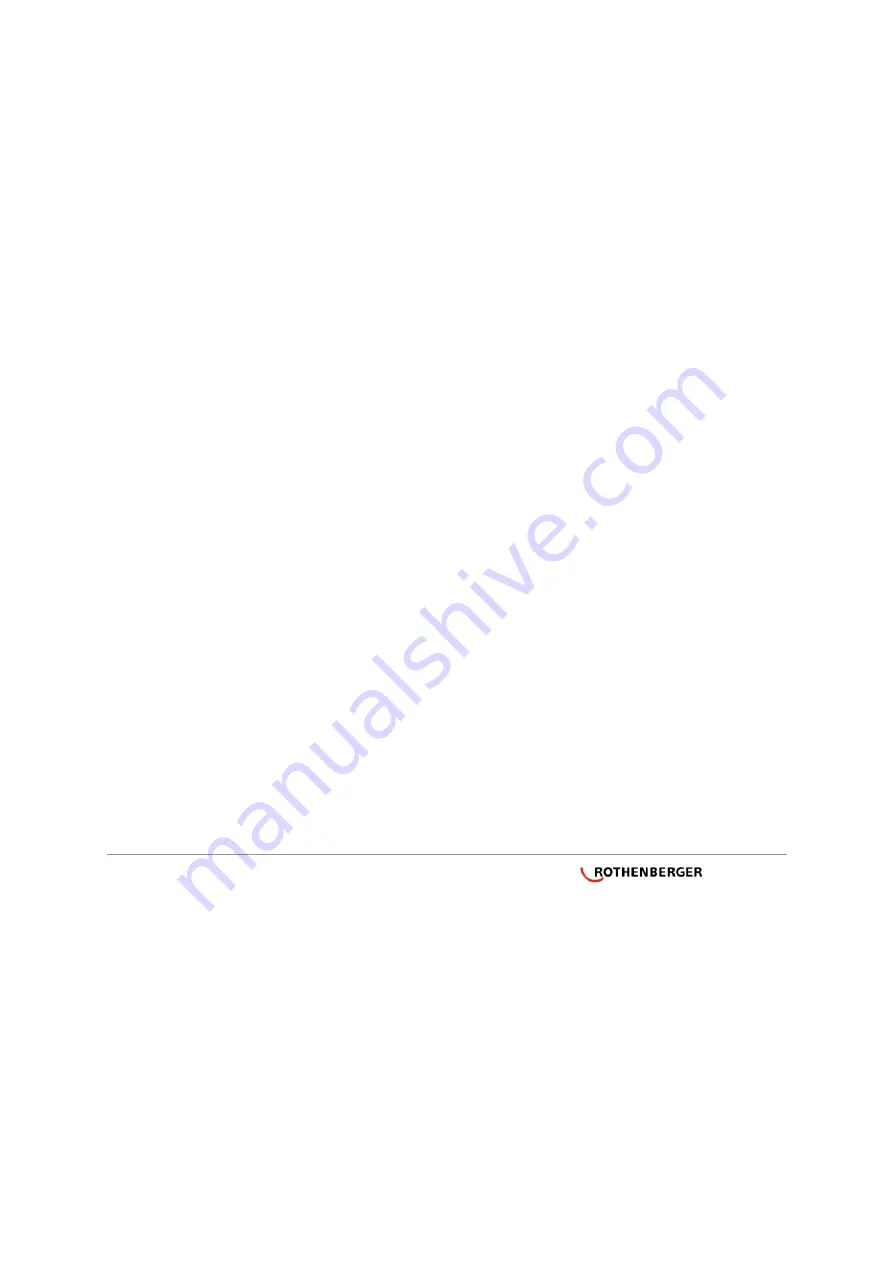
ENGLISH
23
4.5
Welding Process
The welding process is monitored for its entire duration applying the
welding parameters computed for the fitting.
4.6
End of Welding
The welding process was completed successfully if the actual welding time
shown on the screen is 0, the green LED (End) is on, and at the same time
the audible signal can be heard twice.
4.7
Welding Aborted
The welding process has caused errors if the red LED (Fault) is on and the
audible signal buzzes intermittently. Additionally, an error code is dis-
played on the screen.
An error has to be reacted to by pressing the STOP key.
4.8
Cooling Time
The cooling time as given in the fitting manufacturer’s instructions has to
be respected. Note that during that time, no external forces must be
applied to the pipe fitting joint which is still warm.
4.9
Returning to the Start of Welding
After welding is finished, disconnecting the welded fitting from the weld-
ing unit will cause the unit to return to the start of welding. An additional
safety feature prevents a given electro fusion fitting from being welded
twice inadvertently: after a properly completed or an aborted welding
operation, the welding unit first has to be disconnected from the fitting
to be ready for the next welding.