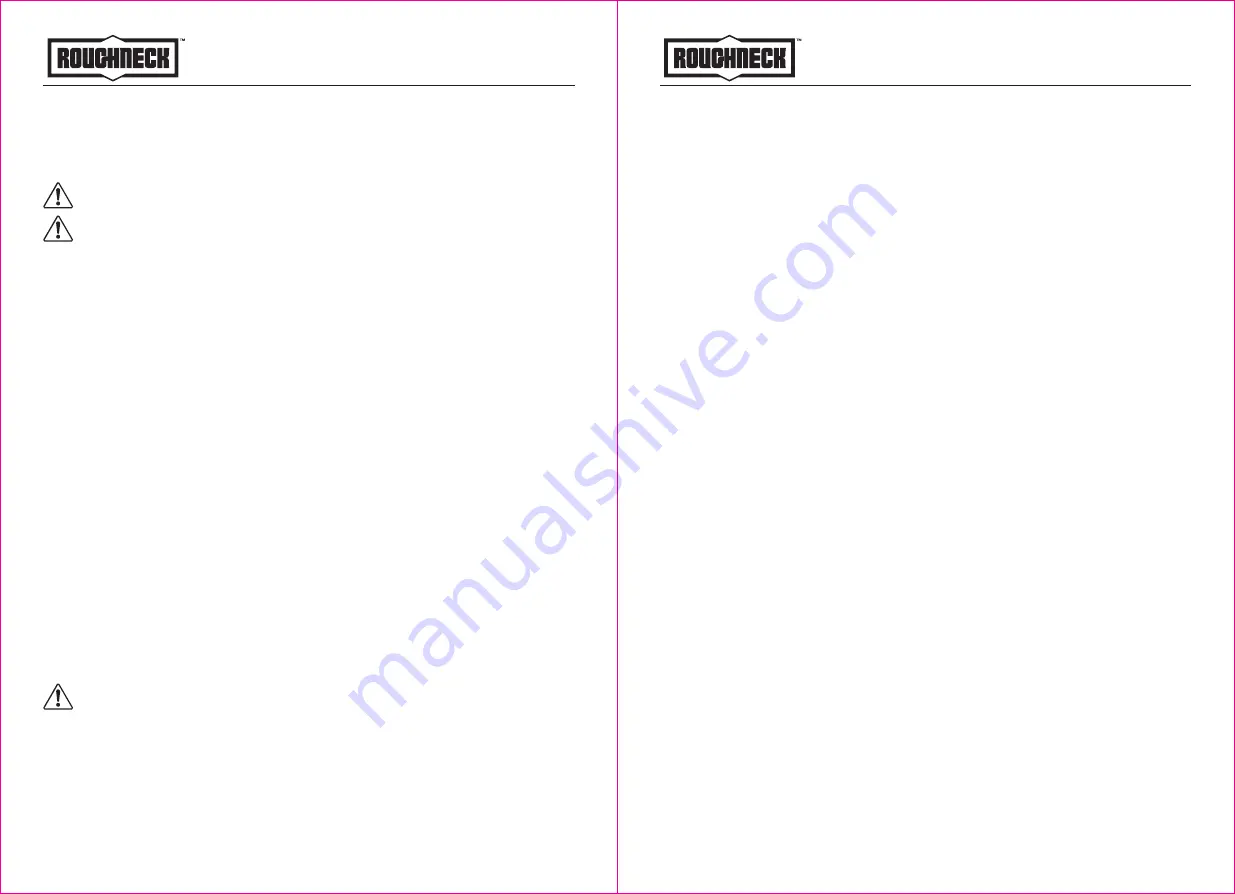
12V FUEL TRANSFER PUMP OWNER’S MANUAL
12V FUEL TRANSFER PUMP OWNER’S MANUAL
OPERATING CONDITIONS
Temperature: Minimum -4°F (-20°C) / Maximum 140°F (60°C)
Relative Humidity: Maximum 90%
GENERAL SAFETY REGULATIONS
WARNING:
Read and understand all instructions.
WARNING:
The warnings, cautions, and instructions discussed in this instruction
manual cannot cover all possible conditions or situations that could occur.
It must be
understood by the operator that common sense and caution are factors that cannot be built
into this product, but must be supplied by the operator.
1.
Keep the work area clean and dry.
Damp or wet work areas can result in injury.
2.
Keep children away from work area.
Do not allow children to handle this product.
3.
Store idle equipment.
When not in use, tools and equipment should be stored in a dry location
to inhibit rust. Always lock up tools and equipment, and keep out of reach of children.
4.
Use the right tool for the job.
Do not attempt to force small equipment to do the work of
larger industrial equipment. There are certain applications for which this equipment was
designed. It will do the job better and more safely at the capacity for which it was intended.
Do not modify this equipment, and do not use this equipment for a purpose for which it was
not intended.
5.
Check for damaged parts.
Before using this product, carefully check that it will operate
properly and perform its intended function. Check for damaged parts and any other condi-
tions that may affect the operation of this product. Replace damaged or worn parts immedi-
ately.
6.
Do not overreach.
Keep proper footing and balance at all times to prevent tripping, falling,
back injury, etc.
7.
DO NOT use the equipment when tired or under the influence of drugs, alcohol, or
medication.
A moment of inattention while operating this equipment may result in serious
personal injury.
8.
Industrial applications must follow OSHA requirements.
SPECIFIC OPERATION WARNINGS
To ensure safe and efficient operation, it is essential to read and follow each of these warnings
and precautions.
1. DO NOT smoke near pump or use pump near an open flame. Fire could result.
2. Disconnect power to pump before servicing pump.
3. Turn off the switch before connecting power.
4. Take motors needing service to an authorized repair shop or return to factory to maintain.
5. A filter should be used on pump outlet to ensure that no foreign material is transferred to fuel
tank.
6. Tank or barrel should be anchored to prevent tipping in both full and empty conditions.
WARNING:
1. Electrical wiring should be done by a licensed electrician in compliance with local codes.
Rigid conduit should be used and proper ground must be provided to avoid the possibility of
electrical shock. Failure to comply with this warning could result in serious injury and/or loss
of property.
2. This product should not be used for fluid transfer into aircraft. This product is not suited for
use with fluids for human consumption, or fluids containing water.
3. Extreme operating conditions with working cycles longer than 30 minutes can cause the
motor temperature to rise, thus damaging the motor itself. Each 30-minute working cycle
should always be followed by a 30-minute power-off cooling phase.
2 of 6
INSTALLATION
1.
Tightly screw suction pipe into inlet coupling of pumping unit.
Extend suction pipe into
truck tank or barrel to within 3in. of tank bottom.
2.
Screw inlet coupling of pump into 2in. tank or barrel opening.
Inlet coupling must be
completely and securely threaded into an undamaged tank or barrel bung.
3.
During installation and maintenance, make sure that the electric supply lines are not live.
4.
Always turn off the switch before supplying electrical power.
5.
Check the correct rotation direction of the DC pump.
If it is inverted, check the polarity of
the connection cable.
a) RED cable: positive pole (+)
b) BLACK cable: negative pole (-)
6.
Systems should be designed to require a minimum amount of suction lift.
Maximum
“equivalent feet of lift” is 8 feet for diesel fuel.
7.
Tank or barrel must be properly vented.
A water separator should be used for pumping
diesel fuel.
8.
Power to the unit should be supplied from a dedicated 30 Amp circuit breaker.
No other
equipment should be powered from this breaker. If two pumps are supplied from one
breaker, that breaker must be capable of handing the load of both motors.
9.
Install bung adapter and suction pipe:
• Tighten the bung adapter snugly into the fuel tank
• Place the union ring gasket into the inlet fitting on the bottom of the pump
• Thread the suction pipe into the inlet fitting and tighten until snug. Install pump on tank
• Clean the tank interior of all dirt and foreign material
• Extend the suction pipe to its full length and insert into the tank opening
• Place the pump on the bung adapter and tighten the union ring securely with a pipe
wrench. Make sure the union ring is not cross-threaded
• To prevent pressure buildup and possible fuel leaks through the muzzle, make sure the tank
is vented a vent cap rated at 3 PSI or less is recommended
10.
Replace gears and drive key:
• Turn the pump OFF and disconnect from power
• Remove the gear cover plate
• Lift the diver key and gears from the pump
• Inspect the gears and key for wear and damage. Replace as necessary
• Wipe the gear cavity with a clean cloth
• Replace the gears. Make sure they turn freely
• Replace the drive key
• Make sure the gear cover plate O-ring is securely in place. Tighten the cover plate to the
housing
11.
To remove or replace the bypass poppet:
• As above, push down on the poppet until the O-ring is exposed
• Remove the O-ring with a small screwdriver or similar tool. Take care not to damage the
poppet or O-ring.
• From inside the housing, use a small screwdriver to push the poppet and spring through
the top outlet port
• Wipe the poppet and gear cavities with a clean cloth
• Replace the poppet, O-ring ,and spring as necessary
Note: Replace O-ring if damaged, swollen, or loose fitting
12.
To clean or replace strainer:
• Turn the pump off and disconnect from power. Remove the strainer cover plate
• Remove the inlet strainer and inspect for damage or clogs
• Clean the strainer with a soft-bristled brush and solvent. If the strainer is very dirty,
compressed air may be used. If damaged, replace the strainer
13.
Place the strainer in the cavity.
Clean the cover plate and O-ring, coat the O-ring lightly
with grease. Ensure the cover plate O-ring is properly seated and tighten the strainer cover
plate.
3 of 6