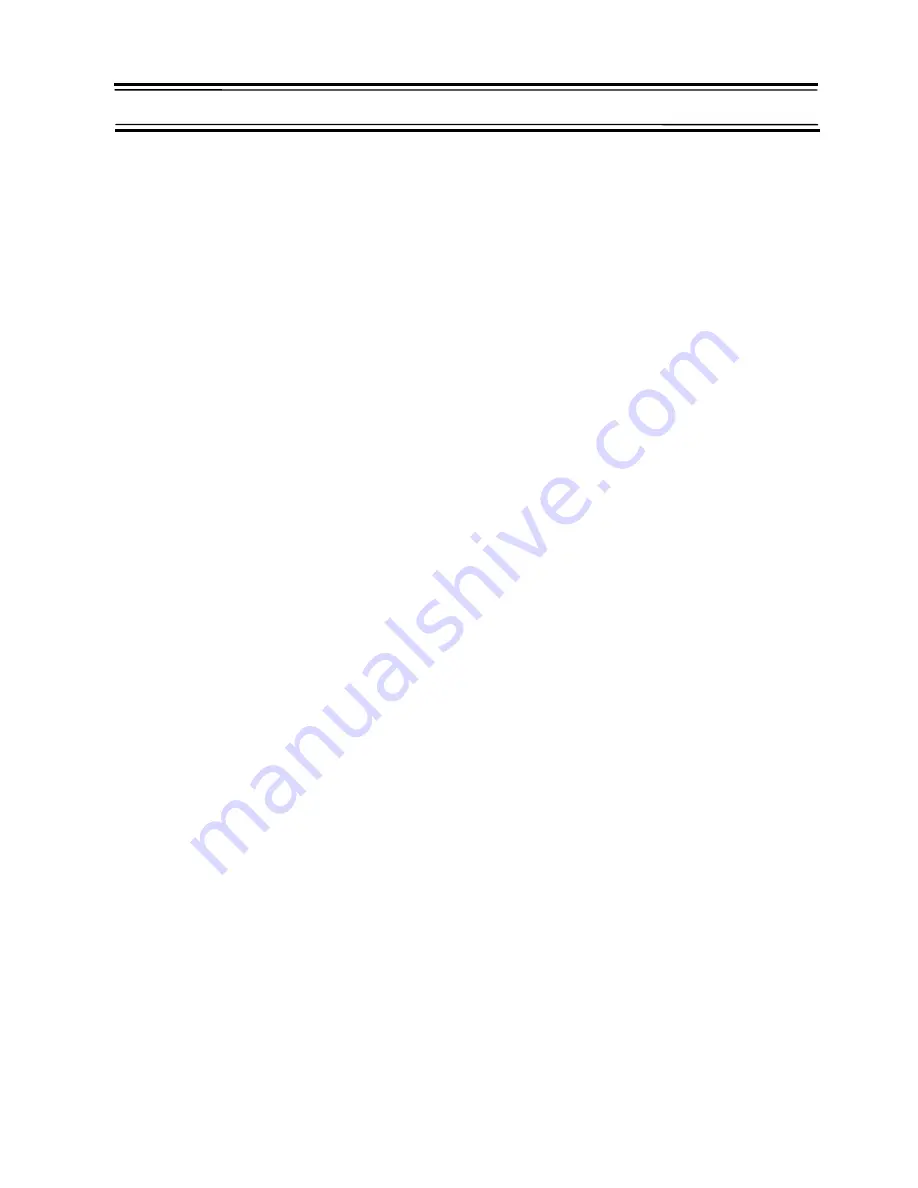
Page 23
tm2[G] TIMER – GATED MODE
The tm2(G) photogated reject timer gives precise
operation of the reject device where individual products,
eg cartoned products, individual chocolate bars etc are
transported on a conveyor. Photogating ensures that the
reject operation is independent of the position of metal
contamination within the product.
When setting up the timer there are some basic
rules that must be applied.
Sample Size
Small size metal contaminants should be used to
set the timer. The use of larger contaminants will produce
errors in the settings. Try to use the smallest metal
sample that can be detected. If this is not possible use
the smallest sample available and adjust the sensitivity
so that the sample gives an indication of 2 or 3 red bars
on the bar graph display.
Product Presentation
Sample product or packs used to set up the timer
should be passed through the detector at their normal
speed and without skewing or slippage.
Product Length
Where a variety of individual products with different
lengths are being inspected ensure that for a particular
timer setting .the variation in pack length does not exceed
+/-
25%
of the pack length used to set up the timer. Three
different timer settings are available, ie A, B, or C to
accommodate variations in pack length.
Window Time
Window time is the time period equal to 2 times the pack
length at normal conveyor speed. This time setting is
derived automatically in the set up process.
Sync Delay
Sync delay is the time taken for the pack to travel from
the photo beam to the optimum reject position.
Delay Time
Delay time is the time taken for a pack with a metal
contaminant in its rear/trailing edge to travel from the
metal detector and have its front/leading edge line up
with the centre of the reject device as it operates.
Reject Time
Reject time is the time required by the reject device to
reject a pack. The minimum value will be the operate time
of the reject device.
Selecting Photo-Electric Devices
Use a two part photo electric device, ie with separate
transmitter and receiver or with combined transmitter and
receiver and reflector. Avoid the use of photo electrics
that require the pack itself to reflect the beam.
Preferred types are infra red with a maximum current
demand of 30 milliamps. Other types may be used,
however, if they exceed the current limitations an
additional power supply will be required.
Light energised or dark energised systems may be used.
The metal detector will set itself automatically and
accommodate either mode during the calibration (CAL)
procedure.
The output device should normally be NPN open
collector, min voltage 15V, min current 10 milliamps. PNP
output devices can be accommodated by changing the
internal link arrangement in the detector head.
Positioning the Photo-Sensors
Position the photobeam on the conveyor at right angles
to flow of product along the conveyor
Summary of Contents for STANDARD SERIES
Page 11: ......
Page 22: ...Figure 6C Cable Gland Assemblies for Power Supply Unit Page 9A...
Page 23: ...Figure 8 Bearing Block Insulation Figure 7 Roller Shaft Insulation one end only Page 9B...
Page 24: ...THIS PAGE IS LEFT BLANK INTENTIONALLY Page 9C...
Page 25: ...Page 10...
Page 26: ......