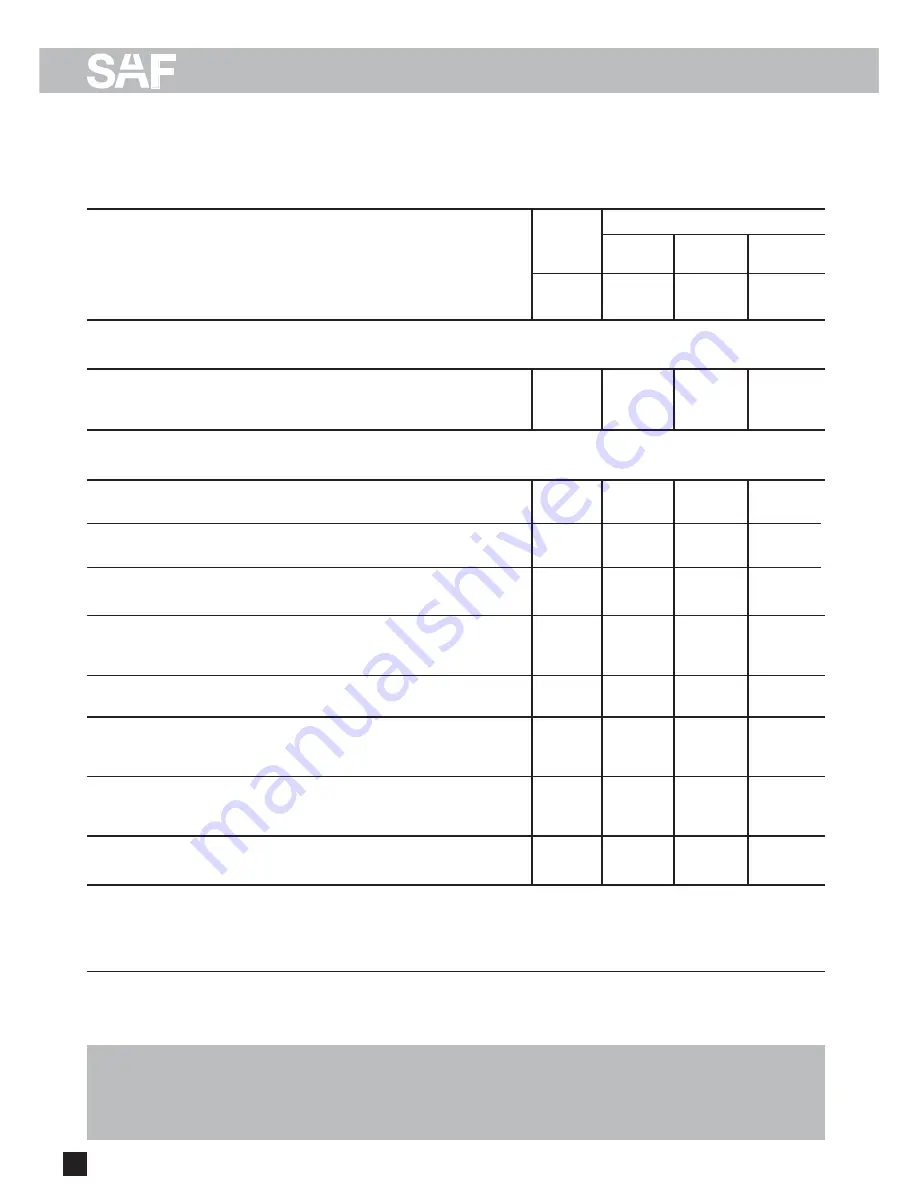
6
B) Maintenance instructions
SK 1000 Disc / ET 120
SK RB 9019 W - SK 1000 ET 120
Vehicles with long standing periods:
service at specified time intervals
Vehicles used under extreme conditions:
shorten the service interval to 6 months /
e.g. construction site operation, multi-shift operation
75,000 km
Maintenance intervals
whichever comes first
Mileage intervals
>
Time intervals
>
After first
5,000 km
or
every
30,000 km
every
150,000 km
After first
month
every
3 months
every
75,000 km
every
6 months
every
12 months
Periodic checks
Hub unit maintenance-free.
Visual inspection for grease leaks.
Inspect the brake caliper guide system.
Check for free movement and sliding action.
Check rubber dust covers for cracks and damages.
Check adjuster cap for correct seating.
Inspect the brake pad thickness
at regular intervals (e.g. when ever tyre pressure is checked)
but at least every 3 months.
Inspect the brake disc for cracks.
– Perform general annual inspection
(brakes, air bags, tyres, etc.)
– Perform general annual safety check
(tractor/ (semi-) trailer brake compatibility, ABS etc.)
Note:
Be sure to retighten wheel nuts to the
prescribed torque after the first 50 km and 150 km
(and after every wheel removal).
Mechanical check
Visual and safety inspection
Special service conditions
Warranty claims will only be accepted as long as the operating and maintenance instructions
have been complied with and if SAF approved spare parts have been fitted.
NOTE!
If the sealmark on the hub nut is broken before the end of the 1,000,000 km this will
invalidate all warranty coverage unless the repair works have been carried out in an
SAF-authorised workshop.
•
•
•
•
•
•
•
Summary of Contents for SK RB 9019 W
Page 4: ...NOTIZEN NOTES NOTE 4...