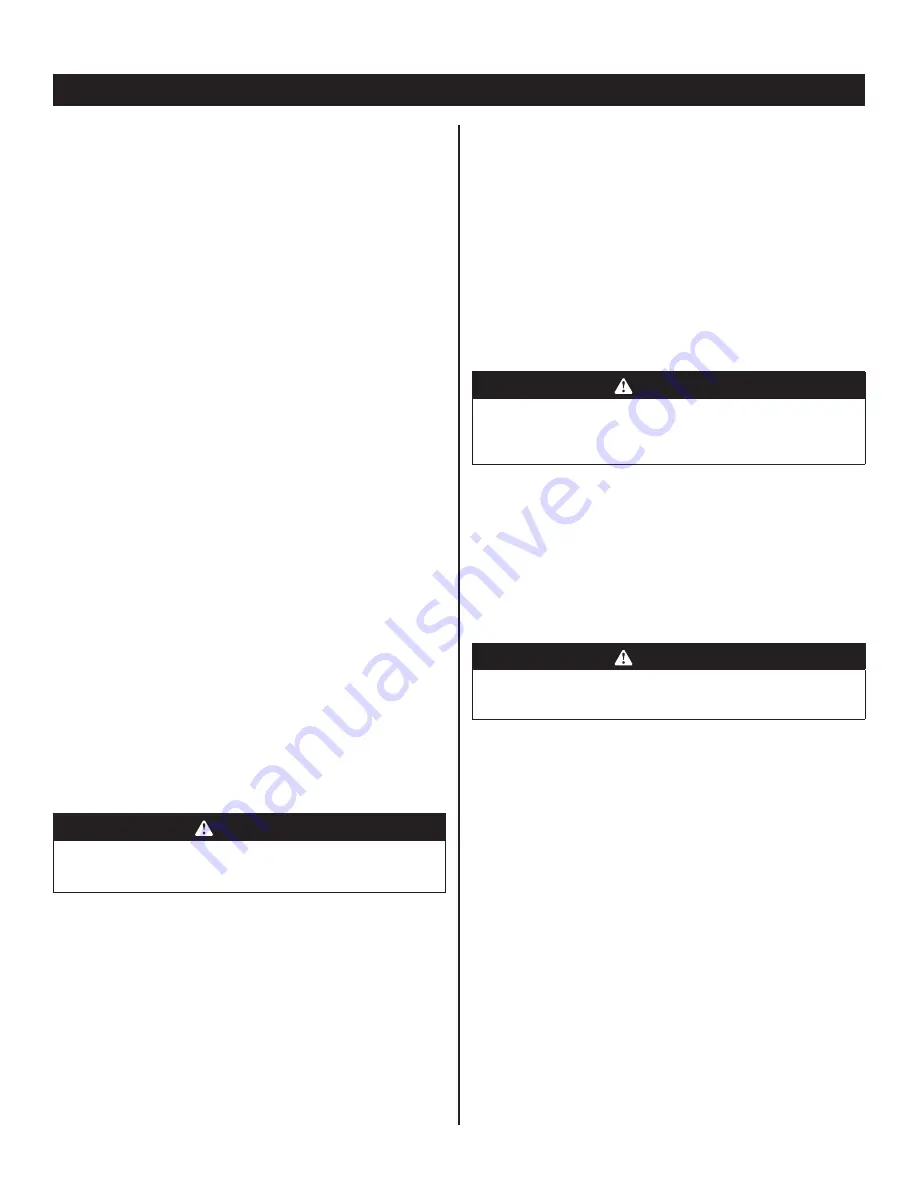
4
English
Tighten the screw to install the adjusting guide on the
tool base plate. Loosen the wing bolt to adjust the guide.
Then tighten the screw fi rmly to fi x the adjusting guide at
a required distance.
Install the guide into the base by bolt A. Adjust the distance
between the bit and base by bolt B, then fasten by bolt C.
When using the tool, please keep the guide mounted on
the workpiece edge.
A bit/cutter guard is attached to protect users from
contacting the bit/cutter when adjusting the fence.
DEPTH OF CUT
See fi gure 9
As previously mentioned, the depth of cut is important
because it affects the rate of feed which, in turn, affects
the quality of a cut (and also, the possibility of damage
to your trimmer motor and cutter). A deep cut requires
a slower feed than a shallow cut and a too deep cut will
cause you to slow the feed so much that the cutter is no
longer cutting.
Making a deep cut is never advisable. The smaller cutters
especially those only 1.6 mm in diameter are easily broken
when subjected to too much side thrust. A large cutter
may not break, but if the cut is too deep a rough cut will
result and it may be very diffi cult to guide and control the
cutter as desired. For these reasons, we recommend that
you do not exceed 3 mm depth of cut in a single pass,
regardless of the cutter size or the softness or condition
of the workpiece. This will result in a higher quality cut.
To make deeper cuts it is therefore necessary to make as
many successive passes as required, lowering the cutter
3 mm for each new pass. In order to save time, do all the
cutting necessary at one depth setting, before lowering the
cutter for the next pass. This will also ensure a uniform
depth when the fi nal pass is completed.
WARNING
If desired depth of cut is greater than can be safely cut
in one pass, make cuts in two or more passes.
DIRECTION OF FEED AND THRUST
See fi gure 10
The trimmer motor and cutter revolve in a clockwise
direction. This gives the tool a slight tendency to twist (in
your hands) in a counterclockwise direction, especially
when the motor starts.
Because of the extremely high speed of cutter rotation
during “proper feeding” operation, there is very little
kickback under normal conditions. However, should the
cutter strike a knot, hard grain, foreign object etc, that
would affect the normal progress of the cutting action,
there will be a slight kickback — suffi cient to spoil the
trueness of your cut if you are not prepared. Such a
kickback is always in the direction opposite to the direction
of cutter rotation.
To guard against such kickback, plan your setup and
direction of feed so that you will always be thrusting the
tool to hold it against whatever you are using to guide the
cut in the same direction that the leading edge of the cutter
is moving. In short, the thrust should be in a direction that
keeps the sharp edges of the cutter continuously biting
straight into new (uncut) timber.
WARNING
When servicing use only identical replacement parts.
Use of any other parts may create a hazard or cause
product damage.
BRUSH REPLACEMENT
See fi gure 11
Your trimmer has externally accessible brush assemblies
that should periodically be checked for wear. Proceed as
follows when replacement is required:
Unplug your trimmer.
WARNING
Failure to unplug your trimmer could result in accidental
starting causing serious injury.
Remove the brush cap with a flat blade screwdriver.
Brush assembly is spring loaded and will pop out when
you remove the brush cap.
Remove the brush assembly (brush and spring).
Check for wear. If worn, always replace in pairs. Do
not replace one side without replacing the other.
Reassemble using new brush assemblies. Make sure
curvature of brush matches curvature of motor and
that the brush moves freely in the brush tube.
Make sure the brush cap is oriented correctly (straight)
and replace.
Tighten the brush cap securely. Do not over tighten.
PROPER CARE OF CUTTERS
Get faster more accurate cutting results by keeping cutters
clean and sharp. Remove all accumulated pitch and gum
from cutters after each use. When sharpening cutters,
sharpen only the inside of the
Cutting edge. Never grind the outside diameter. Be sure