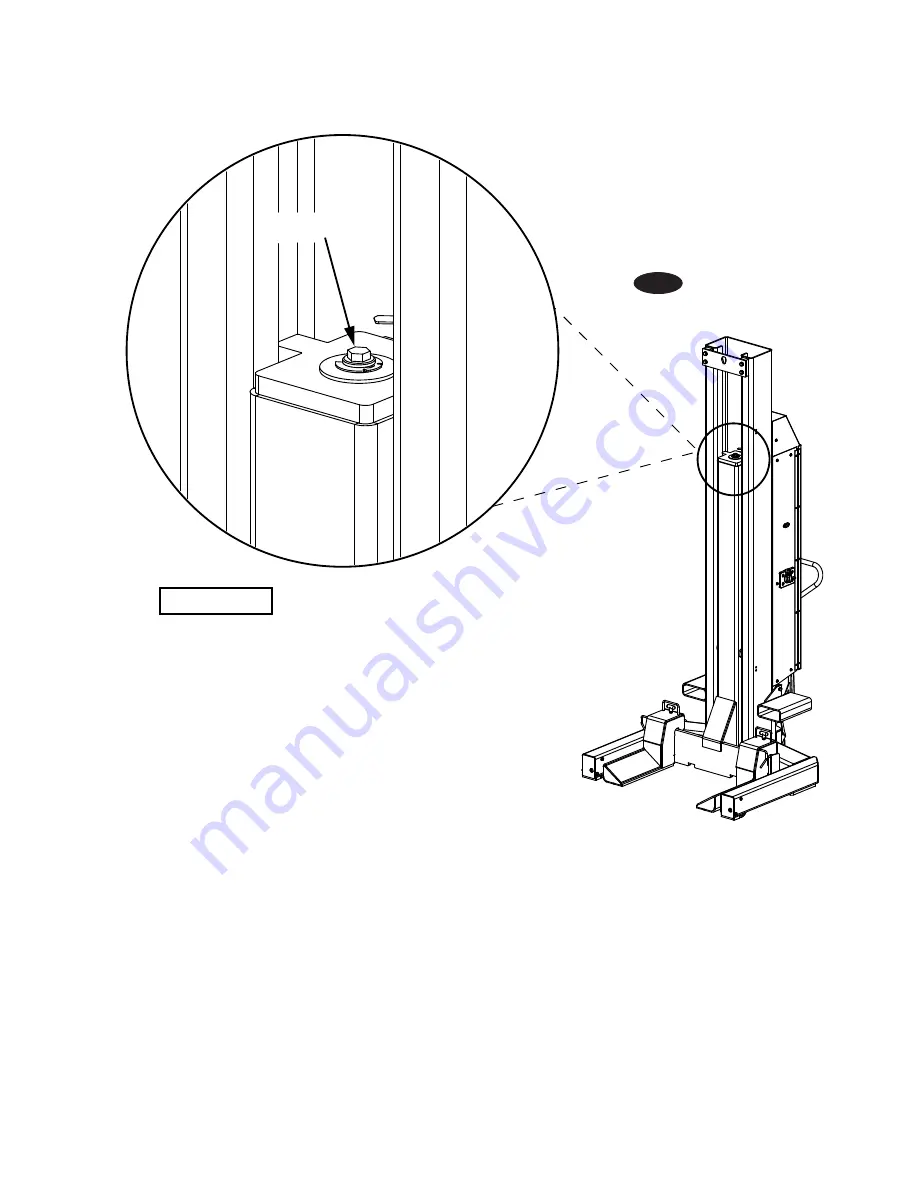
5
12. Bleed mobile columns, Fig. 2b.
a.) Fully raise lift, then lower to just below lowest lock.
b.) Loosen bleed screw to release air from system.
c.) Close screw and repeat steps a and b until there is no air in the system and fluid runs clear.
Bleed Screw
Do Not Exceed Torque Values
On Bleeder Screw
Torque Values: 177-230 In/Lbs (20Nm-26Nm)
IMPORTANT
Fig. 2b
13. Upon completion of the assembly of the lift, the lift is to
be operated to assure proper function. Observe for locks
operating in all locking positions, each side lifts equally,
hydraulics do not leak, all electrical controls function as
labeled, all pneumatics are functional and leak free, ramps
rotate freely (if applicable), and proper clearances with all
items in bay have been maintained.
Operate the lift with a typical vehicle and observe to assure
the same items for proper functioning.