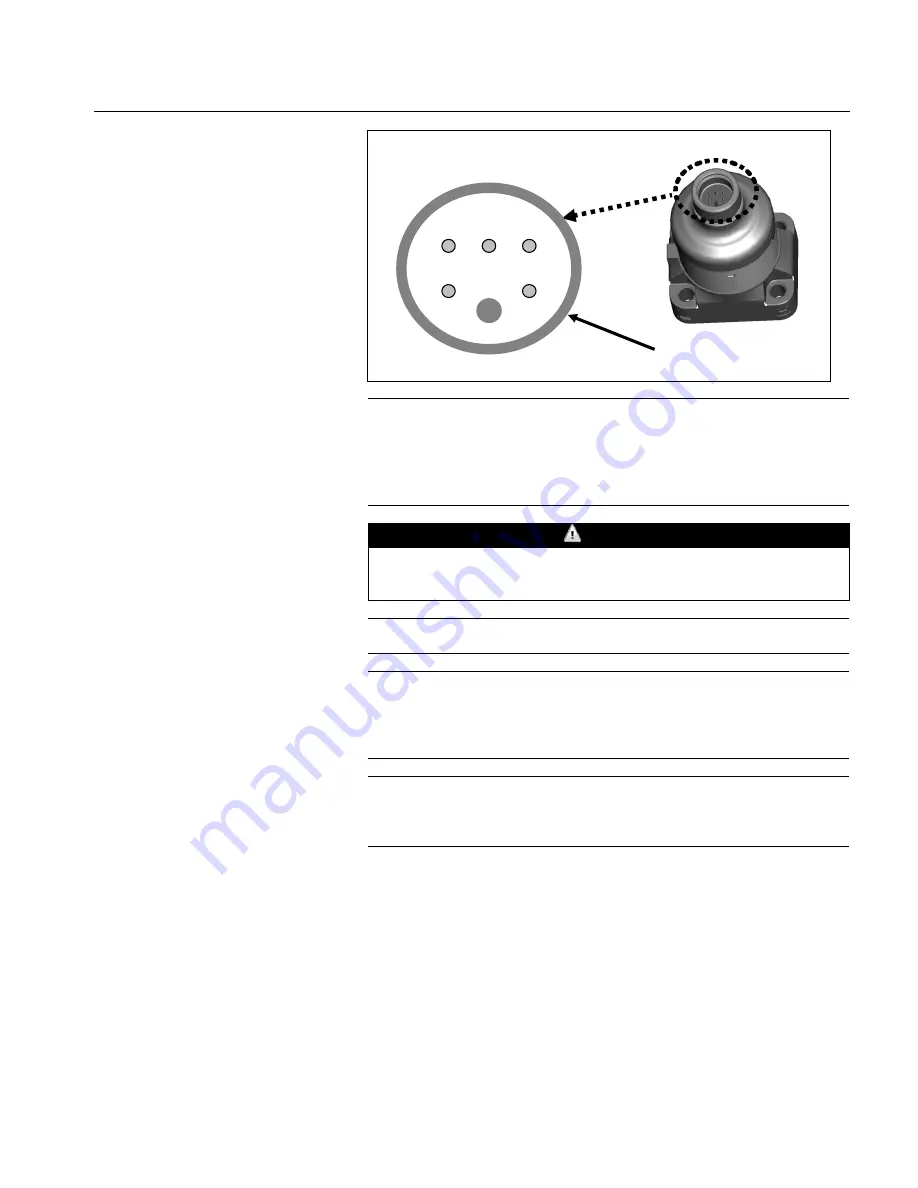
Rosemount 3150 Series
Reference Manual
00809-0100-4835 Rev BD
July 2016
5-7
Figure 5-2 – Sensor Module Pin
Connections
DISSASSEMBLY
PROCEDURE
NOTE
Before removing the transmitter from service:
•
Follow all plant safety rules and procedures.
•
Isolate and vent the process from the transmitter before
removing the transmitter from service.
•
Remove all electrical leads and conduit.
WARNING
Residual process fluid may remain after disassembly of process
flanges. If this fluid is potentially contaminated, take appropriate
safety measures.
NOTE
Numbers in parentheses refer to item numbers in Figure 5-1.
NOTE
3150 Series transmitters contain electronic circuit boards which may
be static sensitive. Therefore, observe proper ESD
precautions/techniques whenever the electronics assemblies are
handled and/or uncovered.
NOTE
Special testing and part replacement are required for reassembly.
Read the
Process Flange Reassembly Procedure
section (see pg.
5-14) before attempting disassembly.
Process Flange Removal
1. Remove the transmitter from service before disassembling
flanges.
2. Remove the two flange cap screws (13).
3. Detach process flange (10) by removing the four large bolts (11).
Take care not to scratch or puncture the isolating
diaphragms.
Identify the orientation of flange with respect to
sensor module for reassembly.
4. Carefully remove the C-rings (9).
Do not reuse C-rings. Take
care not to scratch the sealing surfaces on the process
flange and sensor module.
2
1
3
4
5
MODULE HOUSING
Summary of Contents for 3152
Page 2: ......
Page 6: ...Rosemount 3150 Series Reference Manual 00809 0100 4835 Rev BD July 2016 iv ...
Page 10: ...Rosemount 3150 Series Reference Manual 00809 0100 4835 Rev BD July 2016 1 2 ...
Page 27: ...Reference Manual 00809 0100 4835 Rev BD July 2016 Rosemount 3150 Series 2 17 ...
Page 45: ...Reference Manual 00809 0100 4835 Rev BD July 2016 Rosemount 3150 Series 3 18 ...
Page 51: ...Reference Manual 00809 0100 4835 Rev BD July 2016 Rosemount 3150 Series 4 6 ...
Page 70: ...Rosemount 3150 Series Reference Manual 00809 0100 4835 Rev BD July 2016 5 19 ...