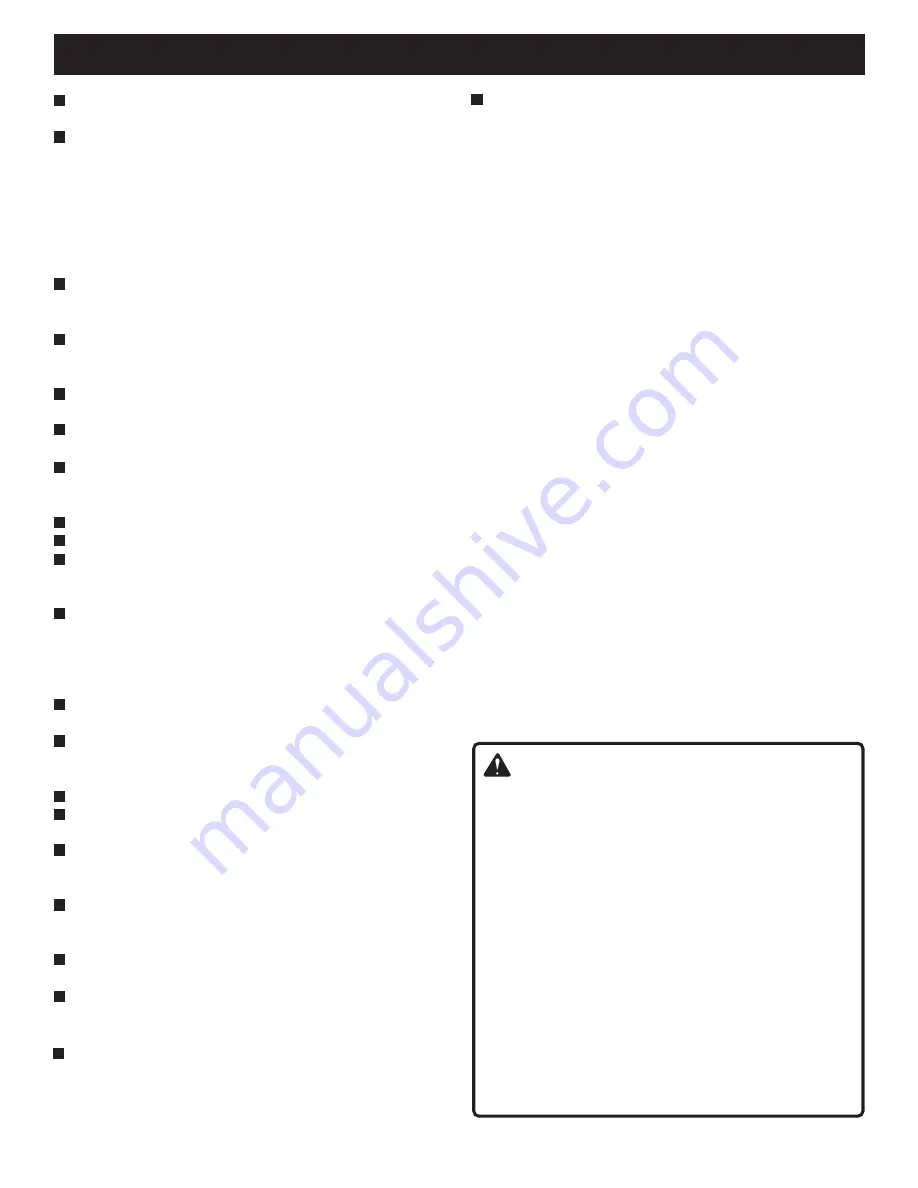
RULES FOR SAFE OPERATION
Page 5
PROVIDE
adequate support to the rear and sides of the
saw table for wide or long work pieces.
AVOID KICKBACKS
(work thrown back toward you)by:
(1) Keeping blade sharp.
(2) Keeping rip fence parallel to the saw blade.
(3) Keeping splitter and guard in place and operating.
(4) Not releasing the work before it is pushed all the way
past the saw blade.
(5) Not ripping work that is twisted or warped or does not
have a straight edge to guide along the fence.
AVOID
awkward operations and hand positions where a
sudden slip could cause your hand to move into the cutting
tool.
NEVER
use solvents to clean plastic parts. Solvents could
possibly dissolve or otherwise damage the material.Only
a soft damp cloth should be used to clean plastic parts.
PERMANENTLY
mount the saw to a supporting surface
before performing any cutting operations.
NEVER
cut metals or materials which may make hazardous
dust.
ALWAYS
use in a well ventilated area. Remove saw dust
frequently. Clean out sawdust from the interior of the saw
to prevent a potential fire hazard.
Do not use saw blades which are damaged or deformed.
Replace table insert when worn.
Use only saw blades recommended by the manufacturer,
Warning: The splitter shall not
be
thicker than the kerf of
blade and not thinner than the body of saw blade.
Take care that the selection of the saw blade depends on
the material to be cut. Use only saw blades for which the
maximum possible speed is not less than the maximum
speed of the tool and the material to be cut. Do not use
high speed steel (HSS) blade
s
.
Use this
table
saw to cut only wood and wood like
products.
Use push-sticks to feed the workpiece past the blade.
Always store the push stick with the machine when not
in use.
Connect saw to a dust-collecting device when sawing.
Store idle tools. When not in use, tools should be stored
in a dry locked-up place, out of reach of children.
Connect dust extraction equipment. If device are provided
for the connection of dust extraction and collecting
equipment ensure these are connected and properly used.
Do not abuse the cord. Never yank the cord to disconnect
it from the socket. Keep the cord away from heat, oil and
sharp edges.
Stay alert. Watch what you are doing, use common sense
and do not operate the tool when you are tired.
Inspect tool cords periodically and if damaged have them
repaired at an authori
s
ed service facility. Inspect extension
cord periodically and replace if damaged.
Have your tool repaired by a qualified person. This electric
tool complies with the relevant rules. Repairs
should only
be carried out by qualified persons using original
spare
parts, otherwise this may result in considerable danger
to
the user.
Use outdoor extension leads. When the tool is used outdoors,
use only extension cords intended for outdoor use and so
marked.
■
CHECK WITH A QUALIFIED ELECTRICIAN
or service
personnel if the grounding instructions are not completely
understood or if in doubt as to whether the tool is properly
grounded.
■
USE ONLY CORRECT ELECTRICAL DEVICES
: 3-wire
extension cords that have 3-prong grounding plugs and 3-
pole receptacles that accept the tool's plug.
■
DO NOT MODIFY
the plug provided. If it will not fit the
outlet, have the proper outlet installed by a qualified
electrician.
■
USE ONLY RECOMMENDED ACCESSORIES
listed in
this manual or addendums. Blades must be rated for at
least 5,500 rpm. Use of accessories that are not listed may
cause the risk of personal injury. Instructions for safe use
of accessories are included with the accessory.
■
DOUBLE CHECK ALL SETUPS.
Make sure blade is tight
and not making contact with saw or workpiece before
connecting to power supply.
■
SECURE THE SAW TO THE LEG STAND OR A WORK-
BENCH
capable of supporting the load of the saw plus any
workpiece. This is necessary to avoid any risk of the saw
tipping over.
■
MAKE SURE THE WORK AREA HAS AMPLE LIGHT-
ING
to see the work and that no obstructions will interfere
with safe operation
BEFORE
performing any work using
the table saw.
■
ALWAYS TURN OFF SAW
before disconnecting it, to
avoid accidental starting when reconnecting to power
supply.
■
SAVE THESE INSTRUCTIONS.
Refer to them frequently
and use to instruct other users. If you loan someone this
tool, loan them these instructions also.
WARNING:
Some dust created by power sanding, sawing, grinding,
drilling, and other construction activities contains
chemicals known to cause cancer, birth defects or
other reproductive harm. Some examples of these
chemicals are:
• lead from lead-based paints,
• crystalline silica from bricks and cement and other
masonry products, and
• arsenic and chromium from chemically-treated
timber
.
Your risk from these exposures varies, depending on
how often you do this type of work. To reduce your
exposure to these chemicals: work in a well ventilated
area, and work with approved safety equipment, such
as those dust masks that are specially designed to filter
out microscopic particles.