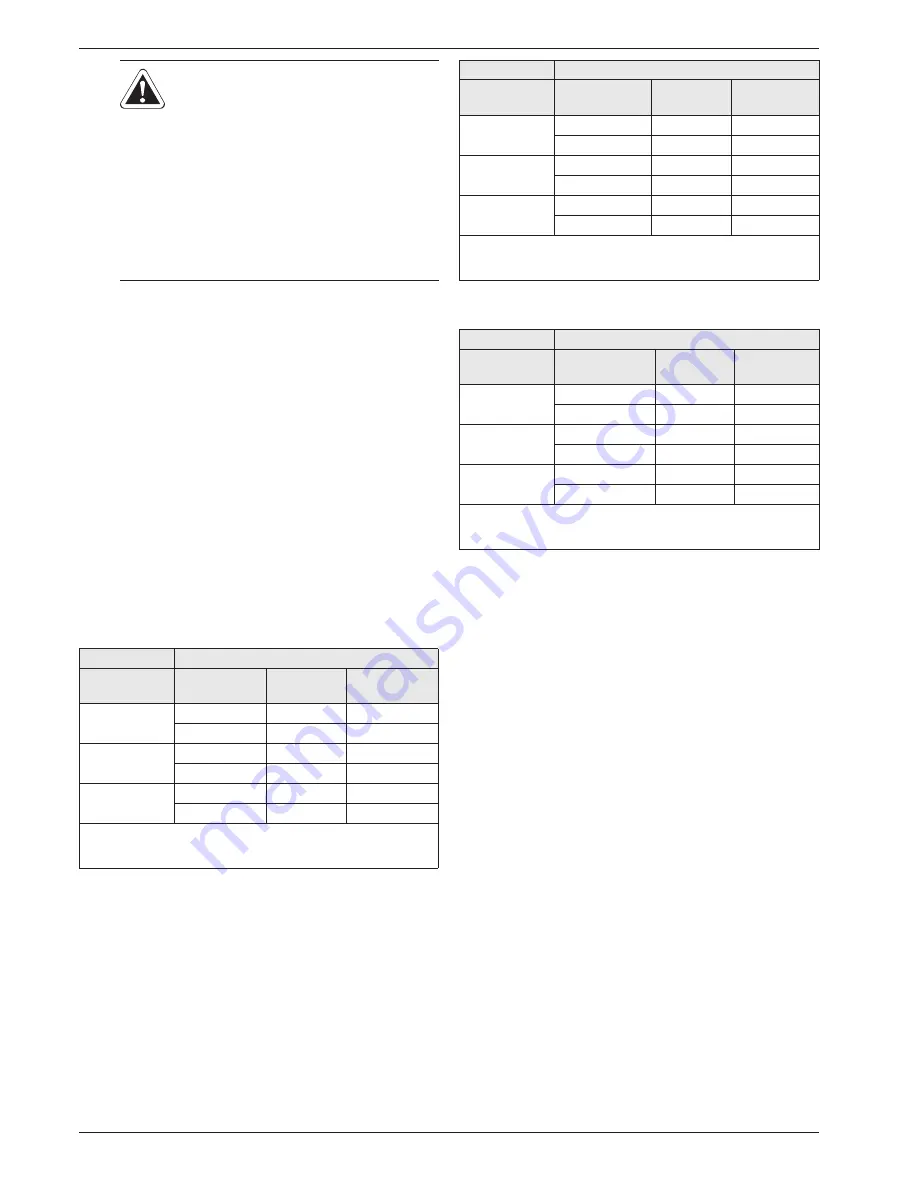
32
ROTEX GCU compact -
5
x
Start-up
6. In the programme [Emission Measurement] select the setting
[Base Load]
(see chapter 15.2),
but do not confirm
.
–
Make sure the heat can dissipate into the heating network
during emission measurement.
Ɣ
Use the flue gas analyser to check the burner settings and
compare them with tab. 5-1 to tab. 5-3.
a) If the O
2
/CO
2
concentrations lie within the permissible
values:
Î
No additional measures are required.
b) If the O
2
/CO
2
concentrations lie outside the permissible
values:
Î
Carry out 100% calibration and adjust the [Drop Io-base]
in such a way that the setting range is reached (see
chapter 7.3.4) and repeat the measurement from step 5.
Ɣ
Document the measured values in the "Installation certifi-
cation" and in the operating manual.
7. End programme [Emission Measurement].
8. Set manual mode from the RoCon BF control (see operating
instructions "RoCon BF Control").
9. Check the resistance in the flue gas line (see chapter 4.5).
5.1.4 After start-up
Ɣ
Mount the sound insulation hood (see chapter 4.4.3).
Ɣ
Check all items on the "Checklist after start-up" (see
section 5.2).
Ɣ
Log the test results on the checklist.
Only when it is possible to answer
all items
on the checklist
with
Yes
, is it allowed to hand over the ROTEX GCU compact
to the operator.
CAUTION!
The firing unit is programmed to take into
account the ageing of the components.
A 100 % calibration of the firing unit can have
a negative impact on the above even if the
exhaust setting values (tab. 5-1 to tab. 5-3) are
adhered to.
Ɣ
Only carry out a calibration of the firing unit
when the exhaust setting values are not
adhered to, or when a mechanical change
was carried out, e.g. by replacing the
component with original ROTEX spare
parts.
Type
GCU compact 315 / 515 (BIV)
Gas type
(Prüfgas)**
Burner load
O
2
-content
in %
CO
2
-content
in %
Natural gas E/H
(G20)
Base Load
4.0 - 5.5
8.6 - 9.5
Full Load
4.0 - 5.4
8.7 - 9.5
Natural gas
LL/L (G25)
Base Load
4.0 - 5.5
8.5 - 9.3
Full Load
4.0 - 5.4
8.5 - 9.3
Propane*
(G31)
Base Load
4.0 - 5.5
10.0 - 11.2
Full Load
4.0 - 5.4
10.2 - 11.2
*
Liquid gas setting
**
Compare with the information on the yellow sticker attached to the burner
housing
Tab. 5-1 Start-up control values for GCU compact 315 and GCU
compact 515 for various gas types
Type
GCU compact 324/ 524 (BIV)
Gas type (test
gas)**
Burner load
O
2
-content
in %
CO
2
-content
in %
Natural gas E/H
(G20)
Base Load
4.0 - 5.5
8.6 - 9.5
Full Load
3.8 - 5.1
9.0 - 9.6
Natural gas
LL/L (G25)
Base Load
4.0 - 5.5
8.5 - 9.3
Full Load
3.8 - 5.1
8.7 - 9.4
Propane*
(G31)
Base Load
4.0 - 5.5
10.0 - 11.2
Full Load
3.8 - 5.1
10.4 - 11.3
*
Liquid gas setting
**
Compare with the information on the yellow sticker attached to the burner
housing
Tab. 5-2 Start-up control values for GCU compact 324 and GCU
compact 524 for various gas types
Type
GCU compact 533 (BIV)
Gas type (test
gas)**
Burner load
O
2
-content
in %
CO
2
-content
in %
Natural gas E/H
(G20)
Base Load
4.0 - 5.5
8.6 - 9.5
Full Load
3.5 - 4.9
9.0 - 9.8
Natural gas
LL/L (G25)
Base Load
4.0 - 5.5
8.5 - 9.3
Full Load
3.5 - 4.9
8.8 - 9.5
Propane*
(G31)
Base Load
4.0 - 5.5
10.0 - 11.2
Full Load
3.5 - 4.9
10.5 - 11.4
*
Liquid gas setting
**
Compare with the information on the yellow sticker attached to the burner
housing
Tab. 5-3 Start-up control values for GCU compact 533 for various gas
types