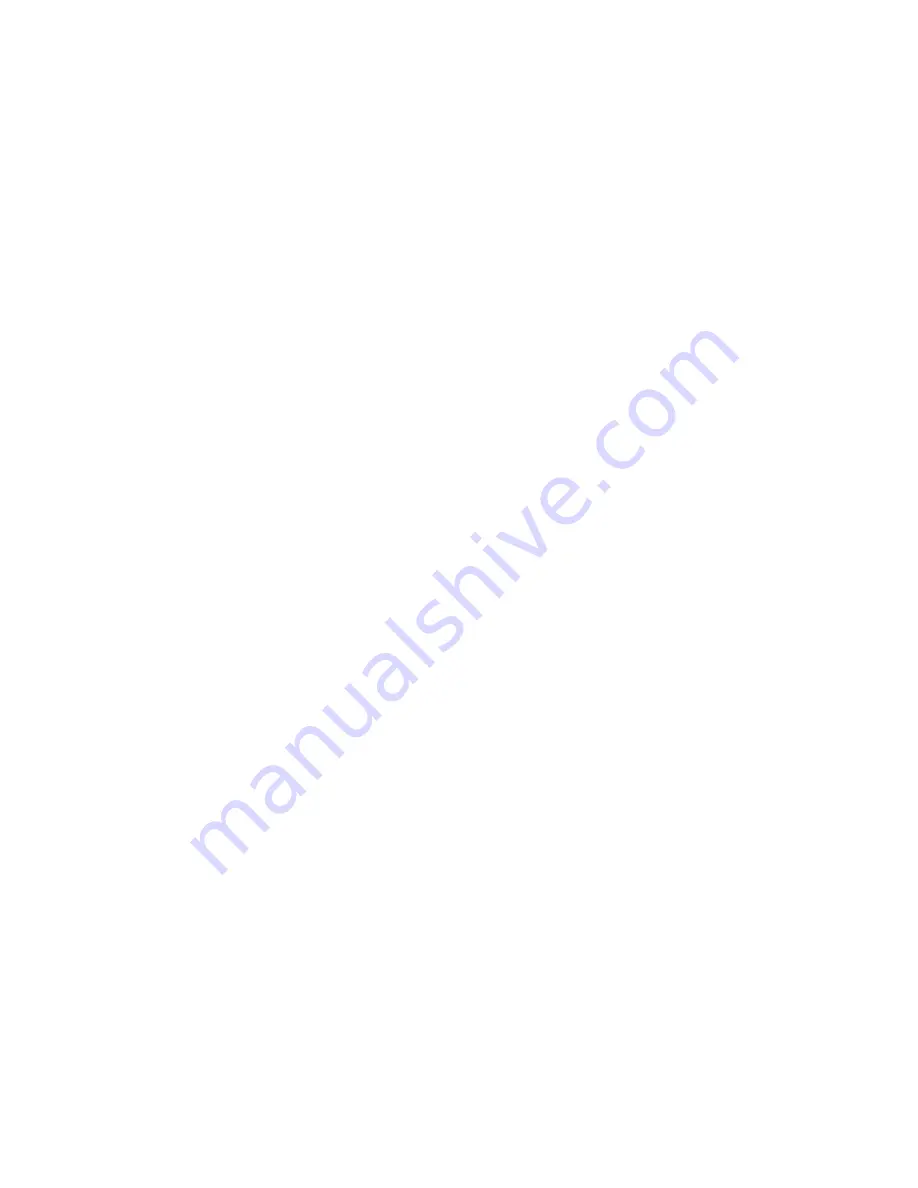
amount of water in the pipes and cylinders which will cause the
engine to run jerkily until it is exhausted through the chimney. This
is known as priming and is quite normal and will clear after a few
moments. If the engine appears to ‘lock up’ during initial starting
from cold, it is often helpful to close the regulator and gently move
the engine manually to expel the excess water from the cylinders
then open the regulator just a little to allow a small amount of
steam through. It is also helpful to reverse direction of the
locomotive with the regulator closed, then open the regulator just a
little and run in reverse for a short distance. This may have to be
repeated until all water clears but avoid forcing or jerking the
engine as this will only aggravate the matter. Gently does it and
small regulator openings will ensure the quickest results.
Once the parts have warmed up, the engine will move off steadily
and its speed can be controlled with the regulator. Subsequent
starts will be quite smooth once the cylinders etc. have reached
their normal operating temperature and the water level in the boiler
has dropped a little. This tendency to prime will often reduce as the
loco becomes ‘run in’.
To reverse the locomotive, close the regulator to bring it to a halt,
move the engine manually for one wheel revolution in the desired
direction and open the regulator again. Take care when holding the
engine to reverse it as it will be very hot in places.
The art of
fine control will soon be learnt with a little practice.
Once the gas has all been used, the burner will go out and steam
pressure will drop until it is so low that the loco will no longer run.
When this happens, close both the steam and gas regulators and
allow the loco to cool down before preparing for another run. Once
it is cool enough to remove the safety valve, refill water, gas and
lubricator as previously described ready for the next run.
The boiler should not be allowed to run dry, but as the gas is
designed to run out before the water, this should not happen under
normal running conditions and if the engine is sufficiently ‘run in‘.
11