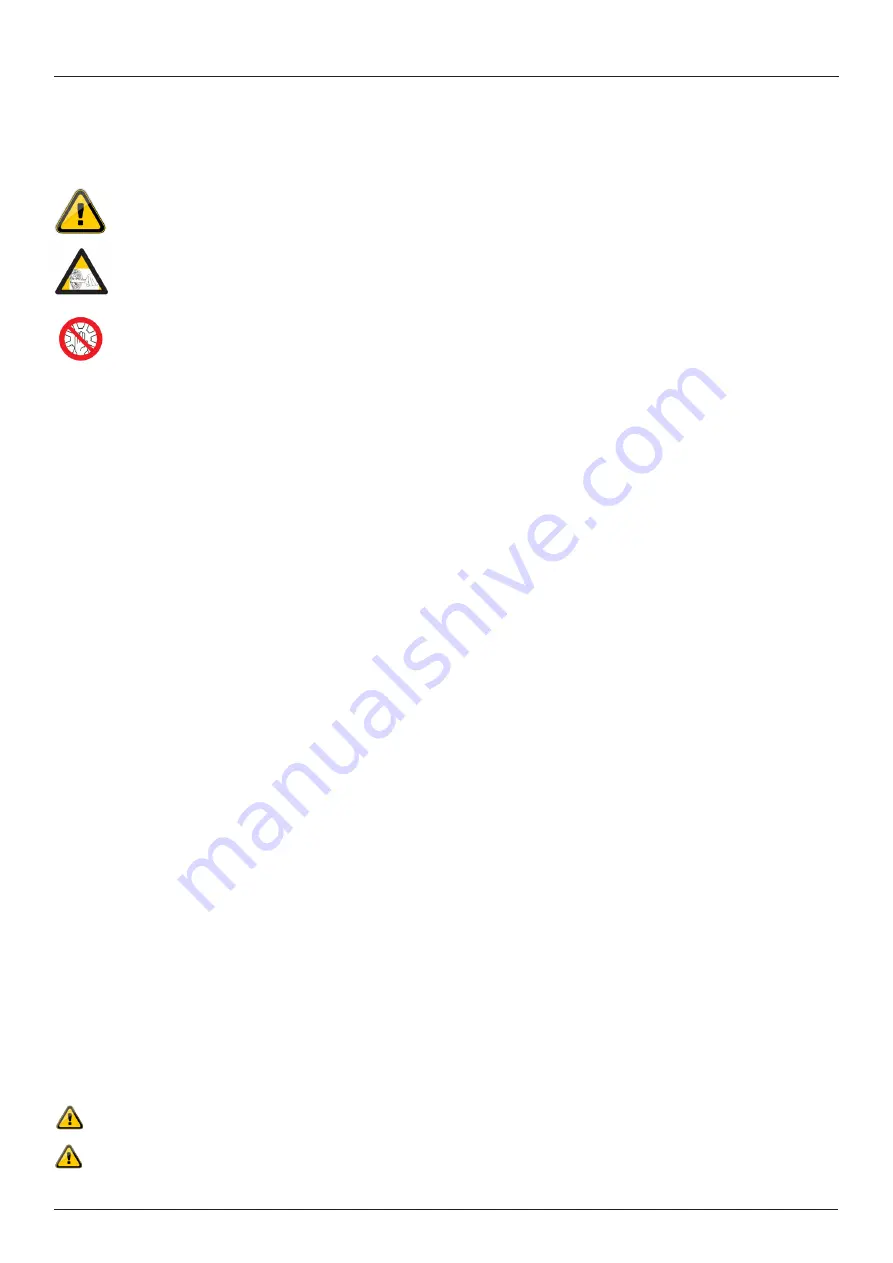
5
MINI CRIMPER SERIES OPERATION MANUAL
Danger Zones
General Warning Label
Pay particular attention to these items.
Crimping Hose Assembly Label
When crimping a hose assembly, hold the hose far enough away to avoid any pinch or crush zones.
No Hands Label
Do not put your hands in these areas while the motor is running.
SAFETY RULES
RY16
The machine consists of a chassis, crimping head and is delivered ready to use, packed in a wooden box on a pallet.
To ensure a safe and practical work environment the machines should be located in an area that provides
• Adequate working space around the machine
• Sufficient lighting of the work area.
Equipment
GENERAL
The RYCO RY16 Crimper is designed for a max input pressure of 700 bar/10,000 psi. Do not exceed this input
pressure.
Appropriate Personal Protective Equipment (PPE) must be worn during hose making and maintenance activities.
•
This pump should only be used by qualified, trained persons who are familiar with this equipment.
•
To avoid personal injury, keep hands and feet away from crimper and workpiece during operation.
•
Do not exceed equipment ratings. Overloading causes equipment failure and possible personal injury. The crimper is
designed for a max. pressure of 700 bar (10,000 psi).
•
Never Set the relief valve pressure above 725 bar (10,500 psi). Serious personal Injury could result if this maximum
limit is exceeded. Damage to crimper pump and components may also occur.
•
Keep hydraulic equipment away from flames and heat. Excessive heat will soften packings and seals, resulting in
fluid leaks. Heat also weakens hose materials and packaging. For optimum performance do not expose equipment to
a Temperature of 50°C (122°F) or higher. Protect hoses and cylinders from weld spatter.
Safety Notes
Hose Assembly
Should a hydraulic hose rupture, burst or need to be disconnected, immediately shut off the pump and shift the control
valve to release all pressure.
•
Never grasp a leaking pressurized hose with your hands.
•
Always keep the hose away from fire, sharp surfaces, heavy impact and extreme heat or cold. Never kink, twist, curl
or bend the hose so tightly that the oil flow within will be blocked or reduced.
•
Always inspect the hose for wear periodically, as any of these conditions can damage the hose and possibly result in
personal injury.
•
Hose material and coupling seal must be compatible with the hydraulic fluid used.
•
Hose must not come in contact with corrosive materials.
•
Never paint a coupling, hose will deteriorate due to toxic materials.
•
Never use the hose to move attached crimper*. Stress can damage the hose and may cause personal injury.
Summary of Contents for MINI CRIMPER Series
Page 2: ......