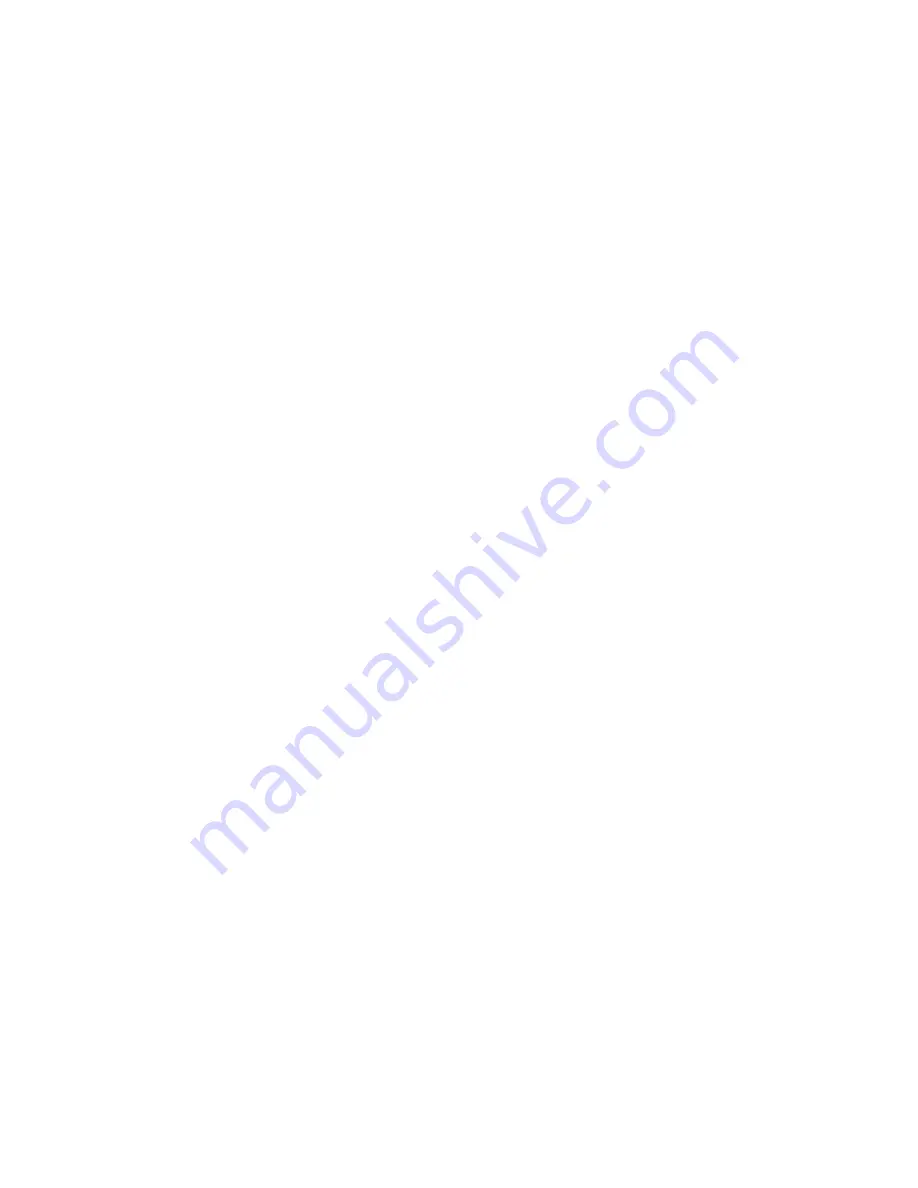
4.
Depress the gas control slightly and turn clockwise until the indicator mark is opposite to the large flame
symbol. The burner will now run at its maximum rate.
5.
To turn the appliance ‘off’, return the control to the ‘off’ position.
6.
If for any reason the fire cuts out, return the control knob to the ‘off’ position and wait 3 minutes before re-
lighting.
5(029$/2)'(%5,6256227'(326,76
Allow the appliance to cool sufficiently before removing all of the coals and firebed components for cleaning
purposes. Once all the ceramics are removed from the firebed check that no debris is located in the burner slots
(both front and rear). If any debris is present it may easily be removed by using a small piece of thin cardboard to
ease out any foreign matter. Be sure to remove the cardboard after use. Should any soot accumulation become
excessive, the fuel effect pieces should be removed from the fire for cleaning. Cleaning should be carried out in a
well-ventilated area or in the open air, by gently brushing with the pieces held away from your face so that you
avoid inhaling the dust. We do not recommend the use of a normal domestic vacuum cleaner, which may blow
dust back into the air. Any sooty deposit on the thermocouple probe can be cleaned off using a non-fluffy cloth.
$66(0%/<2)7+()8(/%('&20321(176
1.
Locate the fibre back/side cheeks in position.
2.
Place the coal support shelf on the stainless steel channel, (the machined groove on the underside of the shelf is
located on the rear flange of the channel), two additional location dowels are fitted to prevent the shelf being
incorrectly placed.
3.
Place the two shaped burner inserts in channel between the two burner flame ports, (check that a minimum gap of
approx. 6mm is maintained between the rear of the burner insert and the front edge of the coal support shelf).
4.
Position the front simulated coal on the shelf provided above the control facia panel.
&2$//$<287
Position 3 large coals, 2 triangular and 4 large coals on edge (straddle the gaps of the coal support shelf and run
the strata front to rear) as the first layer (fig. 21). Place 4 medium as a second layer sitting on the gaps of the front
coals and resting against the rear coals.(fig 22). Finally place the remaining 5 small coals as shown in fig 23. Small
adjustments to the coal layout may be made to give the best visual appearance however, additional coals must
not be used. If any fibre component is lost or broken the appliance must not be used until a replacement is
obtained.
9(17,/$7,21
Additional purpose built ventilation is not required for this appliance in GB only, for Ireland (IE) ventilation is
required with a minimal cross sectional area of 100 sq. CMS and should be checked regularly to ensure that it is free
from obstruction.
&/($5$1&(726,'(WLPEHUVXUURXQGVHWF
Minimum clearance required to any combustible material to the side of the appliance must be 150mm.
&/($5$1&(726+(/9(6
Minimum clearance to the underside of a 150mm deep combustible shelf from the hearth must be 833mm. Add
12.5mm to this clearance for every 25mm increase in depth of shelf.
Page 3