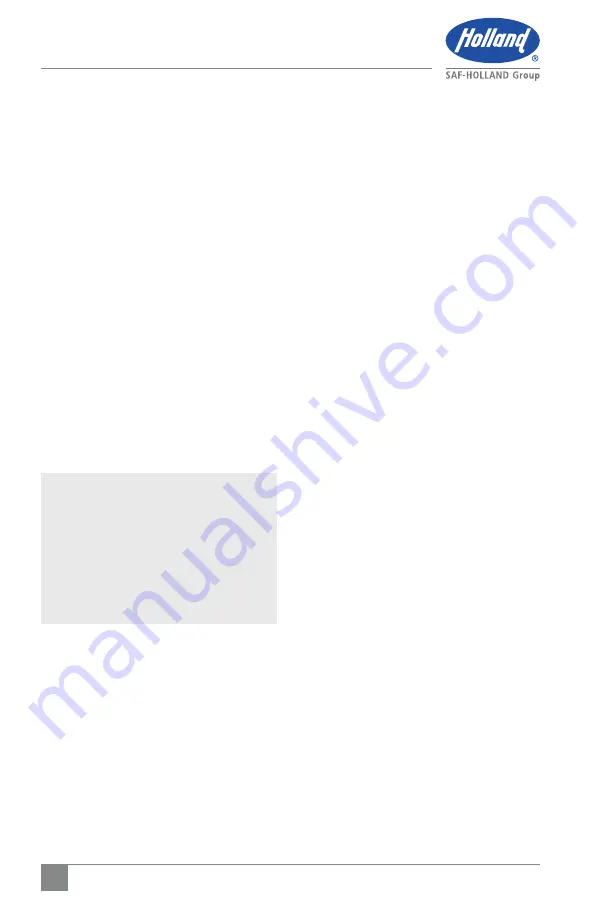
4
XL-DB20016UM-en-US Rev – · 2015-07-29 · Amendments and Errors Reserved · © SAF-HOLLAND, Inc., SAF-HOLLAND, HOLLAND, SAF,
and logos are trademarks of SAF-HOLLAND S.A., SAF-HOLLAND GmbH, and SAF-HOLLAND, Inc.
Welding Instructions
2. Welding Standards
2.1 Scope
When welding please observe the
requirements below. Customers may NOT
weld on SAF-HOLLAND
®
drawbars without
prior approval, including the application of
the American Welding Society standards by
SAF-HOLLAND
®
unless required for
installation. This specification applies to all
components supplied by SAF-HOLLAND
®
,
and its products. The customer assumes
all responsibility for weld integrity if weld
material and procedure differ from those
listed below.
2.2 Material
The SAF-HOLLAND
®
drawbar has been
manufactured from a modified AISI
weldable grade steel, and is intended for
welded installation with AWS filler metal
specification AWS A5.18, filler metal
classification ER-70S-3, ER-70S-6
or equivalent unless otherwise specified.
NOTE:
Any substitution for filler material
from the above standard MUST
comply, as a minimum, with the
following mechanical properties:
Tensile Strength - 72k psi (496 MPa)
Yield Strength - 60k psi (414 MPa)
Charpy V Notch - 20 ft.-lbs. (27 N•m)
at 0
o
F (-17.7
o
C)
% Elongation - 22%
The recommended welding gas for gas
metal arc welding (GMAW) is 90%
Argon/10% CO2. If a different gas is used,
welds MUST comply with penetration
requirements as illustrated below. Where
the installation directions specify different
than above, the directions shall prevail.
2.3 Procedures
Tack welds used for positioning components
are to be located in the center of the final
weld, where practical. Tack weld should
be completely fused to the finish weld.
DO NOT break arc at the end of the weld.
Back up all finish welds at least 1/2" (12 mm)
of a sufficient amount to prevent craters at
the end of the weld. Where weld is shown
to go around corners, it is assumed the
corner represents a stress concentration
area. DO NOT start or stop weld within
1" (25 mm) of the corner. Particular care
should be taken to prevent undercutting
in this area.
Take precautions and ensure NOT to damage
the vehicle electrical system during welding
by disconnecting any power sources, properly
grounding the vehicle, and shielding and
exposed wiring.
2.4 Workmanship
It is the responsibility of the customer to
provide good workmanship when attaching
components with welds.
2.5 Weld Size
If weld size is NOT specified, the effective
throat of the weld MUST be no smaller
than the thinnest material being welded
(Figure 1)
.