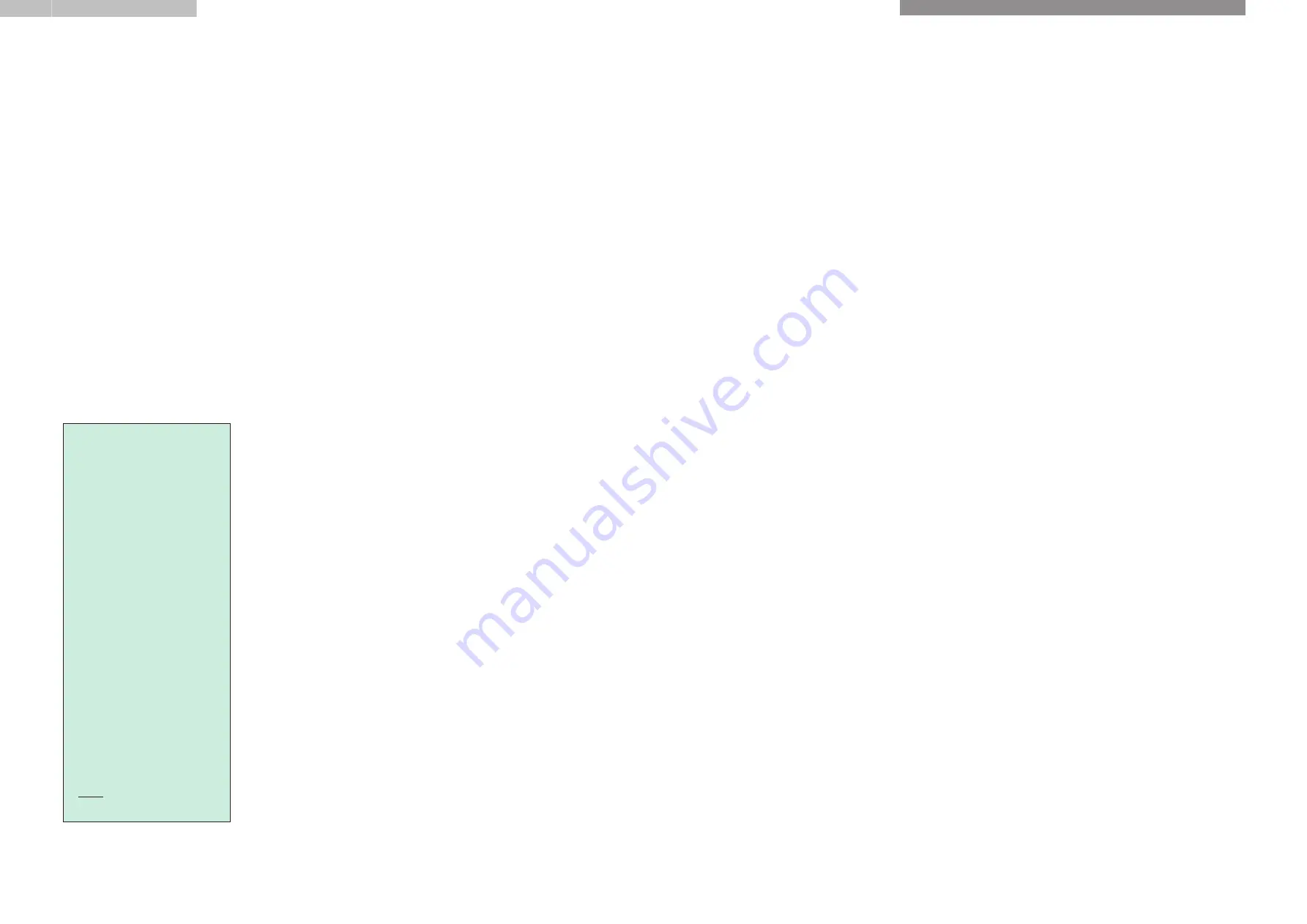
27
11.
Maintenance of block batteries
in service
In a correctly designed standby
application, the block battery requires
the minimum of attention. However, it
is good practice with any system to
carry out an inspection of the system
at least once per year, or at the
recommended topping-up interval
period to ensure that the charger, the
battery and the ancillary electronics
are all functioning correctly.
When this inspection is carried out, it
is recommended that certain
procedures should be carried out to
ensure that the battery is maintained
in a good state.
11.1
Cleanliness/mechanical
Cells must be kept clean and dry at
all times, as dust and damp cause
current leakage. Terminals and
connectors should be kept clean, and
any spillage during maintenance
should be wiped off with a clean
cloth. The battery can be cleaned,
using water. Do not use a wire brush
or a solvent of any kind. Vent caps
can be rinsed in clean water, if
necessary.
Check that the flame arresting vents
are tightly fitted and that there are no
deposits on the vent cap.
Terminals should be checked for
tightness, and the terminals and
connectors should be corrosion
protected by coating with a thin layer
of neutral grease or anti-corrosion oil.
11.2
Topping-up
Check the electrolyte level. Never let
the level fall below the lower MIN
mark. Use only approved distilled or
deionised water to top-up. Do not
overfill the cells.
Excessive consumption of water
indicates operation at too high a
voltage or too high a temperature.
Negligible consumption of water, with
batteries on continuous low current or
float charge, could indicate under-
charging. A reasonable consumption
of water is the best indication that a
battery is being operated under the
correct conditions. Any marked
change in the rate of water
consumption should be investigated
immediately.
The topping-up interval can be
calculated as described in section
6.9. However, it is recommended
that, initially, electrolyte levels should
be monitored monthly to determine
the frequency of topping-up required
for a particular installation.
Saft has a full range of topping-up
equipment available to aid this
operation.
Therefore, the volume of hydrogen
evolved from a battery per hour
= number of cells x charge current
x 0.45 liters
or = number of cells x charge current
x 0.00045 m
3
The volume of hydrogen found by this
calculation can be expressed as a
percentage of the total volume of the
battery room, and from this, the
number of air changes required to
keep the concentration of hydrogen
below a certain level can be
calculated.
Thus, to maintain a maximum
concentration of 2 % (for example),
the air in the room will need
changing 3/2 = 1.5 times per hour.
In practice, a typical figure for natural
room ventilation is about 2.5 air
changes per hour, and so, in this
case, it would not be necessary to
introduce any forced ventilation.
In a floating situation, the current
flowing is very much lower than when
the cell is being charged, and the gas
evolution is minimal; it may be
calculated in the same way using
typical floating currents.
10.5
Preparation for service
Filled cells
Check that cells are externally clean
with adequate protective finish on
posts and connectors.
Carefully remove the plastic transport
seal, and visually check that the
electrolyte levels in the opened cells
are at the MAX level.
If necessary, adjust by careful addition
of approved distilled or demineralised
water.
Wipe away any small spillage on cells
using a clean cloth and close the flip-
top vents to complete preparation for
service.
The cells can now be commissioned
as described in section 8.6.
Discharged and empty cells
Check that cells are externally clean
with adequate protective finish on
posts and connectors.
Identify and calculate the electrolyte
type and quantity required to fill the
cells*. Do not remove the plastic
transport seals at this stage.
Prepare new electrolyte to requirement
from solid electrolyte or liquid
electrolyte, as supplied. When filling
the cells, refer to the ìElectrolyte
Instructionsî data sheet supplied with
the electrolyte. Ensure that only
demineralised or pure distilled water
is used.
Carefully remove the plastic transport
seal and leave the flip-top vents
open.
Carefully fill the cells using a plastic
jug and funnel to a level 5-10 mm
below the MAX level. Allow the cells
to stand for 24 hours. For large
installations, a pump system is
recommended.
Add cell oil as described in the
electrolyte leaflet.
After 24 hours stand, carefully
complete filling the cell to the
maximum level.
Wipe away any small spillage on cells
using a clean cloth and close the flip-
top vents to complete preparation for
service.
The cells can now be commissioned
as described in section 8.6.
*Please refer to the installation and
operation instruction sheet.
26
Example:
A battery of 98 cells, type SBH 77
on a two step, two tier stand, is
placed in a room of dimensions
2 m x 2 m x 3 m.
The charging system is capable of
charging at 0.1C
5
and so the
charging current is 7.7 amperes.
The volume of hydrogen evolved
per hour in this, the worst, case is:
= 98 x 7.7 x 0.00045 m
3
= 0.34m
3
The total volume of the room is
2 x 2 x 3 = 12 m
3
Approximate volume of battery and
stand does not exceed 1 m
3
, and
so, the volume of free air in the
room is 11 m
3
.
Therefore, the concentration of
hydrogen gas after charging for 1
hour at full gassing potential at
0.1C
5
will be:
= 0.34 = 3%
11
Contents
Home
Back
Contents