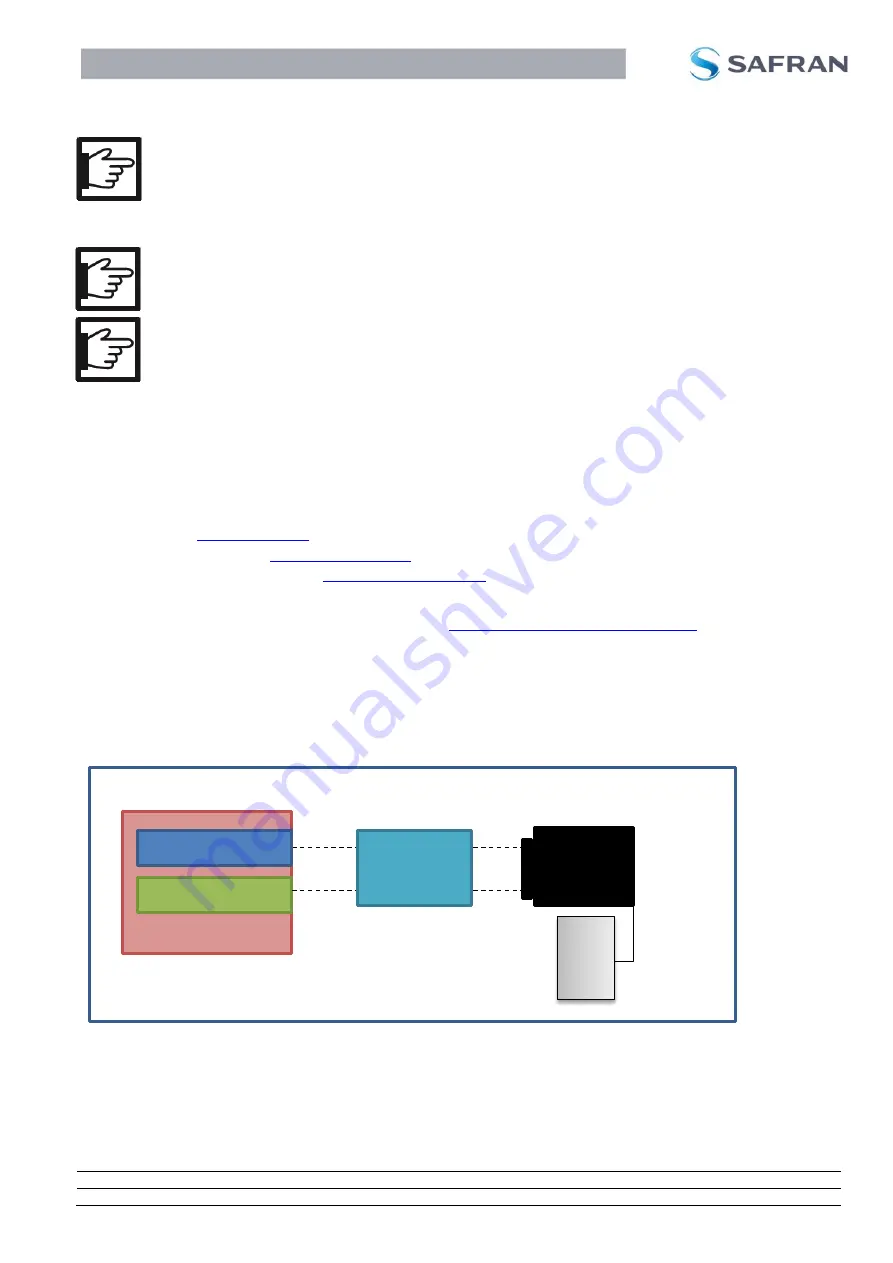
LRF 3013 Integrator Manual
Document number: TML 913655 ver A
Public: 13.03.2017
Confidential & Proprietary
Safran Vectronix AG
– All rights reserved
page: 18/36
Mechanical stress due to tolerance and thermal expansion coefficient mismatches between the
module’s and application‘s mechanical interface should be avoided as much as possible. An
undefined stress could result in a misalignment of the module’s transmitter and receiver
channel and reduces the range performance.
Assembly personnel must be experienced in handling precision, sensitive electronic,
mechanical and optical assemblies.
Vibration and shocks outside the specified values can destroy or shift parts inside the LRF in a
way that proper use is no longer possible.
4.2.3
Boresighting
The module receiver and transmitter are boresighted in the factory. For this reason, the module and can
be mounted and replaced easily. For a professional boresighting of the LRF module with the main optical
axis of the host system, we recommend the use of a collimato
r and a camera that can see the 1’550 nm
wavelength of the laser module. Vendors of 1’550 nm cameras (SWIR cameras):
XenICs (
) (e.g. XEVA-1.7-320)
Sensors Unlimited (
) (e.g. 640HS-1.7RT)
Allied Vision Technologies (
) (e.g. Goldeye P-008 SWIR)
Collimators can be sourced from Möller Wedel Opical (
http://www.moeller-wedel-optical.com
Note: The LRF module provides a low power continuous lasing mode to make its line of sight visible to
SWIR cameras. Please see chapter 6.2.5 for details.
Figure 8 below illustrates the alignment set-up with a collimator and 1550 nm camera.
Figure 8: Alignment Set-up with collimator and 1550 nm camera
1550 nm
Camera
S
c
ree
n
Host System
LRF module
Main optical axis
Collimator
Summary of Contents for LRF 3013
Page 36: ......