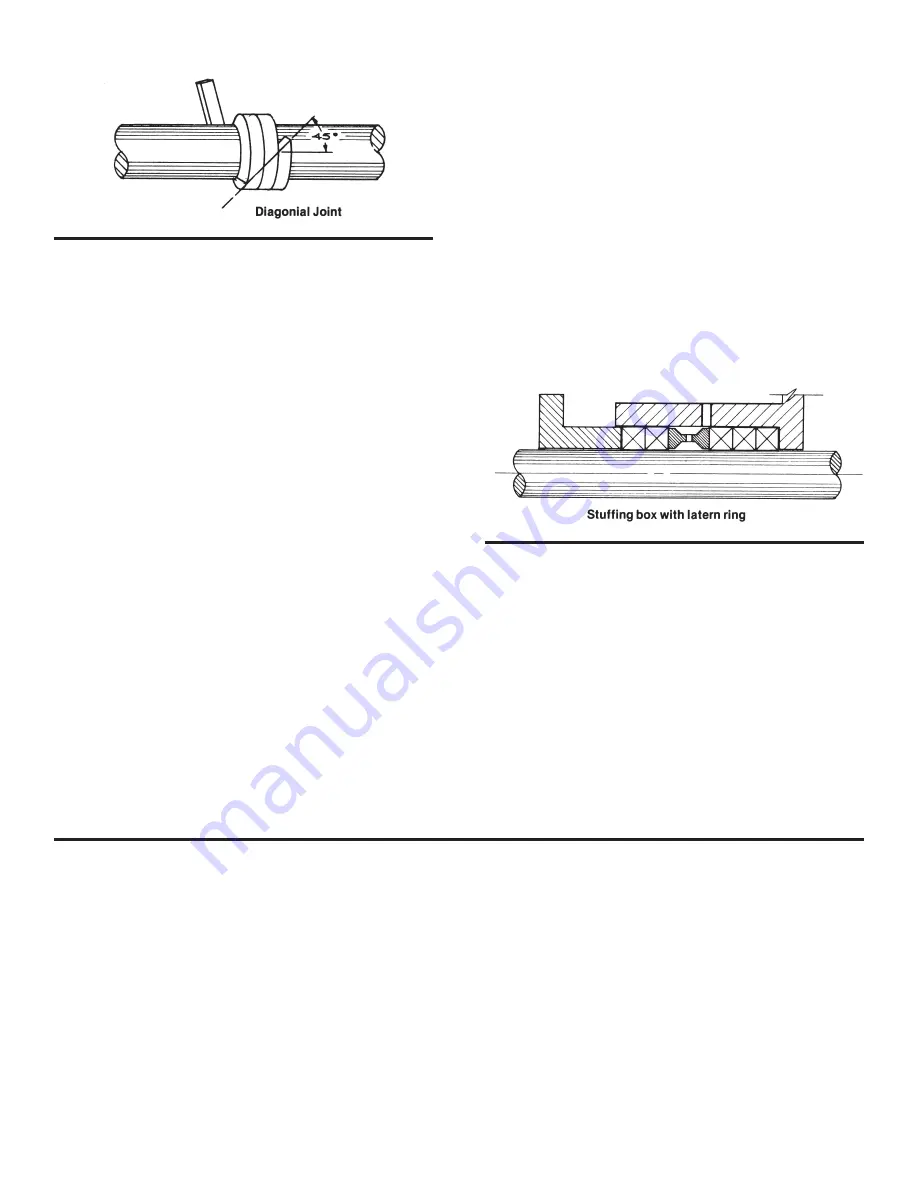
8
It is necessary that the rings be cut to the correct size,
otherwise service life is reduced.
4. Install one ring at a time. Make sure it is clean and
has not picked up any dirt in handling. If clean oil is
available, lubricate the shaft and the inside of the
stuffing box.
Seat rings firmly. (Except for TFE filament and graph-
ite yarn packings which should be snugged up very
gently. Then wrench in gradually...after the pump is
back in operation.) Joints of successive rings should
be staggered and kept at 90
O
apart. Each individu-
al ring should be firmly seated with a tamping tool.
When enough rings have been individually seated so
the nose of the gland (#9) will reach them, individual
tamping should be supplemented by the gland. Nev-
er depend entirely on the gland to seat a set of rings
properly - this practice will jam the last rings installed
but leave the bottom rings loose in the box.
5. After the last ring is installed take up bolts finger
tight or very slightly snugged up. Do not jam the
packing into place by excessive gland loading. Start
pump, and take up bolts until leakage is decreased to
minimum. Make sure gland bolts are taken up evenly,
stopping leakage entirely at this point will cause the
packing to burn up.
6.
Allow packing to leak freely when starting up a newly
packed pump. Excessive leakage during the first hour
of operation will result in a better packing job over a
longer period of time. Final adjustment should allow
approximately 30 drops per minute to leak from the
packing.
7. When specified, Gusher can provide means of lu-
bricating the shaft and packing through a lantern ring
by supplying water, oil, grease, or liquid handled in the
pump.
8. If the stuffing box has a lantern ring, make sure the
lantern ring, as installed, is slightly behind the fluid inlet
so it will move under the inlet as gland pressure is ap-
plied. (See illustration below.)
9. Replace packing when leakage cannot be con-
trolled by further takeup on the gland.
Some of the most common reasons for packing failure
are:
1. Improper installation
2. Uneven gland adjustment
3. Shaft misalignment and shaft whip
4. Improper selection of packing for liquid
5. Improper selection for pressure and temperature
6. Contaminated liquid (dirt, abrasives, etc.)
MECHANICAL SEAL
The most important factor in mechanical seal, other than
the sealing qualities, is the fact that once it has been prop-
erly installed there is little or no maintenance required.
Some of the most common reasons for seal failure are:
1. Improper installation
2. Shaft misalignment and shaft whip
3. Wrong selection for liquid pumped
4. Wrong selection for pressure and temperature
5. Dirt or grit between faces
6. Seal gland (#9) tightened unevenly so stationary seat
is not perpendicular to shaft.
7. Operation without fluid