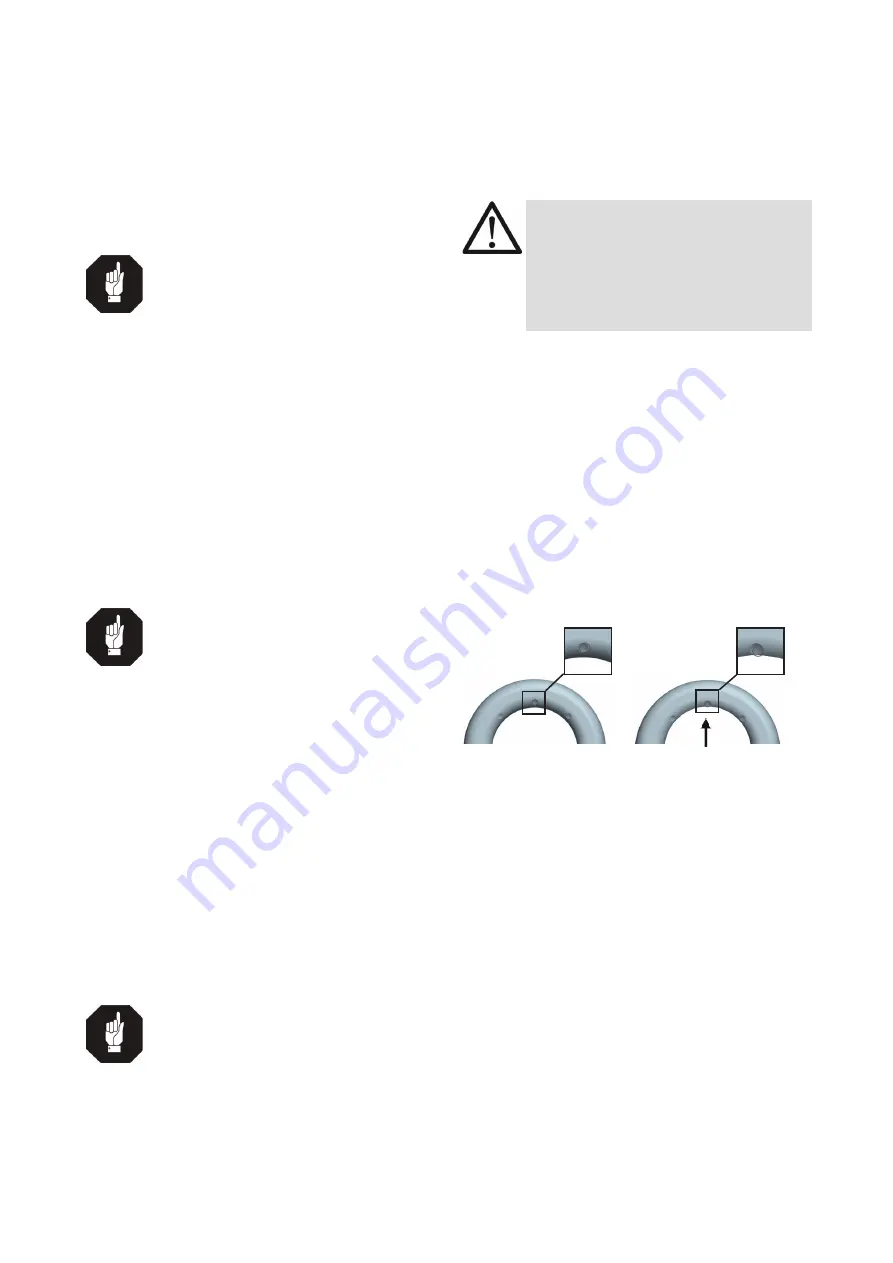
3
LRBS-FIX
• Determine number and position of the lashing
points at vehicles according to EN 12640 resp. DIN
75410 (for RoRo-transportation acc. to EN 29367),
unless the vehicles are not determined due to their
design and construction for transporting specific
goods with special requirements in regard of load
securing.
• Position lashing points as much as possible at the
outside width of the loading platform.
HINT
The lashing points must not protrude in rest
position over the loading platform level.
• Determine the necessary lashing capacity of each
lashing point acc. to EN 12195-1”Load securing
devices on road vehicles” - “Calculation of lashing
forces” and VDI 2700 ”Load securing of road ve-
hicles.”
• Check finally the correct assembly (see chapter
4
Inspection / Repair / Disposal
).
3.3 Hints for the welding
The welding should only be carried out according to
DIN EN ISO 9606-1 or AWS Standards by an autho-
rized and certified welder.
Verification of the used weld-on material must be
checked with the supplier of the welding electrodes.
HINT
•
Never weld at the quentched and
tempered ring!
•
Weld all seams at the same
temperature.
1. Check before initial appending of the LRBS-Fix,
the position of the weld-on blocks to each other,
that means the base area must be at the same
level.
2. Append weld-on blocks.
3. Check function of the ring. The ring must be able
to pivot 180°. If necessary please correct.
4. Remove any welding mistakes and dirt at the root
weld before applying the cover weld seams.
5. Weld blocks on (HY-weld circumferential).
Choose type of weld seam and size according to
picture 2 and chart 2.
6. Please check by a competent person after welding
the ongoing usage of the weld-on lashing point
(see chapter
4 Inspection / Repair / Disposal
)
HINT
By the position of the weld-seam (HY-weld
circumferential) the following requirements
will be observed: DIN 18800 steel con-
structions requires: at outdoor buildings or
when strong corrosion must be expected
weld seams must be carried out as conti-
nuous fillet weld seams.
3.4 User instructions
• Check frequently and before each initial operation
the whole lashing point in regard of linger ability
as a lashing mean, regarding corrosion, wear,
deformation etc. (see chapter
4 Inspection / Repair
/ Disposal
).
ATTENTION
Wrong positioned or damaged weld-on
lashing points as well as improper use can
lead to injuries of persons and damage at
property, when load falls down.
Please check all lashing points carefully
before every usage.
• RUD components have been designed as per DIN
EN 818 and DIN EN 1677 for a dynamic load of
20,000 load cycles.
• Observe and be aware that multiple load cycles
can occur during a lashing operation.
• Observe the risk of product damage caused by
high dynamical influences at high load cycle
numbers.
• BG/DGUV Germany’s employer insurance asso-
ciation recommends: At high dynamical loading
with a high number of load cycles (permanent
use), the stress at WLL acc. to FEM class 1Bm
(M3 acc. to DIN EN 818-7) must be reduced.
Use a lashing point with a higher LC.
• Please check carefully the wear indicator markings
of the weld-on lashing point (see
Pic. 1
):
Usage permitted:
no wear marks
visible
Use prohibited:
Replacement criteria rea-
ched. Material all the
way down to the
wear lenses has gone.
Pic. 1: Wear indicators
• Please note that the lashing mean must be free
moveable in the LRBS-FIX. When lashing means
(f.e. lashing chain) are hinged or unhinged, no
pinching, shearing or joint spots must occure du-
ring the handling.
• Avoid damage of lashing means resulting from
sharp edges.
• Lashing points must not be used for lifting loads.