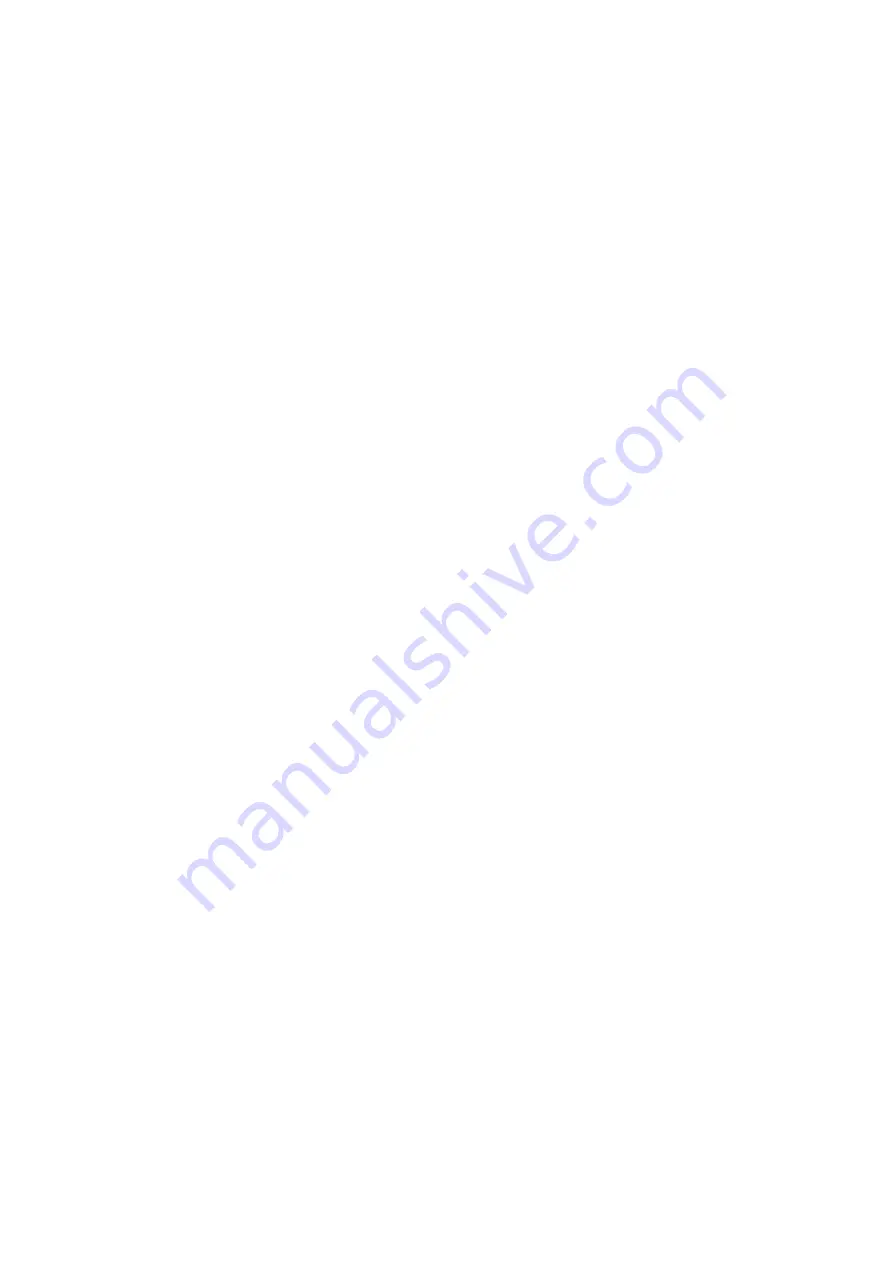
17
Spare parts & Exploded view of ST.33
Drawing
Article nr.
Description
Drawing
Article nr.
Description
1
360.1001
Screw
34
360.1034
Pressing strip
2
360.1002
Motorhousing left side
35
360.1035
Wiring cover
3
360.1003
Label (Left side)
36
360.1036
Frame
4
360.1004
Motorhousing right side
37
360.1037
Clampsystem
5
360.1005
Label (Right side)
38
360.1038
Setting Screw
6
360.1006
Sensor Holder
39
360.1039
Setting Nut
7
360.1007
Bolt M5x60
40
360.1040
Motorcable cover
8
360.1008
Motor Assembly
41
360.1041
Wire #1
9
360.1009
Pin 6x60
42
360.1042
Wire #2
10
360.1010
Lower Inner Gear Plate
43
360.1043
Wire #3
11
360.1011
Gasket
44
360.1044
Wire #4
12
360.1012
Bearing 608
45
360.1045
Connector
13
360.1013
1st Gear
46
360.1046
Coupling nut
14
360.1014
Spindle Gear
47
360.1047
Capstan hub
15
360.1015
Bearing 626ZZ
48
360.1048
Arm
16
360.1016
Adaptor ring
49
360.0001
Battery Pack
17
360.1017
Bearing 6003DDU
50
360.1050
Bolt
18
360.1018
Gear Casing
51
360.1051
Screw
19
360.1019
Spindle Drive Shaft
52
360.1052
Battery Contact board
20
360.1020
Bolt M5x10
53
360.1053
Connector
21
360.1021
Tank holder
54
360.1054
Connector
22
360.1022
Slide
55
360.1055
Battery slide base
23
360.1023
Washer 6
56
360.1056
On Switch
24
360.1024
Bolt M6x20
57
360.1057
Off Switch
25
360.1025
Bolt M6x14
58
360.1058
Main power Switch
26
360.1026
Steady
59
360.1059
connector
27
360.1027
Spindle
60
360.1060
connector
28
360.1028
Rack
61
360.1061
Front Panel Plate
29
360.1029
Screw
62
360.1062
Crimp nut
30
360.1030
Washer
63
360.1063
Screw
31
360.1031
Brass rail (Left side)
64
360.1064
Control Unit
32
360.1032
Brass rail (Right side)
65
360.1065
Rear Panel Plate
33
360.1033
Motor cable protection screw