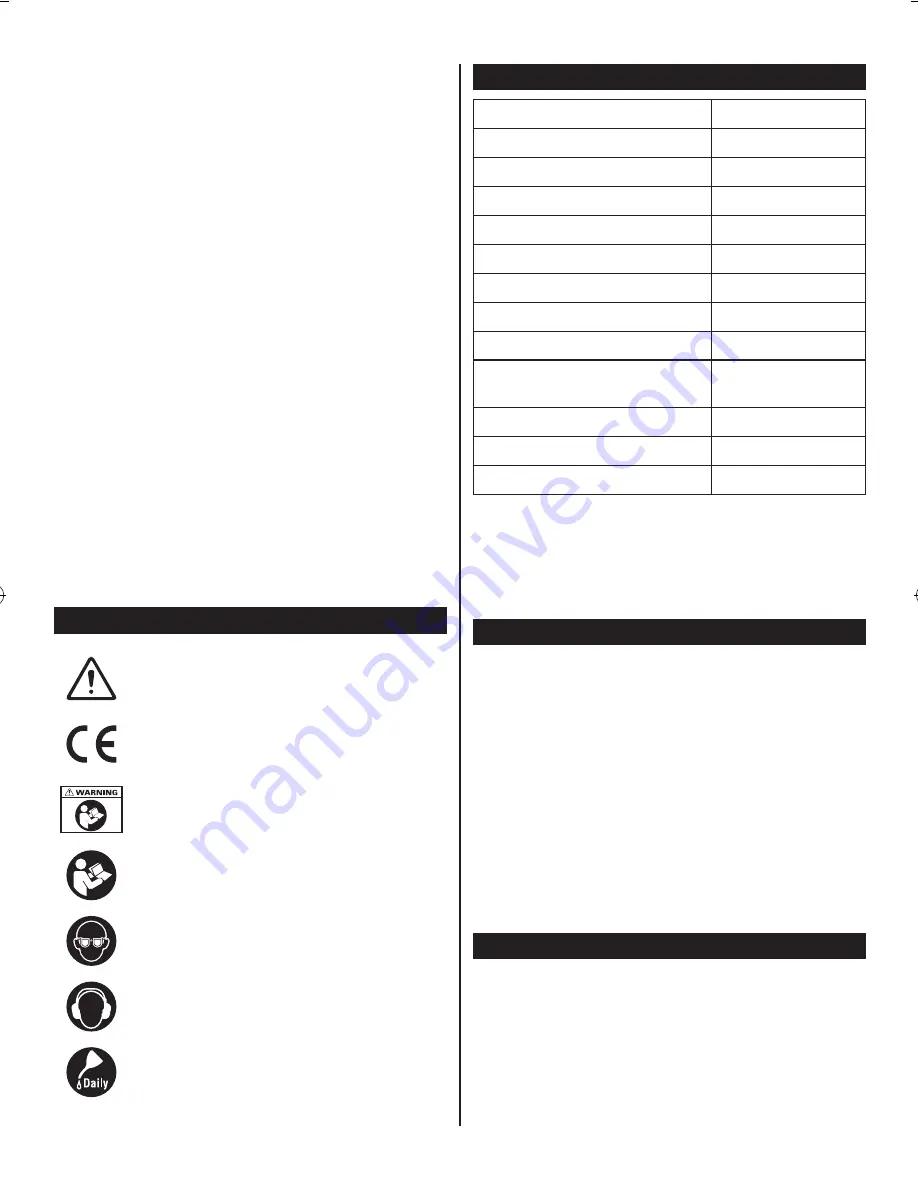
3
ADDITIONAL SAFETY INSTRUCTIONS FOR PNEU-
MATIC POWER TOOLS
■
Air under pressure can cause severe injury.
■
Always shut off air supply, drain hose of air pressure
and disconnect tool from air supply when not in use,
before changing accessories or when making repairs;
■
Never direct air at yourself or anyone else.
■
Whipping hoses can cause severe injury. Always
check for damaged or loose hoses and fittings.
■
Cold air shall be directed away from the hands.
■
Do not use quick-disconnect couplings at tool inlet
for impact and air-hydraulic impulse wrenches. Use
hardened steel (or material with comparable shock
resistance) threaded hose fittings.
■
Whenever universal twist couplings (claw couplings)
are used, lock pins shall be installed and whipcheck
safety cables shall be used to safeguard against
possible hose-to-tool and hose-and-hose connection
failure.
■
Do not exceed the maximum air pressure stated on
the tool.
■
For torque-control and continuous-rotation tools, the
air pressure has a safety critical effect on performance.
Therefore, requirements for length and diameter of the
hose shall be specified.
■
Never carry an air tool by the hose.
SYMBOLS
Safety alert
CE conformity
Please read and understand all instructions
before operating the product, follow all
warnings and safety instructions.
Please read the instructions carefully before
starting the product.
Wear eye protection.
Wear ear protection.
Lubricate with air tool oil daily.
SPECIFICATIONS
Square drive
12.7 mm (1/2”)
Capacity bolt size
16 mm (5/8”)
No-load speed
7,800/min
Max. torque
569 N.m
Avg. air consumption
184 L (6.5 cfm)
Maximum working pressure
6.3 bar (90 psi)
Air inlet size
6.35 mm (1/4”)
Air hose ID
9.52 mm (3/8”)
Weight
2.1 kg
A-weighted sound pressure
level
95.1dB(A), k=3dB
Sound power level
106.1dB(A), k=3dB
Vibration value
5.778 m/s
2
Uncertainty
1.33 m/s
2
Noise emission values are in accordance with
EN ISO 4871 and EN ISO 15744.
Vibration emission values are in accordance with
EN12096, EN28662-1 and EN ISO 8662-7.
APPLICATION
The product comes with durable twin-hammer impact
wrench mechanism, pressure-feed lubrication, adjustable
power regulator, variable speeds, high torque, front
exhaust, sheer power and performance features to tackle
the toughest jobs with ease and proven durability and
economy. The product is used as a wrench. Any other use
is forbidden.
– Used for tires, suspension, frames and other
heavy duty automobile works
– Twin hammer mechanism provides more power,
smooth torque transfer and low vibration
– Lightweight composite material housing and
aluminum front housing
– Soft grip for extra comfort and control
RESIDUAL RISKS
Even if you are operating this product in accordance
with all the safety requirements, potential risks of injury
and damage remain. The following dangers can arise in
connection with the structure and design of this product:
1. Health defects resulting from vibration and noise
emission if the product is being used over long periods
of time or not adequately managed and properly
maintained.