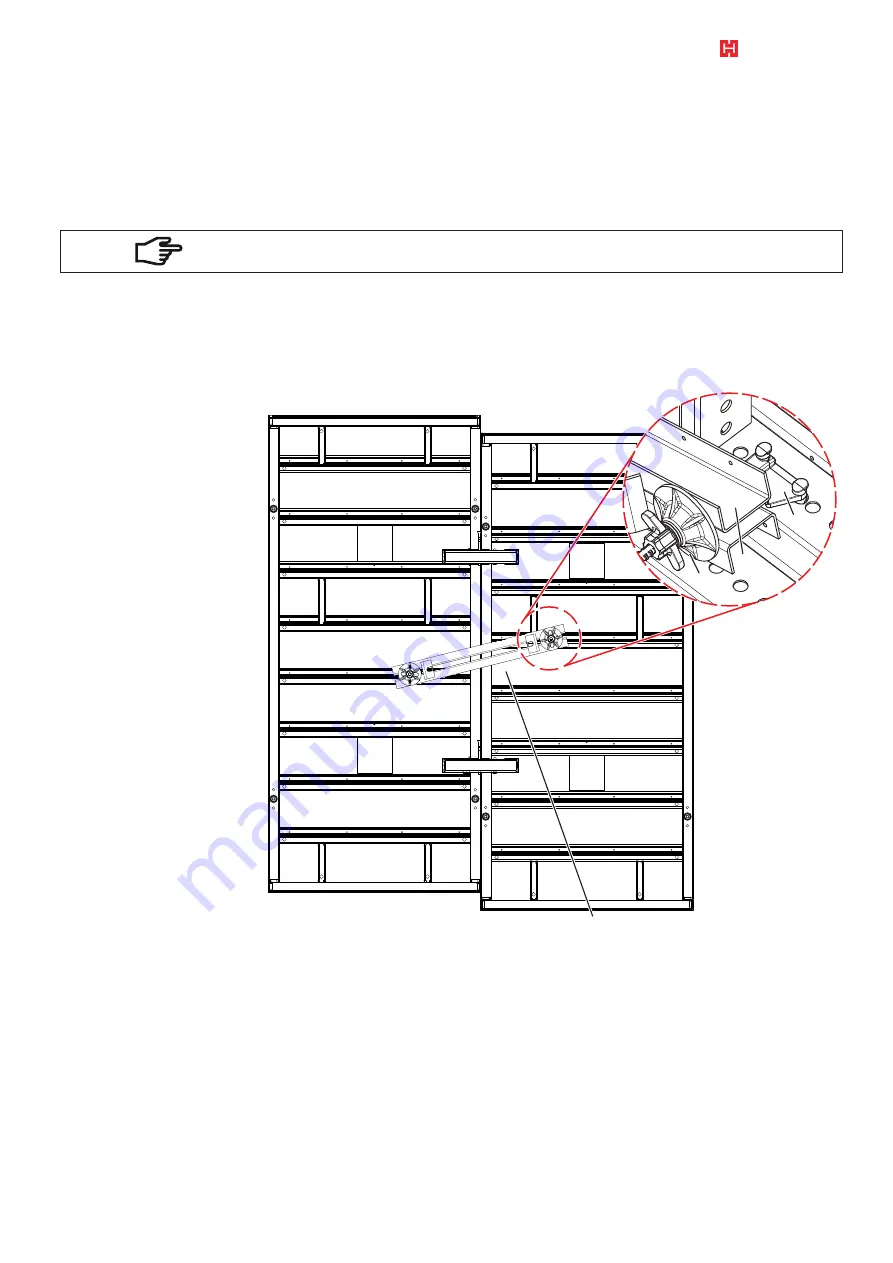
63
Unless stated otherwise, all dimensions are given in mm.
MANTO®
5 Connecting panels horizontally
MANTO panels are normally connected to one another using the MANTO Aligning
Panel Clamp or the PM Aligning Wedge Clamp. The Adjustable Aligning Clamp or the
Multipurpose Waler 100 has to be used for infills at the vertical joint.
Check that all connectors are tight and, if necessary, retighten before every use and
every time they are moved.
5.1
Height offset
MANTO panels can be connected with a height offset of 20 mm using the MANTO con-
nectors. For greater offsets and when the connectors cannot grasp over the H-ribs, the
vertical joints have to be braced with MANTO walers as well.
Multipurpose Waler 100 (
A
, code:450764)
PLATINUM 100 Multi Bolt (
B
, code:605810)
MANTO Tie Nut (
C
, code:464600)
A
C
B
Summary of Contents for Huennebeck MANTO G3
Page 1: ...MANTO Large frame panel formwork User guide...
Page 9: ...9 Unless stated otherwise all dimensions are given in mm MANTO...
Page 61: ...61 Unless stated otherwise all dimensions are given in mm MANTO MANTO G3 M MANTO G3 M...
Page 219: ...219 Unless stated otherwise all dimensions are given in mm MANTO...