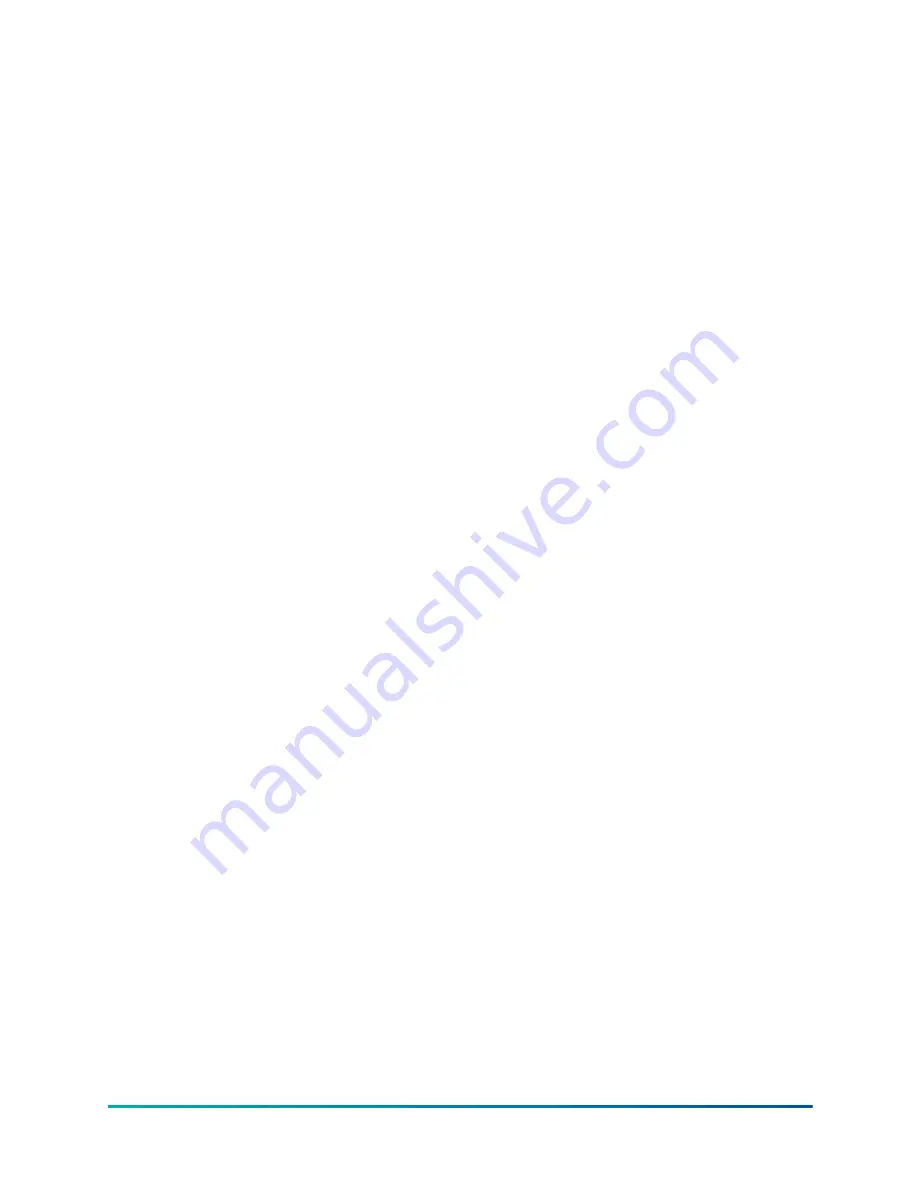
Sound and noise data......................................................................................................................... 34
Noise data................................................................................................................................................... 34
Noise data for SAB 283 and SAB 355....................................................................................................... 34
Installation...................................................................................................................................................... 35
ATEX.......................................................................................................................................................36
Operating instructions.................................................................................................................................. 37
Description of the unit........................................................................................................................ 37
Control system........................................................................................................................................... 37
Principle drawing....................................................................................................................................... 37
General P&I diagram...........................................................................................................................40
P&I diagram - liquid injection............................................................................................................ 43
Valve positions during operation.............................................................................................................44
Descriptions of main components and systems............................................................................. 45
Compressor..........................................................................................................................................45
Compressor lubrication system.........................................................................................................46
No pump oil system............................................................................................................................ 47
Demand pump oil system.................................................................................................................. 47
Compressor oil separation system....................................................................................................47
Automatic oil return valve.................................................................................................................. 48
Function.......................................................................................................................................................48
Cold-start system.................................................................................................................................49
High-stage units.........................................................................................................................................50
Booster applications..................................................................................................................................50
Compressor hydraulic system............................................................................................................51
Single-acting mode, high-stage (> 10 bar pressure differential)......................................................... 52
High-stage compressor loading...............................................................................................................52
High-stage compressor unloading.......................................................................................................... 52
Double-acting mode, booster (< 10 bar pressure differential)............................................................ 52
Booster compressor loading.................................................................................................................... 53
Booster compressor unloading................................................................................................................53
Volumizer volume ratio (VI) control.................................................................................................. 53
Compressor VI increase......................................................................................................................53
Compressor VI decrease.....................................................................................................................54
Compressor oil cooling systems........................................................................................................54
Liquid injection........................................................................................................................................... 54
Suction check valve by-pass............................................................................................................... 54
Balance piston pressure regulator....................................................................................................55
Low ambient temperature operation............................................................................................... 57
Heating element.................................................................................................................................. 57
ATEX............................................................................................................................................................. 57
Start-up................................................................................................................................................. 57
Preparations before start-up....................................................................................................................57
SAB 283-355 A-Frame OHU 6042 and OHU 7650 (including ATEX) Screw Compressor Unit
4