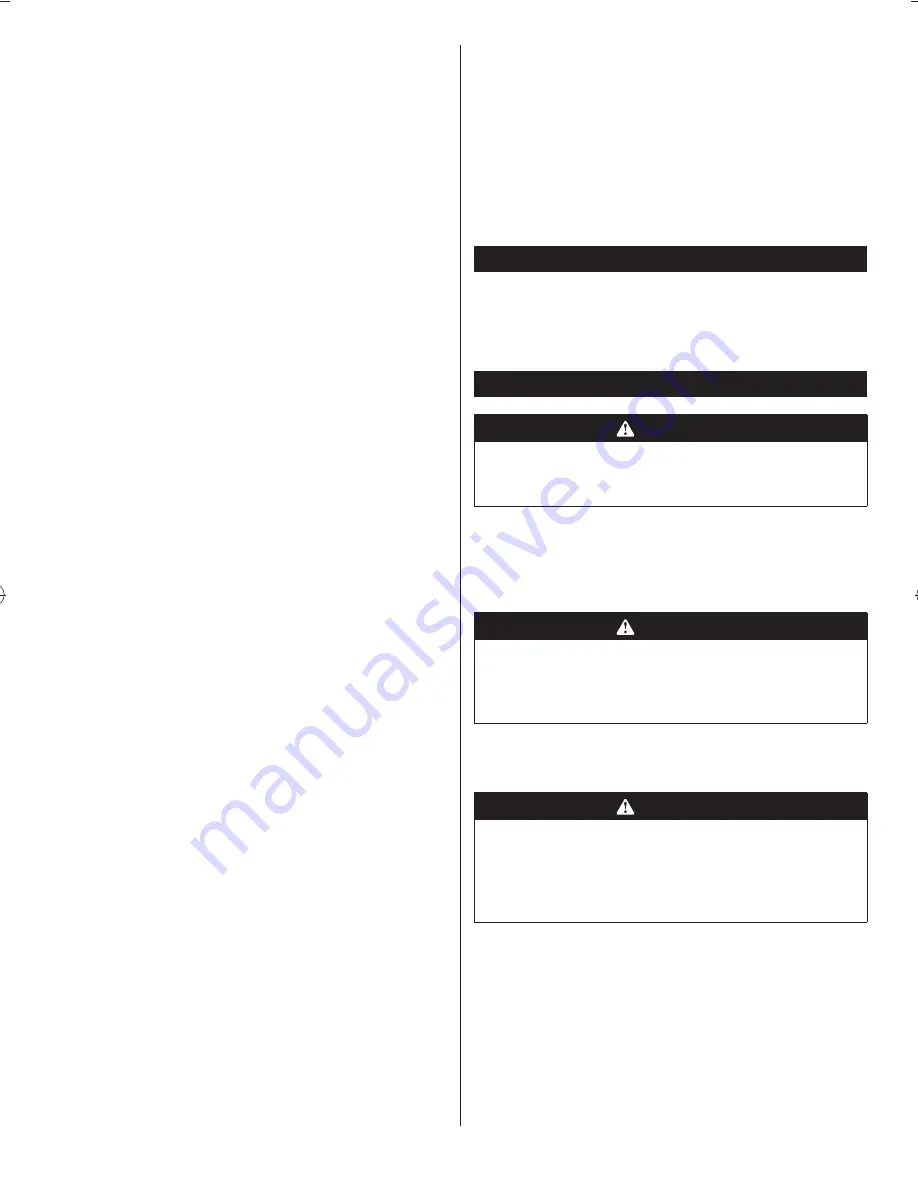
7
preventing further rotation.
With the spindle lock engaged, use the collet wrench
to loosen the collet nut, if necessary.
Remove collet nut and collet.
Insert the 1/8 in. collet.
Replace and tighten the collet nut.
Insert drive shaft into collet nut until the collar meets
the collet nut.
Tighten the collet nut completely, keeping collar in
contact with the collet nut.
Insert cup end of flex shaft onto tool head. Turn
clockwise to tighten.
To install accessories into the fl ex shaft:
Unplug the rotary tool.
Locate the hole behind the collet nut in the flex shaft
body.
Turn the collet nut until the hole in the flex shaft body
aligns with the hole visible inside the flex shaft.
Insert provided locking key into the aligned holes to
lock collet nut into place.
Insert the shank of the accessory into the collet nut
until the shank bottoms out, then pull it out 1/16 in. to
allow for expansion when the accessory gets hot.
With the key still in place, tighten the collet nut with the
provided wrench until the accessory shank is gripped
by the collet. Avoid excessive tightening of the collet
nut.
Remove the key.
To remove accessories from the fl ex shaft:
Unplug the rotary tool.
Locate the hole behind the collet nut in the flex shaft
body.
Turn the collet nut until the hole in the flex shaft body
aligns with the hole visible inside the flex shaft.
Insert provided locking key into the aligned holes to
lock collet nut into place.
With the key still in place, loosen the collet nut with the
provided wrench.
Remove the accessory.
To operate the rotary tool using the fl ex shaft:
Secure all work in a vise or clamp to a workbench to
prevent it from moving under the tool.
Grip the flex shaft along the grooved gripping section.
Hold the tool in front and away from you, keeping the
tool accessory clear of the workpiece.
Turn on the tool and let the motor and accessory build
up to full speed.
Lower the tool gradually until the accessory contacts
the workpiece.
Move the tool continuously at a steady, consistent
pace.
Use just enough pressure to keep the tool from
chattering or bouncing.
NOTE:
Heavy pressure will decrease the tool’s speed and
put a strain on the motor. The weight of the tool alone is
adequate for most jobs.
Lift the tool away from the workpiece before turning
off the tool.
LIVE TOOL INDICATOR
This tool features a live tool indicator which illuminates as
soon as the tool is connected to the supply. This warns the
user that the tool is connected and will operate when the
switch is pressed.
MAINTENANCE
WARNING
When servicing, use only identical replacement parts.
Use of any other part may create a hazard or cause
product damage.
Avoid using solvents when cleaning plastic parts. Most
plastics are susceptible to damage from various types of
commercial solvents and may be damaged by their use.
Use clean cloths to remove dirt, dust, oil, grease, etc.
WARNING
Do not at any time let brake fl uids, gasoline, petroleum-
based products, penetrating oils, etc., come in contact
with plastic parts. They contain chemicals that can
damage, weaken or destroy plastic.
Do not
abuse power tools. Abusive practices can damage
tool as well as workpiece.
WARNING
Do not attempt to modify this tool or create accessories
not recommended for use with this tool. Any such
alteration or modifi cation is misuse and could result
in a hazardous condition leading to possible serious
personal injury.
Electric tools used on fi berglass material, wallboard,
spackling compounds, or plaster are subject to
accelerated wear and possible premature failure because
the fi berglass chips and grindings are highly abrasive to
bearings, brushes, commutators, etc. Consequently, we
do not recommend using the product for extended work
on these types of materials. However, if you do work with
any of these materials, it is extremely important to clean
the product using compressed air.