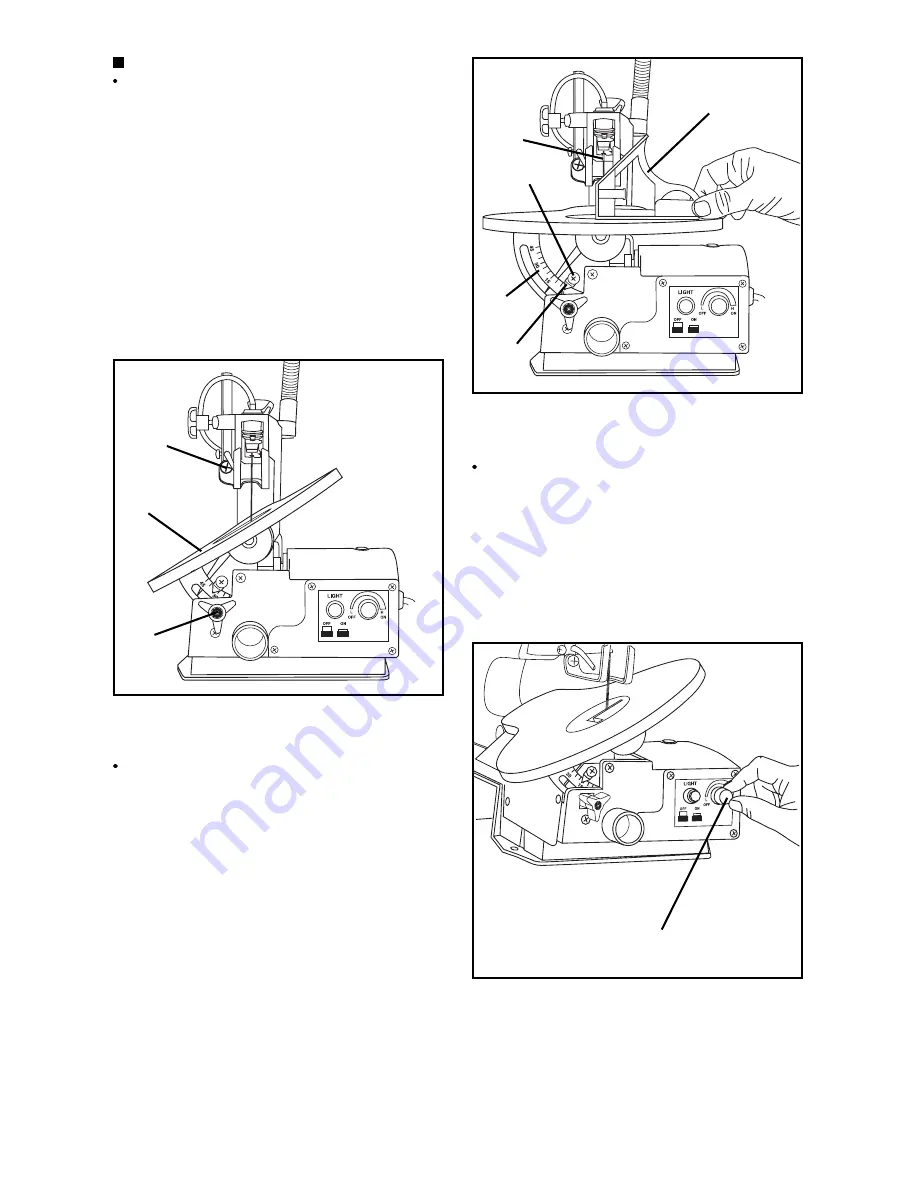
OPERATING ADJUSTMENTS
SETTING THE TABLE FORHORIZONTAL OR BEVEL
CUTTING.
1. Loosen the table lock knob, and the saw table can be
tilted to the left and locked at any angle from 0˚horizontal
cutting position up to 45˚ for bevel cutting.
2. A degree scale is also provided under the work table as
a convenient reference for setting the approximate table
angle for bevel cutting. When greater precision is required,
make prac-tice cuts and adjust the table as necessary for
your requirements.
3. NOTE: When cutting at angles, the drop foot can be tilted
so it’s parallel to the table and rests flat against the
workpiece. To tilt drop foot, loosen allen screw, tilt foot so
it’s parallel to table and securely tighten screw.
ALIGNING THE DEGREE SCALE POINTER
1. Loosen the table lock knob, and move the table until it is
approximately perpendicular, or at a right angle to the blade.
2. Place a small square on the table next to the blade as
shown to check if the table is 90˚ to the blade. If adjustment
is needed, raise or lower the table until table is approxi-
mately 90˚ to the blade and securely tighten the table lock
knob.
3. Loosen the screw holding the degree scale pointer as
shown, move pointer to the 0˚ mark and securely tighten
screw. Remember, the degree scale is a convenient guide
but should not be relied upon for precision. make practice
cuts in scrap pieces of wood to determine if your angle set-
tings are correct.
ON/OFF AND VARIABLE SPEED SWITCH
The On/Off switch of your scroll saw also features variable
speed control which allows you to regu-late the correct
speed for the material and shape to be cut.
For straight cutting, turn the switch clockwise to high speed.
For intricate pattern cutting, turn the switch anti-clockwise
to low speed.
On/Off and Variable Speed Switch
Blade
Pointer
Adjustment
Screw
Degree
Scale
Pointer
Square
Phillips
Screw
Table
Table
Lock
Knob
Page 5