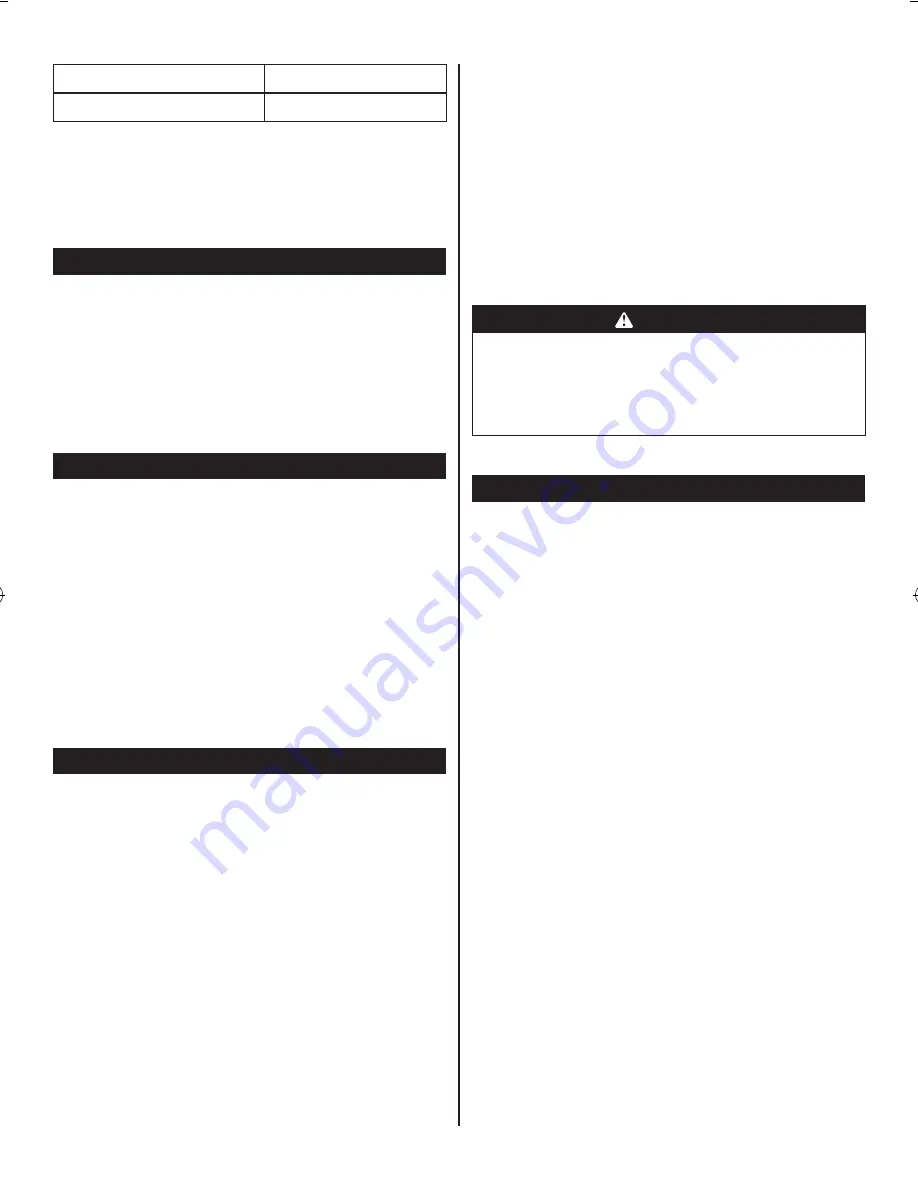
4
Vibration value
1.67 m/s
2
Uncertainty
0.26 m/s
2
Noise emission values are in accordance with
EN ISO 4871 and EN ISO 15744.
Vibration emission values are in accordance with
EN12096 and EN28662-1.
APPLICATION
The product is ideal for cutting-off operation. The durable
and lightweight composite housing design also helps
reduce vibration. It has a lever lock throttle for safety. Any
other use is forbidden.
The product can cut aluminum, plastic, fiber-glass and
steel. A chrome-plated safety guard and a safety latch
protect the user against injury. A safety lock mechanism
prevents accidental start-ups.
RESIDUAL RISKS
Even if you are operating this product in accordance
with all the safety requirements, potential risks of injury
and damage remain. The following dangers can arise in
connection with the structure and design of this product:
1. Health defects resulting from vibration and noise
emission if the product is being used over long periods
of time or not adequately managed and properly
maintained.
2. Injuries and damage to property due to broken cutting
attachments or the sudden impact of hidden objects
during use.
3. Danger of injury and property damage caused by
flying objects.
AIR SUPPLY AND OPERATION
■
Ensure air valve (or trigger) is in the “off” position
before connecting to the air supply.
■
Connect the product to the air hose.
■
Press the trigger to operate the product.
■
The air regulator controls the amount of air flow
entering the rotor. Turn the air regular adjustment
knob to decrease/increase the speed of the product.
■
Do not allow the product to free run for an extended
period of time as this will shorten its life.
■
There is a risk of excessive vibration levels due to
improper mounting or damage of insert tool.
■
There is a risk of running on of the inserted tool after
the start and stop device has been released.
■
Only permitted insert tools of the correct diameter are
used.
■
Release the start and stop device in the case of an
interruption of the air supply.
■
Disconnect the product from the air supply before
changing accessories or making adjustments.
■
Required air pressure of 6.3 bar (90 psi), and an air
flow according to specifications.
■
Attach the cutting off wheel, lock washer and lock
washer nut to the collet.
■
Tighten the lock washer nut to secure the cutting off
wheel by the provided hex key and wrench.
■
Before operation, ensure the inserted tool is fixed in
the product.
WARNING
Ensure the air supply is clean and does not exceed
6.3 bar (90 psi) while operating the product. Too high an
air pressure and unclean air will shorten the product's
life due to excessive wear, and may be dangerous
causing damage and/or personal injury.
LUBRICATION
An
automatic
in-line
filter-regulator-lubricator
is
recommended (Fig. 7) as it increases product life and keeps
the product in sustained operation. The in-line lubricator
should be regularly checked and filled with air tool oil.
Proper adjustment of the in-line lubricator is performed by
placing a sheet of paper next to the exhaust ports and
holding the throttle open for approximately 30 seconds.
The lubricator is properly set when a light stain of oil
collects on the paper. Excessive amounts of oil should be
avoided.
If it becomes necessary to store the product for an extended
period of time (overnight, weekend, etc.), it should receive
a generous amount of lubrication at that time. The product
should be run for approximately 30 seconds to ensure oil
has been evenly distributed throughout the product. The
product should be stored in a clean and dry environment.
●
It is most important that the product be properly
lubricated by keeping the air line lubricator filled
and correctly adjusted. Without proper lubrication
the product will not work properly and parts will
wear prematurely.
●
Use correct lubricant in the air line lubricator. The
lubricator should be of low air flow or changing air
flow type, and should be kept filled to the correct
level. Use only recommended lubricants, specially
made for pneumatic applications. Substitutes
may harm the rubber compounds in the product's
O-rings and other rubber parts.