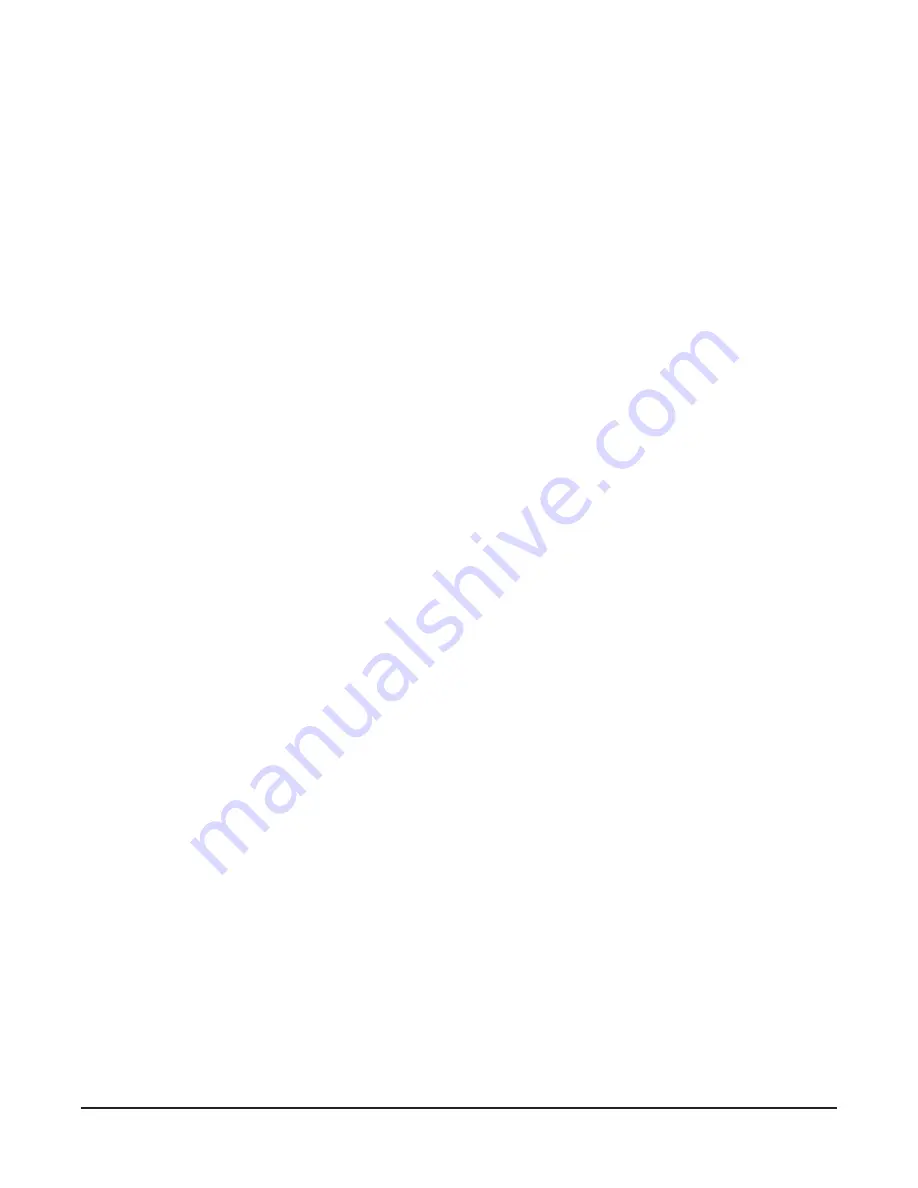
5
Airflow-IQ Start-up & Commissioning Guide
Unpacking and Installing the AIRFLOW-IQ Electronic Air Measuring Station
Remove the AIRFLOW-IQ from its shipping container and inspect for damage, rust or corrosion . Care must be taken
in handling the unit . Always handle the AIRFLOW-IQ by its frame . Do not lift it by the blade, linkage, axle, motor
or jackshaft . Do not drop, drag, step on or apply excessive bending, twisting or racking loads to the AIRFLOW-IQ .
Improper handling of the unit will have adverse affects on the calibration and could result in cancellation of the
warranty .
Inspect the ductwork and/or the opening where AIRFLOW-IQ will be installed for any obstructions or irregularities
that might interfere with the probes, blade, linkage rotation or the actuator . When installed in the ductwork, the
ductwork should be supported in the area of the AIRFLOW-IQ to prevent sagging .
The AIRFLOW-IQ must be installed with the frame square and without twisting or bending . Unless specifically
designed for a vertical blade application, the unit must be mounted with its blade axis in the horizontal plane .
The damper blades, axles and linkage must be able to operate without binding .
Ensure that the air enters the probes upstream and exits the damper downstream .
The best location for the extended shaft or jackshaft must be determined before installing the damper . After the
damper is installed the shaft location cannot be changed without removing the damper . The jackshaft, when pres-
ent, will always be in the leaving air stream . The AIRFLOW-IQ has a specific inlet and outlet and must be installed
in the correct orientation . The air enters through the air measurement probe(s) and exits the unit from the damper
frame side . Use appropriate shims between damper frame and duct opening to prevent distortion of the frame by
the fasteners holding the unit in place .
After installing the assembly in the ductwork or mounting hole, caulk around the damper frame to ensure that there
is no leakage or bypass air around the air measuring station .
The TDP05K probes are factory calibrated and tested in order to perform correctly in its job specific application .
Refer to the wiring schematic and controls section of this document for necessary field power connections .
Once electrical power is applied, the Primary display will go through a start-up sequence during which it will identify
and communicate with each airflow sensor . Once the start-up sequence has been complete, the Primary display will
show the measured airflow rate, velocity, and ambient air temperature .
Reasonable access must be provided to allow inspection and maintenance of the actuator, probes and damper .
The sensor density is based on extensive lab testing to optimize the accuracy of the AIRFLOW-IQ Electronic
Air Measuring Station . Contact your local Ruskin
®
representative if you have questions regarding a particular
application .