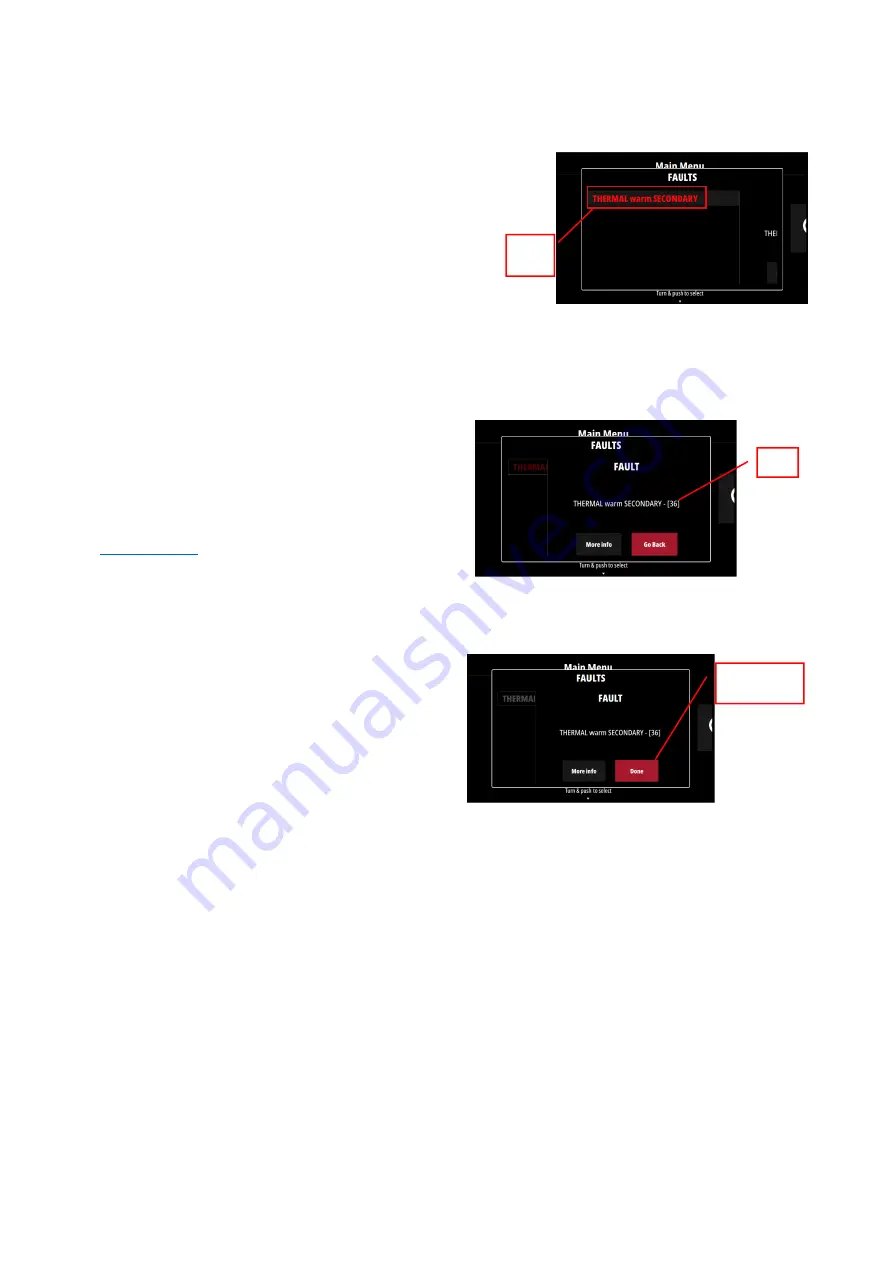
English 16 English
Customer Assistance Policy
The business of The Lincoln Electric Company is
manufacturing and selling high quality welding equipment,
consumables, and cutting equipment. Our challenge is to
meet the needs of our customers and to exceed their
expectations. On occasion, purchasers may ask Lincoln
Electric for advice or information about their use of our
products. We respond to our customers based on the best
information in our possession at that time. Lincoln Electric
is not in a position to warrant or guarantee such advice,
and assumes no liability, with respect to such information
or advice. We expressly disclaim any warranty of any
kind, including any warranty of fitness for any customer’s
particular purpose, with respect to such information or
advice. As a matter of practical consideration, we also
cannot assume any responsibility for updating or
correcting any such information or advice once it has
been given, nor does the provision of information or
advice create, expand or alter any warranty with respect
to the sale of our products
Lincoln Electric is a responsive manufacturer, but the
selection and use of specific products sold by Lincoln
Electric is solely within the control of, and remains the sole
responsibility of the customer. Many variables beyond the
control of Lincoln Electric affect the results obtained in
applying these types of fabrication methods and service
requirements.
Subject to Change – This information is accurate to the
best of our knowledge at the time of printing. Please refer
to
www.saf-fro.com
for any updated information.
Error Codes and troubleshooting
When the error occurs and remains, the Error messages
is displayed in Red.
By pushing the knob button, the Error code number is
displayed.
During error, new welding sequence is blocked until the
reason of error remains.
When the error vanished, it is now possible to
acknowledge the error by pushing the knob. The
background error message becomes white
Table 1 shows list of basic errors that can appear. To get
full list of error codes, please contact local service.
Type of
error
Error
code
“Done”, starting a
new sequence is
possible