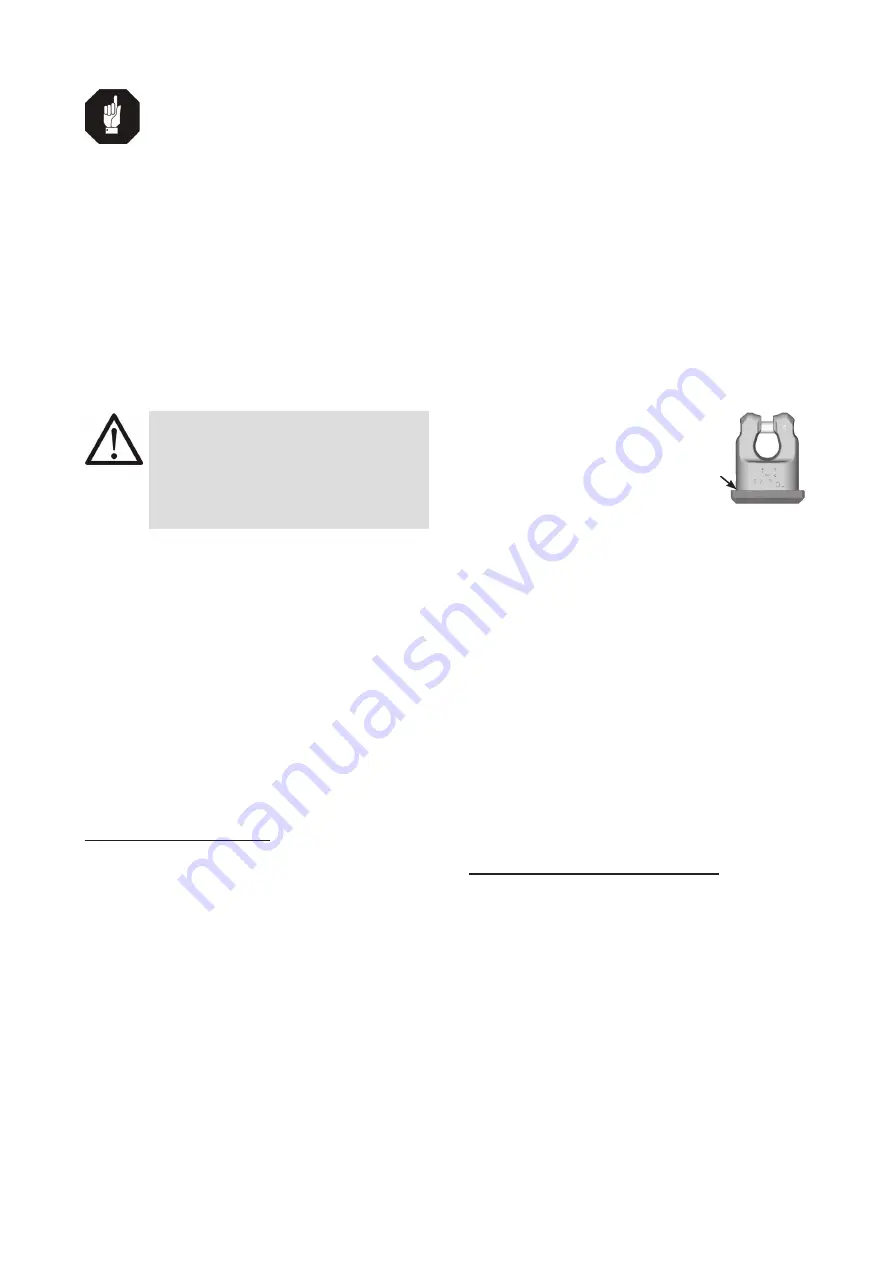
4
PowerPoint
®
HINT
Do
not
weld on the connecting elements (eye-
hook, oval link, ...)!
4. Please check by a competent person after welding the
ongoing usage of the weld-on lifting point (see chapter
5, Inspection / repair
).
5. Due to the welding the amount of lubrication inside the
bearing of the WPP / VWBS can be reduced. If neces-
sary, lubricate the WPP / VWBS bearing (see Section
6
Notes regarding repairing
).
4.4 User instructions
• Check frequently and before each initial operation the
whole weld-on lifting point PowerPoint® in regard of
linger ability as a lifting mean, evidence of cracks on the
welding seam, regarding corrosion, wear, deformation
etc. (see chapter 5, Inspection / repair).
ATTENTION
Wrong positioned or damaged weld-on lifting
points as well as improper use can lead to
injuries of persons and damage at property,
when load falls down.
Please check all lifting points carefully before
every usage.
• RUD components are designed according to DIN EN
818 and DIN EN 1677 for a dynamic load of 20,000 load
cycles.
• Keep in mind that several load cycles can occur
with a lifting procedure
• Keep in mind that, due to the high dynamic stress
with high numbers of load cycles, that there is a
danger that the product will be damaged.
• The BG/DGUV recommends: For higher dynamic
loading with a high number of load cycles (contin
-
uous operation), the working load stress must be
reduced according to the driving mechanism group
1Bm (M3 in accordance with DIN EN 818-7). Use
a lifting point with a higher working load limit.
5 Inspection / repair
5.1 Hints for periodical inspections
The operator must determine and specify the nature and
scope of the required tests as well as the periods of re
-
peating tests by means of a risk assessment (see sections
5.2 and 5.3).
The continuing suitability of the anchor point must be
checked at least 1x year by an expert.
Depending on the usage conditions, f.e. frequent usage,
increased wear or corrosion, it might be necessary to check
in shorter periods than one year. The inspection has also
to be carried out after accidents and special incidents.
The operator must specify the test cycles.
5.2 Test criteria for the regular visual
inspection by the user
• Completeness of the lifting point
• Completeness of manufacturer‘s and WLL markings
plus their readability
• Deformation at load bearing components like base body,
suspension hook and ring (p.ex. marker points at the
Cobra-hook)
• Mechanical deformations like deep notches especially
in areas where tensile stress occures.
•
mouth width opened (overload) > 10 %
• Evidence of cracks
• Evidence of cracks and other damages on the welding
seam.
• Easy, jerk free turning between top and bottom part
of the PowerPoint
®
WPP and VWBS-KA-28 must be
ensured.
•
Pic. 6: Gap
The maximum gap between upper-
and lower part of the PowerPoint
®
must not be exceeded:
WPP-..-0.63 t up to WPP-..-2.5 t
→ max. 1.5 mm
WPP-..-4 t up to WPP-..-8 t
→ max. 2.5 mm
VWBS-KA-28
→ max. 4 mm
• please check tightening of the lateral positioned locking
bolt at all swivel types
5.3 Additional test criteria for the
competent person / repair worker
• Reduction of cross-section caused by wear by more
than 10 %.
• Intense corrosion (pitting).
• further checks may be required, depending on the
result of the risk assessment (e.g. testing for cracks in
load-bearing parts).
6 Notes regarding repairing
Repairing must only be carried out at RUD headquarters
or by RUD authorized partners who have recuperate the
necessary knowledge and capabilities.
For maintenance and re-lubrication of the VWBS-KA-28,
please use grease f.e. AVALITH 2EP or comparable lubri-
cants. For this use a grease press with a nozzle for cup
head lubrication nipples.
Lubricate of the WPP (rotable) during maintenance at the
gap between housing and suspension ring with spray oil
resp. grease (see pict. 6).