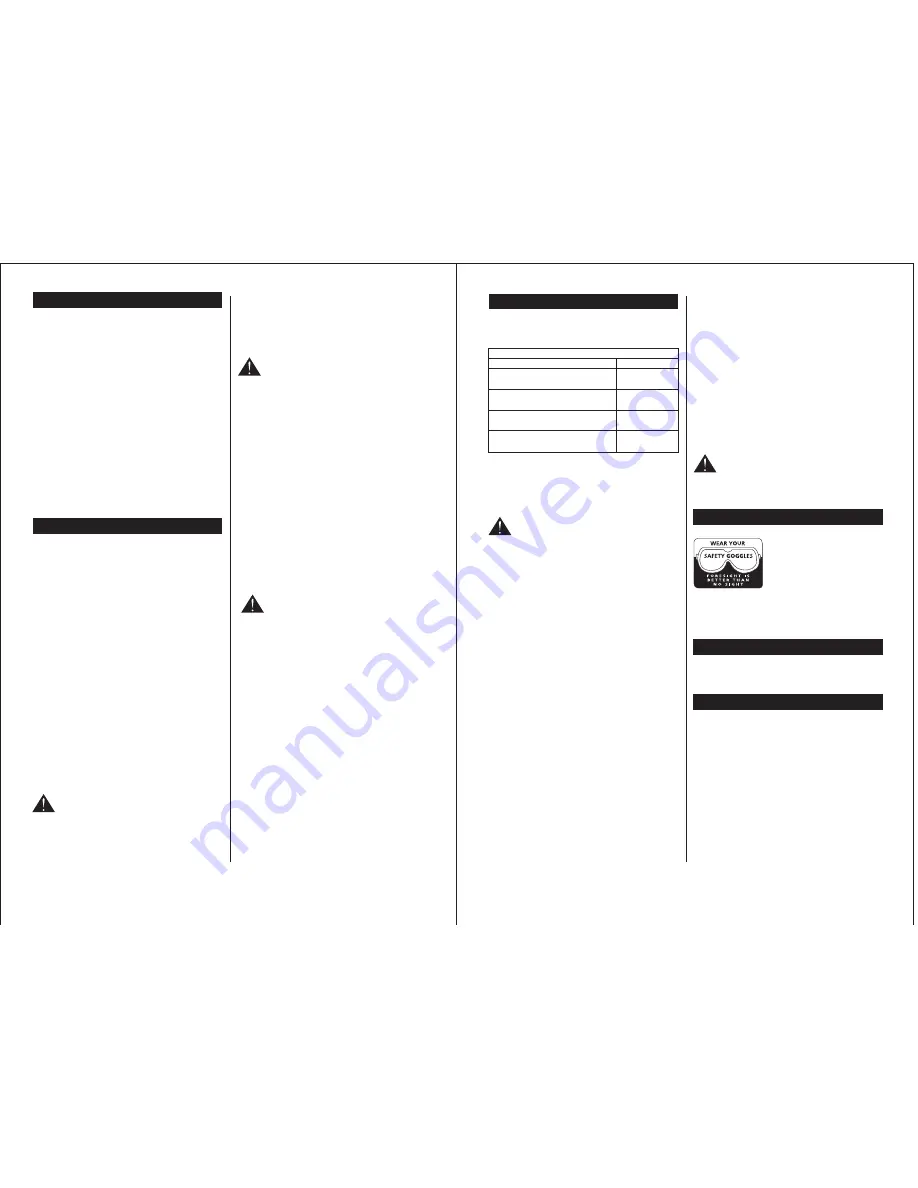
7
ASSEMBLY
Operation:
Refinishing painted wood or metal surfaces.
T
I
R
G
S
K
R
A
M
E
R
To remove paint and to smooth
Coarse
surface irregularities.
16-24-30
m
u
i
d
e
M
h
t
o
o
m
s
o
T
the rough sanding.
36-50-80
To remove scratches left by
Fine
0
2
1
-
0
0
1
.
s
c
si
d
s
u
o
iv
e
r
p
To smooth surfaces for painting,
Very Fine
polishing or waxing.
150-180
6
WARNING
Hold the tool with both hands while starting
the tool, since torque from the motor can
cause the tool to twist.
WARNING
Before using a grinding wheel, be certain
that its maximum safe operating speed is
not exceeded by the nameplate speed of
the grinder. Do not exceed the
recommended wheel diameter.
WARNING
Excessive or sudden pressure on the
wheel will slow grinding action and put
dangerous stresses on the wheel.
WARNING
If the disc (accessory) is held flat or the
back edge of the disc comes in contact
with the work, a violent thrust to the side
may result.
WARNING
Avoid bouncing and snaging the wire
brush, especially when working corners,
sharp edges etc. This can cause loss of
control and kick-back.
OPERATION
OPERATION
SYMBOL
STORAGE AND HANDLING OF ACCESSORIES
■
Use clamps or other practical way to secure
and support the workpiece to a stable
platform.
Holding the work by hand or against
your body leaves it unstable and may lead to
loss of control.
■
It is recommended that the tool always be
supplied via a residual current device with a
rated residual current of 30mA or less.
SLIDE ON-OFF SWITCH WITH LOCK
■
The tool is switched “ON” by the switch button
located at the top of the motor housing. The
switch can be locked in the “ON” position, a
convenience for long grinding operations.
■
To turn the tool “ON” without locking it, push and
slide the switch button forward by applying
pressure ONLY at the REAR portion of the
button. When pressure is released the switch
button will snap to “OFF” position.
■
To lock the switch “ON”, slide the switch button
forward and press “IN” the FRONT portion.
■
To unlock the switch, simply press and release
the REAR portion of the button. Switch is spring
loaded and will snap back automatically.
(Fig.5)
■
Start the tool before applying to work and let the
tool come to full speed before contacting the
workpiece. Lift the tool from the work before
releasing the switch. DO NOT turn the switch
“ON” and “OFF” while the tool is under load; this
will greatly decrease the switch life.
GRINDING OPERATIONS
SELECTING GRINDING WHEELS
DISC GRINDING WHEELS
■
Grinding wheels should be carefully selected in
order to use the grinder most efficiently. Wheels
vary in type of abrasive, bond, hardness, grit
size and structure. The correct type of wheel to
use is determined by the job. Use disc grinding
wheels for fast grinding of structural steel, heavy
weld beads, steel casting, stainless steel and
other ferrous metals.
GRINDING TIPS
■
Efficient grinding is achieved by controlling the
pressure and keeping the angle between wheel
and workpiece at 10° to 15°. If the wheel is flat,
the tool is difficult to control. If the angle is too
steep, the pressure is concentrated on a small
area causing burning to the work surface.
■
When grinding with a new wheel be certain to
grind while pulling tool backwards until wheel
becomes rounded on its edge. New wheels
have sharp corners which tend to “bite” or cut
into workpiece when pushing forward.
SANDING OPERATIONS
SELECTING SANDING DISC
■
Sanding discs are made of extremely hard and
sharp aluminum oxide grits, phenol-resin
bonded to a sturdy fiber backing for fast
heavy-duty service and long life. The discs vary
as to size and spacing of the abrasive grits.
OPEN COAT (type H) — used for soft materials
and on paint or varnish. CLOSED COAT (type
K) —used for metal, hardwood, stone, marble
and other materials.
■
Sanding discs range in grit from 16 (very
coarse) to 180 (very fine). To obtain best results,
select sanding discs carefully. Many jobs require
the use of several grit sizes and at times both
“open coat and closed coat” discs are required
to get the job done faster. See chart for
application examples.
SANDING TIPS
■
For best results, tilt the Disc Sander at a 10° to
15° angle while sanding so that only about 1" of
the surface around the edge of the disc contacts
the work.
■
If sander is tilted too much, sanding action will
be too great and a rough cut surface or gouging
and snagging will result.
■
Guide the Disc Sander with crosswise strokes.
Be careful not to hold the sander in one spot too
long. Do not use a circular motion, as this
makes swirl marks. Test before use on scrap
stock.
■
Do not force or apply pressure when sanding.
Use only the weight of the tool for pressure.
■
Excess pressure actually slows the tool down. If
faster stock removal is desired, change to a
coarser grit disc.
■
Remove gummy paint from metal with an “open
coat” disc. Sand until sparks start to appear,
then stop and change to a “closed coat” disc to
remove any remaining paint.
SANDING WOOD
■
When sanding wood the direction of the disc
motion at the contact point should parallel the
grain as much as possible. The rapid cut of
discs and the swirl type scratch pattern they
occasionally create generally prohibit their use
for producing the final finish.
■
Scratches and circular marks are usually the
result of using too coarse a grit. When changing
to a finer grit, move across the sanding lines
that were made by a previous coarser disc.
SANDING METAL
■
When sanding automobiles or appliances, wipe
the metal clean with a non-flammable solvent or
commercial cleaner to remove all wax and
grease. By doing this first, the sanding discs will
sand better and last longer.
■
For heavy duty work, use a coarse grit disc first.
Follow-up with a medium grit to remove
scratches. To produce smooth finish, use fine
grit disc.
WIRE BRUSH OPERATIONS
■
Wire brushes are intended to “clean” structural
steel, castings, sheet metal, stone and concrete.
They are used to remove rust, scale and paint.
TOOL LUBRICATION
■
Your tool has been properly lubricated and is
ready to use. It is recommended that tools with
gears be regreased with a special gear lubricant
at every carbon brush change.
CARBON BRUSHES
■
The brushes and commutator in your tool have
been engineered for many hours of dependable
service. To maintain peak efficiency of the
motor, we recommend every two to six months
the brushes be examined. Only genuine RYOBI
replacement brushes specially designed for your
tool should be used.
MAINTENANCE
sanding disc on top of the backing pad. Insert
the lock nut through the disc and thread onto the
spindle as far as you can with your fingers.
Press in the spindle lock, then tighten the
backing pad securely with the lock nut spanner.
(Fig.4)
TO REMOVE BACKING PAD AND SANDING
DISC
■
Disconnect tool from power source. Using
the lock nut spanner unscrew the nut from the
spindle, while holding spindle lock in.
WIRE BRUSH ASSEMBLY (Fig.4)
■
Before assembling wire brush to this tool,
disconnect from the power source. Wire brushes
are equipped with their own threaded hub,
simply thread on to spindle. Be sure to seat
against shoulder before turning tool “ON”.
The operation of any tool can
result in foreign objects being
thrown into your eyes, which can
result in severe eye damage.
Before beginning power tool
operation, always wear safety
goggles or safety glasses with side shields and a full
face shield when needed. We recommend Wide Vision
Safety Mask for use over eyeglasses or standard safety
glasses with side shields.
It is recommended that the tool and all accessories
be safety stored after use.