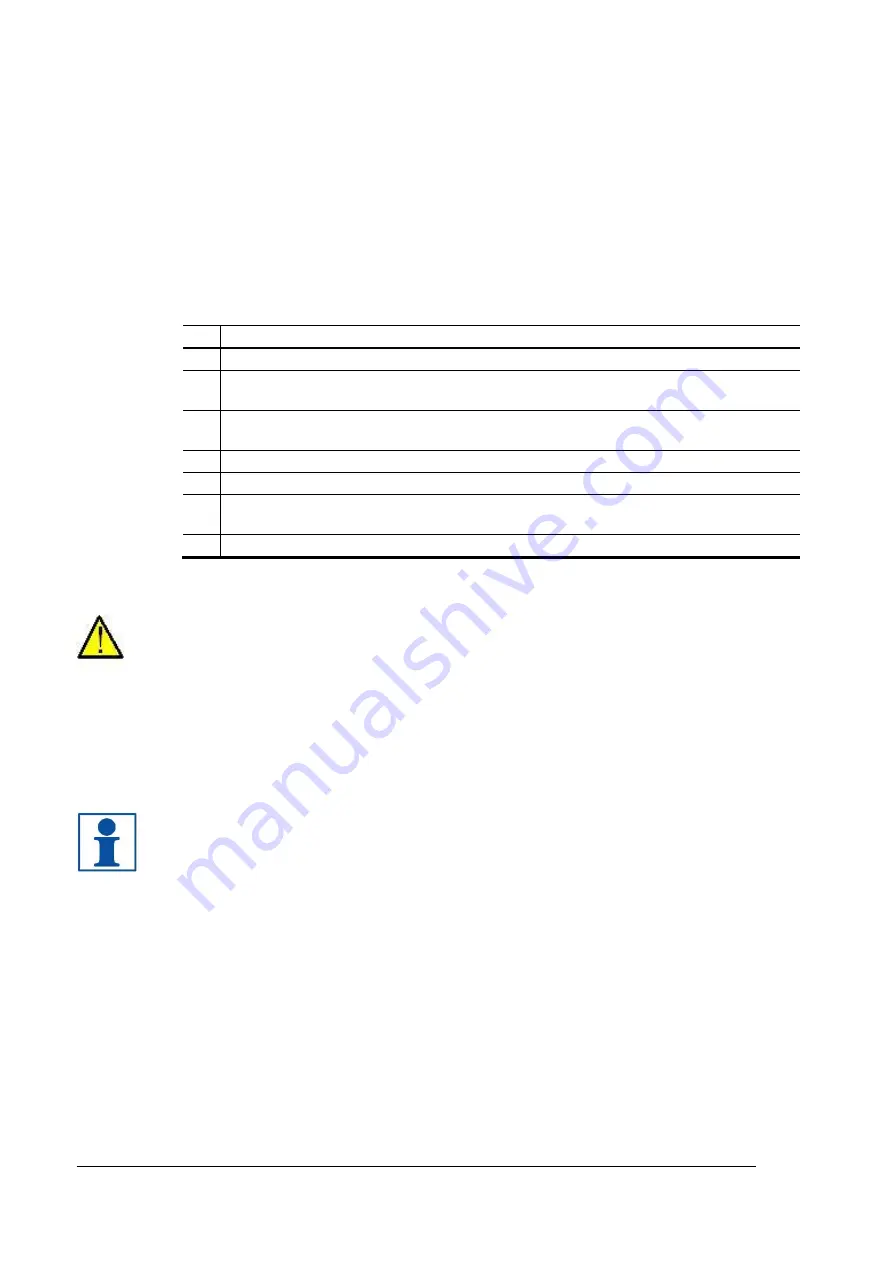
26
M0604-1 ver. 2.3
3.6 Limitation of Robot movements
There can be some limitations on the movement of axis 5 for some robot models. Contact Robot
System Products for more information.
3.7 Hints
Programming
The following will ensure a correct docking position.
Action
1
Attach a spare tool attachment (without the external air module) to the tool changer.
2
Position the spare tool attachment above the tool attachment that is mounted on the
tool.
3
The right position is found when the tool attachments are parallel, centered and the
engraved arrows are on the same line.
4
Save the position. The robot can move to this position with high speed.
5
Dismount the spare tool attachment.
6
Go back to the saved position and move the tool changer (in axis 6 direction) the
remaining distance to the tool attachment (mounted on the tool).
7
Save the position. The robot should move to this position with low speed.
Sparking
WARNING!
Electrical signals and power must be switched off and disconnected
when docking the tool attachment. This is to prevent sparking between signal pins
and tool attachment.
Electrical installation
Connection kits for the tool changer and tool attachment are available (see
section 2.2.5).
Tool stand
NOTE!
To guarantee reliability and a long service-life for the tool changer, the tool
stand must be stable, both in terms of its design and attachment.
Tool Identification
Jumpers on signals at the tool attachment can be used to give information about
which tool attachment that is docked in the tool changer.
Summary of Contents for P0602
Page 2: ...2 M0604 1 ver 2 3 ...
Page 18: ...18 M0604 1 ver 2 3 2 1 8 Pneumatic diagram Pne0166 001A ...
Page 19: ...M0604 1 ver 2 3 19 2 1 9 Circuit diagram E0166 001B for P0603 and P0608 ...
Page 20: ...20 M0604 1 ver 2 3 2 1 10 Circuit diagram E0166 005D for P0604 ...
Page 36: ...36 M0604 1 ver 2 3 5 SPARE PARTS 5 1 Part list for tool changer P0601 and P0603 ...
Page 41: ...M0604 1 ver 2 3 41 ...
Page 42: ...42 M0604 1 ver 2 3 ...