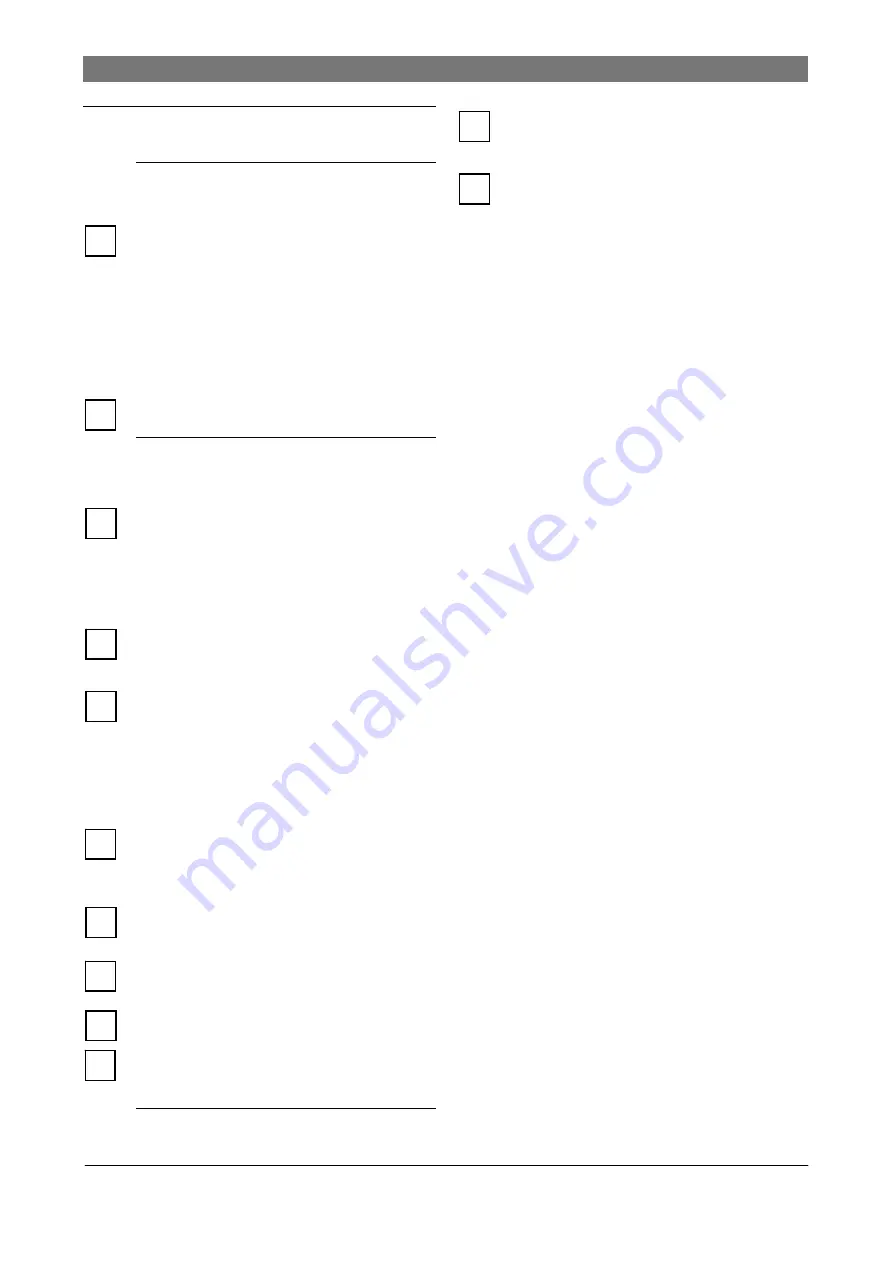
7.
Maintenance
19
117592
●
03/2013
7.
Maintenance
7.1 Maintenance
staff
qualification
Maintenance work may only be carried out by
competent persons (
chapter 1.3). Parts
lists do not act as authorisation for
maintenance or repairs on the lift, unless
otherwise expressly stated in the operating
manual
.
They are only designed to provide
information to the maintenance technician of
the authorised dealer.
Only specialists with specialist knowledge and
experience of hydraulics may work on
hydraulic equipment.
7.2 Safety
regulations
Only OEM parts supplied by authorised
dealers may be used. If these parts are not
used, the manufacturer of the lift shall not
assume any liability and the warranty shall
become null and void. Maintenance and
service work may only be carried out on
equipment which is switched off and locked.
Before any maintenance or adjustments,
disconnect the lift from the power supply. Also
make sure that all mobile components are
securely locked.
Inform everyone in the lift zone of the
maintenance work.
Avoid contact with or inhaling of toxic
substances such as hydraulic fluid, as well as
environmental hazards. If required, wear
protective clothing, e.g. protective goggles,
protective gloves, etc.
After design modifications to or repair of safety-
related parts, the lift must be inspected by a
certified expert.
Before carrying out maintenance work,
display a warning sign and secure the lift
zone with a red-white chain.
Tighten fasteners after maintenance with the
specified torque.
Do not disassemble or modify lift parts – only
maintenance technicians from the authorised
dealer may do so.
Follow the maintenance schedule, document
the maintenance work (
maintenance
report).
7.3 Maintenance
schedule
Lifts in especially dirty environments must be
cleaned and maintained more often.
Oil and grease are water pollutants. Always
dispose of them in an environmentally friendly
manner according to the regulations
applicable in your country (
Chapter 14,
Disposal).
Daily
1. After finishing work, lower the lift fully and lock
to prevent unauthorised use.
2. Clean the lift and the work zone.
3. Check the condition and wear on cables and
sheaves.
4. Check that the latches are not permanently
bent.
Monthly
1. Check the hydraulic oil level (
chapter 7.5).
2. Check the controls for functionality and the
electrical cables for damage.
3. Check the seals on hydraulic components (
chapter 7.7).
4. Carry out a function test with or without load
(
chapter 7.9).
5. Check the tension of the synchronisation
cables.
6. Check whether screws and bolts are secure
Annually
1. Carry out a safety inspection
(
chapter 12).
2. Inspect and if necessary adjust the
synchronisation cables (
chapter 12).
Every 2 years
1. Change the oil (
chapter 7.5).
i
i
i
i
i
i
i
i
i
i
i
i
Summary of Contents for SGL35
Page 2: ......
Page 4: ......
Page 44: ...Diagrams spare parts lists 40 117592 03 2013 Figure 1 ...
Page 45: ...Figure 2 ...
Page 46: ...Diagrams spare parts lists 42 117592 03 2013 Figure 3 Figure 4 ...
Page 47: ...Figure 5 Figure 7 Figure 6 ...
Page 48: ...Diagrams spare parts lists 44 117592 03 2013 Figure 8 ...
Page 49: ...Figure 9 ...
Page 52: ...Diagrams spare parts lists 48 117592 03 2013 ...